The purpose of the Installation Qualification of Steam Sterilizer cum Bung Processor protocol is to establish documentary evidence to ensure that it received matches the Design specification and also to ensure that it is properly and safely installed.
💡Related Topics: Area Qualification Protocol in Pharmaceuticals
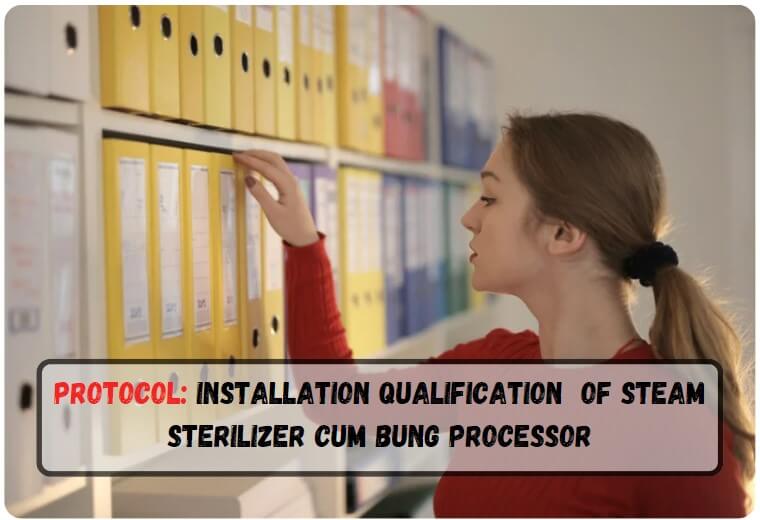
Protocol Contents for Steam Sterilizer cum Bung Processor IQ:
SERIAL NO. | ITEM DESCRIPTION |
1.0 | PROTOCOL APPROVAL |
2.0 | OVERVIEW: |
2.1 | Objective |
2.2 | Purpose |
2.3 | Scope |
2.4 | Responsibility |
2.5 | Execution Team |
3.0 | ACCEPTANCE CRITERIA |
4.0 | REVALIDATION CRITERIA |
5.0 | INSTALLATION QUALIFICATION PROCEDURE |
5.1 | System Description |
5.2 | Instruction for Filling the Checklist |
5.3 | Installation Check-List |
5.4 | Identification Of Major Components |
5.5 | Verification of material of construction |
5.6 | Identification of Supporting Utilities. |
5.7 | Identification Of Safety Feature(s) |
5.8 | Identification of standard operating procedure |
5.9 | Identification Of Component to be Calibrated |
5.10 | Verification of Drawings and Documents |
5.11 | Abbreviations |
5.12 | Deficiency And Corrective Action(s) Report(s) |
5.13 | Annexure(s) |
6.0 | INSTALLATION QUALIFICATION FINAL REPORT |
6.1 | Summary |
6.2 | Conclusion |
6.3 | Final report approval |
1.0 | PROTOCOL APPROVAL: |
When signing this approval Protocol, it shows that you agree with the qualification approach described in this document. If a modification to the qualification approach is necessary, it shall be prepared and approved as an addendum. The protocol cannot be used for execution unless the following authorities approve it.
