The purpose of the Operation Qualification of Steam sterilizer cum Bung sterilizer protocol is to establish documentary evidence to ensure that the installed Steam sterilizer cum Bung sterilizer will operate reproducibly and consistently within its full dynamic range of operation according to the specifications of the manufacturer.
Related Topic: Installation Qualification of Steam Sterilizer cum Bung Processor (Protocol)
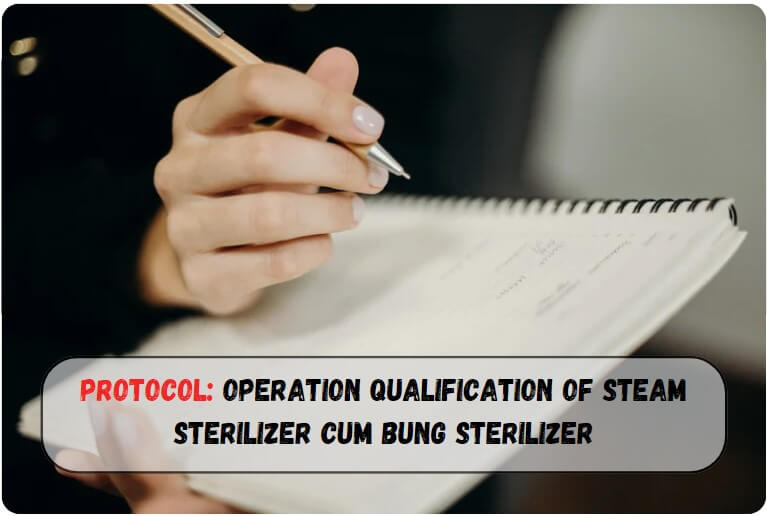
Content of Steam Sterilizer cum Bung Sterilizer OQ Protocol:
SERIAL NO. | ITEM DESCRIPTION |
1.0 | PROTOCOL APPROVAL |
2.0 | OVERVIEW: |
2.1 | Objective |
2.2 | Purpose |
2.3 | Scope |
2.4 | Responsibility |
2.5 | Execution Team |
3.0 | ACCEPTANCE CRITERIA |
4.0 | REVALIDATION CRITERIA: |
5.0 | OPERATIONAL QUALIFICATION PROCEDURE |
5.1 | Equipment Description |
5.2 | Instruction for Filling the Checklist |
5.3 | Verification of Functional Checks |
5.4 | Verification of Key Functionality of Control Panel |
5.5 | Verification of Safety Feature (S) |
5.6 | Verification of Standard Operating Procedure |
5.7 | Training Record Of Personnel (S) |
5.8 | Deficiency And Corrective Action(s) Report(s) |
6. 0 | OPERATIONAL QUALIFICATION FINAL REPORT |
6.1 | Summary |
6.2 | Conclusion |
6.3 | Final Report approval |
1.0 | PROTOCOL APPROVAL: |
This Operational Qualification Protocol of Steam sterilizer cum Bung sterilizer has been reviewed and approved by the following persons:
FUNCTION | NAME | DEPARTMENT | SIGNATURE | DATE |
---|---|---|---|---|
PREPARED BY | QUALITY ASSURANCE | |||
REVIEWED BY | PROJECTS / ENGINEERING | |||
REVIEWED BY | PRODUCTION | |||
APPROVED BY | QUALITY ASSURANCE |
2.0 | OVERVIEW: |
2.1 | OBJECTIVE: |
To perform the Operational Qualification Steam sterilizer cum Bung sterilizer to be used for sterilizing the various types of dry goods products such as filter housing and cartridges, machine parts, textiles, rubber stoppers, products in pouches, products in ampoules or vials, etc. | |
2.2 | PURPOSE: |
The purpose of this protocol is to establish documentary evidence to ensure that the installed Steam sterilizer cum Bung sterilizer will operate reproducibly and consistently within its full dynamic range of operation according to the manufacturer’s specifications. | |
2.3 | SCOPE: |
The Scope of this protocol is limited to the Operational Qualification of Steam sterilizer cum Steam sterilizer cum Bung sterilizer in XYZ Pharmaceuticals. | |
2.4 | RESPONSIBILITY: |
The following shall be responsible; | |
Quality Assurance Officer/Executive | For Preparation of Protocol /Execution Projects. |
Engineering Head | For execution. |
Production Head | For execution support. |
Quality Assurance Head | For adequacy and final approval. |
2.5 | EXECUTION TEAM: |
The execution team is responsible for the execution of this protocol. The execution team comprises of: |
DEPARTMENT | DESIGNATION | NAME | SIGNATURE | DATE |
---|---|---|---|---|
PROJECTS/ ENGINEERING | ||||
PRODUCTION | ||||
QUALITY ASSURANCE |
3.0 | ACCEPTANCE CRITERIA: |
3.1 | The equipment should operate according to its specified operating instructions. |
3.2 | We need to verify and check all standard operating procedures (SOPs) for the equipment. |
3.3 | Training is important to all the concerned personnel. |
3.4 | All MOC of the contact parts are to be checked as per the specifications. |
3.5 | All the functionality of equipment components is to be checked. |
4.0 | REVALIDATION CRITERIA: |
The Steam sterilizer cum Steam sterilizer cum Bung sterilizer has to be revalidated if: | |