This Installation Qualification protocol for Steam Sterilizer cum bung processor has been reviewed and approved by the following persons:
FUNCTION | NAME | DEPARTMENT | SIGNATURE | DATE |
---|---|---|---|---|
PREPARED BY | QUALITY ASSURANCE | |||
REVIEWED BY | PROJECTS / ENGINEERING | |||
REVIEWED BY | PRODUCTION | |||
APPROVED BY | QUALITY ASSURANCE |
2.0 | OVERVIEW: |
2.1 | OBJECTIVE: |
The objective of developing and executing this protocol is to collect sufficient data pertaining to the Steam Sterilizer cum bung processor and define the qualification requirements and acceptance criteria for the unit. Successful completion of these qualification requirements will provide assurance that the Steam Sterilizer cum bung processor was installed as required in the manufacturing area. | |
2.2 | PURPOSE: |
The purpose of this protocol is to establish documentary evidence to ensure that the Steam Sterilizer cum bung processor received matches the Design specification and also to ensure that it is properly and safely installed. | |
2.3 | SCOPE: |
This Protocol is applicable to the installation of a Steam Sterilizer cum bung processor at the tablet manufacturing facility in XYZ Pharmaceutical & the subsequent documentation. | |
2.4 | RESPONSIBILITY: |
The following shall be responsible; Quality Assurance officer / Executive – For preparation of protocol / Execution Projects / Engineering Head – For execution Production Head – For execution support Quality Assurance Head – For adequacy and final approval. |
2.5 | EXECUTION TEAM: |
The satisfactory installation of the Steam Sterilizer cum bung processor shall be verified by executing the qualification studies described in this protocol. The successfully executed protocol documents that the Steam Sterilizer cum bung processor is installed and is satisfactorily integrated. The execution team is responsible for the execution of the installation of the Steam Sterilizer cum bung processor. The execution team comprises of: |
DEPARTMENT | DESIGNATION | NAME | SIGNATURE | DATE |
PROJECTS / ENGINEERING | ||||
PRODUCTION | ||||
QUALITY ASSURANCE |
3.0 | ACCEPTANCE CRITERIA: |
3.1 | The equipment shall fulfill all the selection criteria and its individual application. |
3.2 | The equipment shall comply with the specification mentioned in the user requirement specification. |
3.3 | It shall be complying with all the designed specifications. |
3.4 | The Material Of Construction (MOC) shall comply with the specification. |
3.5 | All supporting electric and non-electric utilities of specified capacities are to be near the place of installation. |
4.0 | REVALIDATION CRITERIA: |
The machine has to be revalidated if: | |
💡 There are any major changes in system components, that affect the performance of the system. 💡 After major breakdown maintenance is carried out. 💡 As per the revalidation date and schedule. |
5.0 | INSTALLATION QUALIFICATION PROCEDURE: | ||
5.1 | SYSTEM DESCRIPTION: |
The Principle of Steam Sterilizer cum bung processor is designed for steam sterilization of various types of dry goods products such as machine parts, garments, rubber stoppers, media fills, components and pressure vessels, etc.
Sterilizer is designed for moist heat sterilization by using pure steam. Sterilizer designed by completely PLC operated with manual override in case of emergency. PLC is equipped with different cycles as per the requirements of the material i.e. for sterilization of garments, sterilization of empty glass flasks, rubber stoppers, machine parts, media for process simulation, and components the system description is divided into the following sections:
General, Technical summary along with Mechanical Construction, Design and Manufacturing Process, Control System, Cycle Operation, Documentation, Maintenance and recommended spare parts, Troubleshooting, etc.
The action of steam sterilizer on all the materials placed within the chamber is that the steam penetrates into the microorganisms present on and within the material thereby transferring the latent steam, which in turn will coagulate with the proteins, imparting a lethal effect on the organism, which will lead to the destruction of the organism.
The steam sterilizer is made up of an SS sheet which is welded with a U-profile SS jacket. The sterilization chamber is provided with two vertical sliding doors which are also made up of SS reinforced with MS support structure. The door is operated with the help of pneumatic cylinders. When both door reaches at the end position the gaskets are pushed out automatically with the help of compressed air ejectors. When the gaskets retract the sterilizer chamber door slides automatically. The door sealing is made effective with the help of a tubular silicon rubber gasket. To ensure proper sealing the gaskets are activated with compressed air and retracted with the help of vacuum.
The sterilization chamber is insulated with resin-bonded glass wool, which helps in reducing the heat loss to the environment and ensures uniform distribution of temperature inside the chamber. This insulation is cladded with SS cover plate.
To ensure a leak-tight partition between the Sterile area (Class A unloading side) and the loading side an SS flush panel is provided on the partition wall and the outer cover of the steam sterilizer. All the joints, crevices are filled with silicon sealant to prevent leakages. The autoclave holds the vacuum with a rate of NMT 13 mbar per 10 minutes. All the automatic valves are closed when the autoclave chamber is at the ambient pressure. During the vacuum cycle except the vacuum valve, all other valves are closed.
The sterilizing grade filter is placed in a class A environment and connected to a chamber for the purpose of vacuum break. The filter is suitable for integrity testing and steam sterilization. Both the vertical sliding doors have an interlocking system in which the door does not open simultaneously. The doors do not open in any case during sterilization. The steam sterilizer has the ability to stand with a maximum of 3.0 kg /cm2 pressure. The steam sterilizer has a safety valve, which will blow off if 0.5 kg/cm2 exceeds than the working pressure. The system has an emergency stop so as to stop all the physical movement and operation of the machinery immediately, which is located along with the control panel.
5.2 | INSTRUCTION FOR FILLING THE CHECKLIST |
5.2.1 | In case of compliance of the test use the word ‘Complies’ otherwise use ‘Does not comply‘ to indicate non-compliance. |
5.2.2 | For identification of the components of the equipment and utilities use the word ‘’yes’’ to show its presence and use ‘No’ to indicate the absence of the identity |
5.2.3 | Give detailed information in the summary and conclusion part of the Installation Qualification report. |
5.2.4 | Whichever column is blank or not used ‘NA’ shall be used. |
5.3 | INSTALLATION CHECKLIST: |
The installation checklist is as follows: |
Sr. NO. | STATEMENT | YES / NO | CHECKED BY (SIGN) | DATE |
---|---|---|---|---|
01 | Safety valve for chamber | |||
02 | Safety valve for jacket | |||
03 | Air pressure regulator | |||
04 | Gasket air pressure regulator | |||
05 | Air pressure switch | |||
06 | Gasket vacuum switch | |||
07 | Vacuum valve | |||
08 | Pure steam supply | |||
09 | Sealing water for vacuum pump | |||
10 | Compressed air supply | |||
11 | Header outlet (Drain connection) | |||
12 | Chamber vacuum line | |||
13 | Validation probe | |||
14 | WFI (Distilled water) | |||
15 | Purified water | |||
16 | Detergent Solution | |||
17 | Silicon solution | |||
18 | Air heater nozzle & piping connection | |||
19 | Electric power supply | |||
20 | Electric connection between power & Control panel etc. | |||
21 | Pneumatic instruments tubing | |||
22 | Pneumatic connection leakages | |||
23 | Duct flanges bolted connections | |||
24 | System interlock functioning | |||
a) Emergency | ||||
b) Air pressure low | ||||
c) Power failure | ||||
d) Door open temperature not reached | ||||
e) Sterile or non-sterile door open | ||||
f) Control temperature sensor faulty | ||||
i) Final vacuum problem | ||||
g) Door Between | ||||
h) Initial vacuum problem | ||||
j) Preheating temperature problem | ||||
k) Pressure release problem | ||||
l) Vacuum release problem | ||||
m) Gasket release problem | ||||
n) Sterile temperature problem | ||||
o) Chamber pressure high | ||||
p) Water level problem | ||||