💡Any major changes in system components affect the system’s performance. 💡After major breakdown maintenance is carried out. 💡As per the revalidation date and schedule. |
5.0 | OPERATIONAL QUALIFICATION PROCEDURE: |
5.1 | EQUIPMENT DESCRIPTION: |
Equipment Name | Steam sterilizer cum Bung Sterilizer |
Supplier / Manufacturer | Pharmalab |
Dimension Internal (WXHXD mm) | 900 x 900 x 1200 mm |
Volume | 972 liters |
Model | PSSD334AB (H) |
Job no. | 2006127 |
Service it offers | Sterilization of machine parts, rubber stoppers, Garments, etc. |
Steam sterilizer cum Bung sterilizer comprises of following components: |
1. Validation gland adaptor 2. Sampling valve 3. Safety valve 4. Compound pressure gauge 5. 2-Way pneumatic valve 6. Pressure gauge 7. Air pressure switch 8. Air vacuum switch 9. Jacket pressure switch 10. Float-type steam trap 11. Pressure transmitter 12. Vacuum pump 13. Vent filter with housing 14. Air pressure regulator 15. Gasket air pressure regulator 16. Non return valve 17. Needle valve 18. Ball valve 19. Temperature sensor 20. Strainer 21. Solenoid valve 22. Door limit switch 23. Door safety switch 24. Printer 25. Chart recorder 26. Air agitation regulator with gauge 27. Float switch 28. Circulation water pump 29. Recirculation filter with housing 30. Drum motor 31. Dosing pump 32. Control panel |
Steam sterilizer cum Bung processor is designed to sterilize various types of dry goods products such as filter housing and cartridges, machine parts, textiles, rubber stoppers, products in pouches, products in ampoules or vials, etc. |
5.2 | INSTRUCTION FOR FILLING THE CHECKLIST: |
5.2.1 | In case of compliance of the test use the word ‘Complies’ otherwise use ’Does not comply‘ to indicate non-compliance. |
5.2.2 | For identification of the components of the equipment and utilities use the word ‘’yes’’ to show its presence and use ‘No’ to indicate the absence of the identity. |
5.2.3 | Give detailed information in the summary and conclusion part of the Operational Qualification report. |
5.2.4 | Use ‘NA‘ in any column that is blank or not used. |
5.3 | VERIFICATION OF FUNCTIONAL CHECKS: |
NAME OF EQUIPMENT COMPONENT | SPECIFIED FUNCTION | MATCHES WITH THE SPECIFIED FUNCTION (YES / NO) | VERIFIED BY (SIGN) | DATE |
---|---|---|---|---|
1. Validation gland adaptor | ||||
2. Sampling valve | ||||
3. Safety valve | ||||
4. Compound pressure gauge | ||||
5. 2-Way pneumatic valve | ||||
6. Pressure gauge | ||||
7. Air pressure switch | ||||
8. Air vacuum switch | ||||
9. Jacket pressure switch | ||||
10. Float-type pressure switch | ||||
11. Pressure transmitter | ||||
12. Vacuum pump |
13. Vent filter with housing | ||||
14. Air pressure regulator | ||||
15. Gasket air pressure regulator | ||||
16. Non return valve | ||||
17. Needle valve | ||||
18. Ball valve | ||||
19. Temperature sensor | ||||
20. Strainer | ||||
21. Solenoid valve | ||||
22. Door limit switch | ||||
23. Door safety switch | ||||
24. Printer | ||||
25. Chart recorder | ||||
26. Air agitation regulator with gauge | ||||
27. Float switch | ||||
28. Circulation water pump | ||||
29. Recirculation filter with housing | ||||
30. Drum motor | ||||
31. Dosing pump | ||||
32. Control panel |
5.4 | VERIFICATION OF KEY FUNCTIONALITY OF CONTROL PANEL: |
COMPONENT OF CONTROL PANEL | SPECIFIED FUNCTION | MATCHES WITH THE SPECIFIED FUNCTION(YES / NO) | VERIFIED BY(SIGN) | DATE |
1. Main Switch | To start the machine. | |||
2. On-Off switch | The green indicator is for a run of the machine and the red indicator shows that the machine is off. | |||
3. Guard | The machine will trip if the guard is opened. |
5.5 | VERIFICATION OF SAFETY FEATURES: |