25 | Properly Mounted and Supported | |||
26 | Properly labeled and identified |
5.4 | IDENTIFICATION OF MAJOR COMPONENTS: |
Describe each critical component and check them and fill out the inspection checklist. |
System Components | Design Specification | Complies / Does Not Comply | Checked By(Sign) | Date |
---|---|---|---|---|
1) Validation gland adaptor | Size – 2” Triclover | |||
No of holes – 8 nos. | ||||
Gland – Silicon | ||||
Gland diameter – 6MM | ||||
MOC – SS 316L | ||||
Make – Pharmalab | ||||
Qty – 02 | ||||
Location 1 – At the left side of chamber | ||||
Location 2 – At the right side of chamber | ||||
2) Sampling valve | Size – 25 MM | |||
MOC – SS 316L | ||||
Diaphragm – Silicon | ||||
Operation – Manual | ||||
Make – Pharmalab | ||||
Qty – 01 | ||||
Location – Chamber condensate line | ||||
3) Safety valve | Size – ¾” BSP female | |||
MOC – SS 316L | ||||
Make – Shakti | ||||
Range – 0 – 43 PSI | ||||
Type – Spring loaded | ||||
Qty – 02 | ||||
Location 1 – on the chamber | ||||
Location 2 – on the jacket | ||||
4) Compound pressure gauge | Dial size – 4” | |||
Range – -1 to 3.5 kg/cm2 | ||||
Make – Waree | ||||
Mounting – Panel mounting | ||||
End connection – 3/8” BSP | ||||
MOC – Body: SS304Movement: SS304Burden socket: SS316L | ||||
Type – Analogue | ||||
Qty – 02 | ||||
Location 1 – on front facia at sterile side | ||||
Location 2 – on front facia at non-sterile side | ||||
5) Compound pressure gauge | Dial size – 2 – ½” | |||
Range – -1 to 3.5 kg/cm2 | ||||
Make – Warre | ||||
Mounting – Panel mounting | ||||
End connection – ¼” BSP | ||||
MOC – Body: SS304 Movement: SS304 Burdon socket:SS316L | ||||
Type – Analogue | ||||
Qty – 02 | ||||
Location 1 – On front facia at non-sterile side | ||||
Location 2 – On front facia at non-sterile side | ||||
6) 2 Way pneumatic valve | Make – Micro pneumatics | |||
Model – 2 way, 3 p/c | ||||
MOC of working parts- SS 316L | ||||
MOC of the body – SS 316 | ||||
Type–ball valve with full bore | ||||
Size – ½” | ||||
Seal – P.T.F.E | ||||
Actuator – single acting (spring return) | ||||
Operation – pneumatically operated | ||||
Solenoid valve – 24 V AC | ||||
Qty – 08 | ||||
Location 1 – At the venting line | ||||
Location 2 – At the vacuum break line | ||||
Location 3 – At the side drain line | ||||
Location 4 – At the side drain bypass line | ||||
Location 5 – At the air agitation line | ||||
Location 6 – At the side spray line | ||||
Location 7 – At the silicon line | ||||
Location 8 – At the detergent line | ||||
7) 2 Way pneumatic valve | Make – Micro pneumatics | |||
Model – 2 way, 3 p/c | ||||
MOC of working parts- SS 316L | ||||
MOC of the body – SS 316 | ||||
Type–ball valve with full bore | ||||
Size – 1” | ||||
Seal – P.T.F.E | ||||
Actuator – single-acting | ||||
(spring return) | ||||
Operation – pneumatically operated | ||||
Solenoid valve – 24 V AC | ||||
Qty – 10 | ||||
Location 1 – Steam inlet to chamber | ||||
Location 2 – Steam inlet to jacket | ||||
Location 3 – At the chamber condensate line | ||||
Location 4 – At the chamber vacuum line | ||||
Location 5 – At the steam agitation line | ||||
Location 6 – At the drain line | ||||
Location 7 – At the main drain line | ||||
Location 8 – At the water recirculation line | ||||
Location 9 – At the D.M. water inlet line | ||||
Location 10 – At the distilled water inlet line | ||||
8) Pressure gauge | Dial size – 4” | |||
Range – 0 to 4.2 kg/cm2 | ||||
Make – Warre | ||||
Mounting – Panel mounting | ||||
End connection – 3/8” BSP | ||||
MOC – Body: SS3304Movement: SS304Burden socket: SS316L | ||||
Type – Analogue | ||||
Qty – 02 | ||||
Location 1 – Panel mount at the sterile side | ||||
Location 2 – Panel mount at the non-sterile side | ||||
9) Air pressure switch | Make – Orion | |||
Model – MGH07CB10 | ||||
Range – 0.5 to 7 kg/cm2 | ||||
Diff. pressure – 0.4 kg/cm2 | ||||
MOC – Brass | ||||
Diaphragm – Teflon | ||||
Qty – 01 | ||||
Location – On the outlet of the air pressure regulator | ||||
10) Air vacuum switch | Make – Orion | |||
Model – MNV00CB11 | ||||
Range –100 to 750mm of hg | ||||
Diff. pressure – 100 mm of hg | ||||
MOC – Brass | ||||
Diaphragm – Teflon | ||||
Qty – 02 | ||||
Location 1 – Door -1 gasket vacuum line | ||||
Location 2 – Door – 2 gasket vacuum line | ||||
11) Jacket pressure switch | Make – Orion | |||
Model – MAH03CS10 | ||||
Range – 0.2 to 2.6 kg/cm2 | ||||
Diff. pressure – 0.2 to 1.5 kg/cm2 | ||||
Test pressure – 12 kg/cm2 | ||||
End connection – ¼” BSP female | ||||
Qty – 01 | ||||
Location – On the jacket | ||||
12) Float-type steam trap | Size – 15NB | |||
Model – FT-14CI-10 | ||||
Make – Spirax | ||||
Type – Balanced pressure thermostatic trap | ||||
Max. Working pressure – 13 kg/cm2 | ||||
Max working temperature – 120c | ||||
MOC – body: C.I.Cover: C.I. Valve seat: SS 410 | ||||
Qty – 02 | ||||
Location 1 – chamber condensate line | ||||
Location 2 – jacket condensate line | ||||
13) Pressure transmitter | Make – Keller | |||
Model – 23 R | ||||
MOC – SS 316L | ||||
Range – -1 to 3 kg/cm2 | ||||
Mounting – direct mounting | ||||
Output – 4 to 20 mA | ||||
Qty – 01 | ||||
Location – On the chamber | ||||
14) Vacuum pump | Make – Vindivac | |||
Model – RTZ, 3HP | ||||
RPM – 2850 | ||||
Vacuum capacity – 710 mm of hg | ||||
Flow rate – 50 M3 /hr | ||||
Qty – 01 | ||||
Location – Service floor | ||||
15) Vent filter with housing | Housing model – ZLK9010G23H4 | |||
Model – SLK7002PFRP | ||||
Rating – 0.2 micron | ||||
Make – Pall | ||||
Filter length – 5” | ||||
Medium – PTFE | ||||
MOC – SS316L | ||||
Housing gasket – Silicon | ||||
Qty – 01 | ||||
Location – at the sterile side in the vacuum break line | ||||
16) Air pressure regulator | Make – Festo / SMC | |||
Model – ¼” | ||||
Size – ¼” mm | ||||
Qty – 01 | ||||
Location – Main airline | ||||
17) Gasket air pressure regulator | Model – ¼” | |||
Make – Festo / SMC | ||||
Size – ¼” | ||||
Qty – 01 | ||||
Location – air gasket sealing line | ||||
18) Non return valve | Make – VB | |||
Size – 25mm | ||||
MOC – SS316L | ||||
Qty – 01 | ||||
Location – at the chamber vacuum line | ||||
19) Needle valve | Make – shakti | |||
Size – ½” BSP female | ||||
MOC – SS316L | ||||
Qty – 01 | ||||
Location – at the chamber condensate bypass line | ||||
20) Ball valve | Size – 3/8” | |||
Model – 3 piece | ||||
MOC – SS316L | ||||
Qty – 02 | ||||
Location 1 – at the jacket condensate bypass line | ||||
Location 2 – at the side of the chamber for sampling | ||||
21) Temperature sensor | Make – techno | |||
Class – A | ||||
MOC – SS316L | ||||
Seath size – 4.5 mm | ||||
Length of seath – 55mm | ||||
Range – 0degree – 200 degree | ||||
Type – PT 100 | ||||
Element – Dual | ||||