SAFETY FEATURES DESCRIPTION | FUNCTION | VERIFIED BY(SIGN) | DATE |
1. Door Safety | The door should not open during the process ON. | ||
2. Emergency off | All output should get off except door gasket sealing if the emergency is pressed. | ||
3. Control temperature sensor faulty. | If there is any problem with the control temperature sensor machine should stop. | ||
4. Chamber safety against overpressure of the steam. | PLC should cut off the steam supply when the steam pressure is over. | ||
5. Jacket safety against overpressure of the steam. | The safety valve should open when the steam pressure is over. | ||
4. Earthing | To avoid electrical shocks due to leakage current. |
5.6 | VERIFICATION OF STANDARD OPERATING PROCEDURE (SOP): |
The following Standard Operating Procedures were verified as important for the effective performance of Steam sterilizer cum Bung sterilizer operation.
Sr. No. | SOP TITLE | SOP NUMBER | VERIFIED BY | DATE |
1. | ||||
2. | ||||
3. | ||||
4. |
5.7 | TRAINING RECORD OF PERSONNEL (S): |
Sr. No. | Name of Personnel | Designation | Sign. & Date | Trained By | Remark |
---|---|---|---|---|---|
1. | |||||
2. | |||||
3. | |||||
4. | |||||
5. |
5.8 | DEFICIENCY AND CORRECTIVE ACTION (S) REPORT (S): |
The following deficiency was identified and corrective actions were taken in consultation with the validation team. |
Description of deficiency: |
Corrective action(s) taken: |
Reviewed By:
Date:
6.0 | OPERATIONAL QUALIFICATION FINAL REPORT: |
The validation team to prepare a summary report shall review all the OQ data sheets and discrepancy reports. The summary of OQ shall be used to draw conclusion for approval of the installation qualification report. |
6.1 | SUMMARY |
6.2 | CONCLUSION |
6.3 FINAL REPORT APPROVAL:
It has been verified that all tests required by the Steam sterilizer cum Bung sterilizer protocol are completed, reconciled, and attached to this protocol or included in the qualification summary report. It verified that all amendments and discrepancies are documented, approved, and attached to this protocol.
The signature in the block below indicates that all items in this qualification report of Steam sterilizer cum Bung sterilizer have been reviewed and found to be acceptable and that all variations or discrepancies have been satisfactorily resolved.
NAME | DESIGNATION | DEPARTMENT | SIGNATURE | DATE |
PROJECTS / ENGINEERING | ||||
PRODUCTION | ||||
QUALITY ASSURANCE |
Related Topics:
- Installation Qualification of Steam Sterilizer cum Bung Processor (Protocol)
- Auto Coater Installation Qualification Protocol/ Annexures
- Auto Coater Operational Qualification Protocol/ Annexures
- Auto Coater Performance Qualification Protocol
- Blender Installation Qualification Protocol/ Annexures
- Blender Performance Qualification Protocol/ Annexures
- Blister Machine Operation Qualification Protocol/ Annexures
- Design Qualification in Pharmaceutical Industry
- Design Qualification of Electric Stacker
- Design Qualification Protocol for Vertical Laminar Reverse Flow
- Installation Qualification Protocol for Automatic Capsule Filling Machine
- Installation Qualification Protocol for Blister Packing Machine with Annexures

Naresh Bhakar is the Founder and Author at Pharmaguddu.com, bringing his extensive expertise in the field of pharmaceuticals to readers worldwide. He has experience in Pharma manufacturing and has worked with top Pharmaceuticals. He has rich knowledge and provides valuable insights and data through his articles and content on Pharmaguddu.com. For further inquiries or collaborations, please don’t hesitate to reach out via email at [email protected].