Qty – 05 | ||||
Connection – Triclover | ||||
Location 1 – at the chamber condensate line | ||||
Location 2 – at the left side of the chamber – top | ||||
Location 3 – at the left side of the chamber – bottom | ||||
Location 4 – at the right side of the chamber – top | ||||
Location 5 – at the right side of the chamber – bottom | ||||
22) Strainer | Make – Shakti / karan | |||
MOC – SS304 | ||||
Size – ½” BSP female | ||||
Qty – 02 | ||||
Location 01 – at the chamber condensate line | ||||
Location 02 – at the jacket condensate line | ||||
23) Solenoid valve | Size – ¼” BSPF | |||
Make – SMC / Aira | ||||
Volt – 24V AC | ||||
MOC – Brass | ||||
Qty – 05 | ||||
Location 1 – at the inlet of the vacuum pump | ||||
Location 2 at the door – 1 gasket seal line | ||||
Location 3 – at the door –2 gasket seal line | ||||
Location 4 – at the door – 1 gasket vacuum line | ||||
Location 5 – at the door – 2 gasket vacuum line | ||||
24) Door limit switch | Model – JLSL – 2 | |||
Make – Jay Balaji | ||||
Contact – 1 NO + 1 NC | ||||
Qty – 04 | ||||
Location 1 – at the sterile side door open the position | ||||
Location 2 – at the sterile side door close the position | ||||
Location 3 – at the non-sterile side door open position | ||||
Location 4 – at the non-sterile side door close the position | ||||
25) Door safety switch | Model – JLSPBA | |||
Make – Jay Balaji | ||||
Contact – 1 NO + 1 NC | ||||
Qty – 04 | ||||
Location 1 – on the sterile side door | ||||
Location 2 – on the sterile side door | ||||
Location 3 – on non-side door | ||||
Location 4 – on the non-sterile side door | ||||
26) Printer | Model – LX 300 | |||
Make – Epson | ||||
Type – Dot matrix | ||||
Qty – 01 | ||||
Location – at the bottom box of the control panel | ||||
27) Chart recorder | Model – 4102M | |||
Type – 6 points strip chart recorder | ||||
Input – channel –1pressure 0 to 10mv | ||||
Channel–2 Temperature, PT-100 | ||||
Channel–3 Temperature, PT-100 | ||||
Channel–4 Temperature, PT-100 | ||||
Channel–5 Temperature, PT-100 | ||||
Channel–6 Temperature, PT-100 | ||||
Make – Eurotherm | ||||
Qty – 01 | ||||
Location – on the paneling of non-sterile side | ||||
28) Air agitation regulator with gauge | Model – ½” | |||
Make – Festo / SMC | ||||
Size – ½” | ||||
Qty – 01 | ||||
Location – air agitation line | ||||
29) Float switch | Type – magnetic | |||
Temp. range – 150 deg. C | ||||
MOC – SS316L | ||||
Make – Mahalakshmi/ crystal /punetectrol | ||||
Qty – 01 | ||||
Location – at the side of the chamber | ||||
30) Circulation water pump | Model – CHI-2-50 | |||
Make – Grundfos | ||||
MOC – SS316L | ||||
Gasket – EPDM | ||||
Qty – 01 | ||||
Location – recirculation water line | ||||
31) Recirculation filter with housing | Filter size – 40 microns | |||
Type – Wire mesh | ||||
Filter length – 10” (INCH) | ||||
Gasket – silicon | ||||
Water flow rate – 2.5 to 3 CMH | ||||
Make–Tec fill | ||||
Housing MOC – SS316L | ||||
Qty – 01 | ||||
Location – recirculation water line | ||||
32) Drum motor | Type – Geared motor flange mounted | |||
HP – 0.75 | ||||
RPM – 16 | ||||
Service factor – 2.1 | ||||
Shaft diameter – 44 MM | ||||
Frame size – NZ 3 90 L 8 | ||||
Make – Remi | ||||
Qty – 01 | ||||
Location – on the chamber | ||||
33) Dosing pump | Model – HC-100-04-05 | |||
Type – Metering | ||||
Diaphragm – Electronics | ||||
Flow rate – 4LPH@ 5 Bar Pressure | ||||
Make – AQUA | ||||
Qty – 02 | ||||
Location 1 – at the inlet of the silicon line | ||||
Location 2 – at the inlet of the detergent line | ||||
34) Control panel | Model – automatic with manual operation facility in case of PLC failure | |||
Enclosure – SS 304,1.6 mm thick with polycarbonate cover on MMI | ||||
Panel location – 2 meters away from the machine | ||||
Size in mm – approx 400 D X 1500 H | ||||
PID controller – Model: MC5438 / P48UMake : Max-thermo / Radix | ||||
PLC – Mitsubishi | ||||
MMI – Beijer | ||||
Temperature transmitter – Range: 0 to 200 deg CMake: RadixQty: 05 nos. | ||||
Transformer – Bhatt Magnetic / Narmada | ||||
3 pole rotary switch – sulzer | ||||
Overload relay – L&T | ||||
ELCB + MCB – Hagger / Datar | ||||
Signal distributor – Radix | ||||
Contactor – L& T | ||||
MCB – 3 Pole – Hagger / Indfoss / Datar | ||||
6-channel relay module – Phonix / Brisk | ||||
D.C. source – Meanwell | ||||
2 way 4 pole switch – Sulzer |
Sr. No. | Component | Material of Construction | Method of verification | Checked By Sign / Date | ||
1. | Chamber 6mm Thick plate | SS 316 L | Visually with test certificate | |||
2. | Jacket shell 10SWG sheet | SS 316 L | Visually with test certificate | |||
3. | Door 14 mm thick plate | SS 316 L | Visually with test certificate | |||
4. | 10 x10 mm SQ. Bar for jacket | SS 316 L | Visually with test certificate | |||
5. | Chamber 1” DIA ROD | SS 316 L | Visually with test certificate | |||
6. | Baffel plate 16 SWG sheet | SS 316 L | Visually with test certificate | |||
7. | 25 mm OD x 2 mm thick plate | SS 316 L | Visually with test certificate | |||
8. | 6 mm OD x 1 mm thick pipe | SS 316 L | Visually with test certificate | |||
9. | ¾” OD 16 SWG WT pipe | SS 316 L | Visually with test certificate | |||
10. | Ø12.7 mm x 1 mm WT pipe | SS 316 L | Visually with test certificate |
5.6 | IDENTIFICATION OF SUPPORTING UTILITIES: |
UTILITY | PROPERLY IDENTIFIED & CONNECTED (YES/NO) | CHECKED BY (SIGN) | DATE |
---|---|---|---|
1) Electricity: Specification: 415 V, 3 Ph. 50 Hz Requirement: 5 KW | |||
2) Pure steam supply Specification: 3 kg/cm² pressure dry and saturated pure steam Consumption: = 120 kg / Hr. | |||
3) Compressed Air Supply Specification: Dry, clean, and Filtered at 8 kg/cm² minimum pressure Requirement: 8 CFM |
5.7 | IDENTIFICATION OF SAFETY FEATURES: |
Identify and record the safety features (if any) and their function in the following tables: |
Safety Features Description | Function | Identified By (Sign) | Date |
---|---|---|---|
1) Door Safety | In case of door open | ||
2) Emergency off, if activated stops the process | For Equipment & Operator Safety | ||
3) Control temperature sensor faulty | Process will stop | ||
4) Chamber safety against overpressure of the steam | The safety valve will open at 2.2 kg/cm2 pressure. PLC will cut off the steam supply control valve when the steam pressure in the chamber reaches at 2.2 kg/cm2 and the venting valve will get open to release the chamber pressure. | ||
5) Jacket safety against overpressure of the steam | Safety valve open at 2.2 kg/cm2 pressure Jacket pressure switch |
5.8 | IDENTIFICATION OF STANDARD OPERATING PROCEDURE (SOP): |
The following Standard Operating Procedures were identified as important for the effective performance of the Steam sterilizer cum bung processor. | |
1 | Operation and cleaning of Steam sterilizer cum bung processor |
2 | Preventive maintenance of Steam sterilizer cum bung processor |
5.9 | IDENTIFICATION OF COMPONENT TO BE CALIBRATED |
1. Pressure gauge 2. Temperature sensors 3. Temperature transmitter |
5.10 | VERIFICATION OF DRAWING AND DOCUMENTS: |
The following documents are reviewed and attached as listed below: |
Sr. No. | DRAWING AND DOCUMENT DETAIL | CHECKED BY (SIGN) | DATE |
5.11 | ABBREVIATIONS: |
Following Abbreviations are used in the installation qualification protocol of Steam sterilizer cum bung processor. | |
P & I: Piping and instrumentation PLC: Programmable logic controller S.S: Stainless steel SSB: Steam sterilizer cum bung processor |
5.12 | DEFICIENCY AND CORRECTIVE ACTION (S) REPORT (S): |
The following deficiency was identified and corrective actions were taken in consultation with the validation team. |
Description of deficiency: |
Corrective action(s) taken: |
Reviewed By:
Date:
5.13 | ANNEXURES |
Following Annexures are used in the installation qualification protocol of Steam sterilizer cum bung processor. |
Sr.No. | Annexure No. | Title of Annexure |
6.0 | INSTALLATION QUALIFICATION FINAL REPORT: |
All the IQ data sheets and discrepancy reports shall be reviewed by the validation team to prepare a summary report. The summary of IQ shall be used to draw a conclusion for approval of the installation qualification report. |
6.1 | SUMMARY |
6.2 | CONCLUSION |
6.3 FINAL REPORT APPROVAL
All tests required by this protocol have been verified as completed, reconciled, and attached to this protocol or included in the qualification summary report. It has been verified that all amendments and discrepancies are documented, approved, and attached to this protocol.
The signature in the block below indicates that all items in this qualification report of Steam sterilizer cum bung processor have been reviewed and found to be acceptable and that all variations or discrepancies have been satisfactorily resolved.
NAME | DESIGNATION | DEPARTMENT | SIGNATURE | DATE |
---|---|---|---|---|
PROJECTS / ENGINEERING | ||||
PRODUCTION | ||||
QUALITY ASSURANCE |
Related Topics:
- Auto Coater Installation Qualification Protocol/ Annexures
- Auto Coater Operational Qualification Protocol/ Annexures
- Auto Coater Performance Qualification Protocol
- Blender Installation Qualification Protocol/ Annexures
- Blender Performance Qualification Protocol/ Annexures
- Blister Machine Operation Qualification Protocol/ Annexures
- Design Qualification in Pharmaceutical Industry
- Design Qualification of Electric Stacker
- Design Qualification Protocol for Vertical Laminar Reverse Flow
- Installation Qualification Protocol for Automatic Capsule Filling Machine
- Installation Qualification Protocol for Blister Packing Machine with Annexures

Naresh Bhakar is the Founder and Author at Pharmaguddu.com, bringing his extensive expertise in the field of pharmaceuticals to readers worldwide. He has experience in Pharma manufacturing and has worked with top Pharmaceuticals. He has rich knowledge and provides valuable insights and data through his articles and content on Pharmaguddu.com. For further inquiries or collaborations, please don’t hesitate to reach out via email at [email protected].