Operational Qualification of the Automatic Capsule Filling Machine is done to get sufficient information and data about the machine and define the qualification and acceptance criteria to show that each criteria is proceed as per the Design specifications. Once the OQ is completed then, the equipment shall proceed to the next stage.
Related: Installation Qualification Protocol for Automatic Capsule Filling Machine
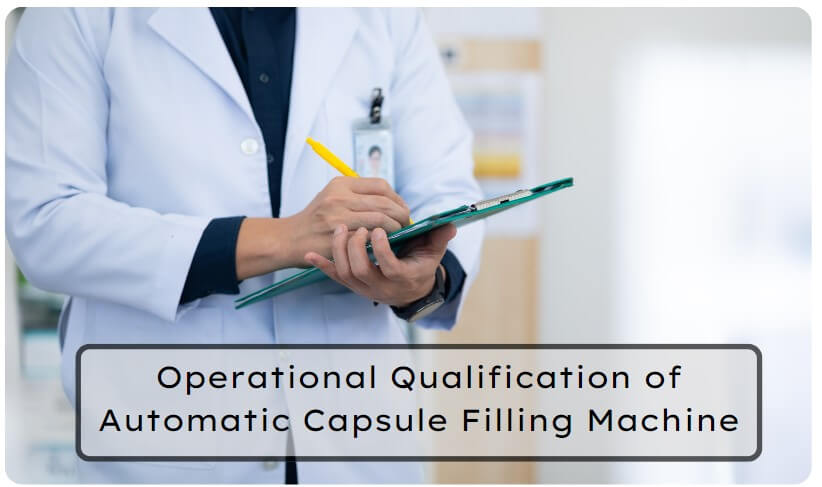
SERIAL NO. | ITEM DESCRIPTION |
1.0 | PROTOCOL APPROVAL |
2.0 | OVERVIEW: |
2.1 | Objective |
2.2 | Purpose |
2.3 | Scope |
2.4 | Responsibility |
2.5 | Execution Team |
3.0 | ACCEPTANCE CRITERIA |
4.0 | REVALIDATION CRITERIA |
5.0 | OPERATIONAL QUALIFICATION PROCEDURE |
5.1 | Equipment Description |
5.2 | Instruction for Filling the Checklist |
5.3 | Verification of Functional Checks |
5.4 | Verification of Key Functionality of Control Panel |
5.5 | Verification of Safety Feature (S) |
5.6 | Verification of Standard Operating Procedure |
5.7 | Verification of Component to be calibrated |
5.8 | Training Record Of Personnel (S) |
5.9 | Deficiency And Corrective Action(s) Report(s) |
6. 0 | OPERATIONAL QUALIFICATION FINAL REPORT |
6.1 | Summary |
6.2 | Conclusion |
6.3 | Final Report Approval |
1.0 | PROTOCOL APPROVAL: |
This Operational Qualification Protocol for the Automatic capsule-filling machine has been reviewed and approved by the following signatories.
FUNCTION | NAME | DEPARTMENT | SIGNATURE | DATE |
PREPARED BY | QUALITY ASSURANCE | |||
REVIEWED BY | PROJECTS / ENGINEERING | |||
REVIEWED BY | PRODUCTION | |||
APPROVED BY | QUALITY ASSURANCE |
2.0 | OVERVIEW: |
2.1 | OBJECTIVE: |
The objective of developing and executing the Automatic Capsule Filling Machine protocol is to collect sufficient informational data about the machine and define the qualification requirements and acceptance criteria for the machine and prove that each operation proceeds as per Design specifications and the tolerances prescribed there in the document are the same at utmost transparency. | |
2.2 | PURPOSE: |
This Protocol aims to establish documentary evidence to ensure that the Automatic capsule filling machine received matches the Design specification and that it is properly and safely installed. | |
2.3 | SCOPE: |
The Scope of this protocol is limited to the Operational Qualification of the Automatic capsule filling machine in XYZ Pharmaceuticals. Once the OQ of the Automatic capsule filling machine has been completed successfully, then equipment shall proceed with the next stage known as the performance qualification procedure. | |
2.4 | RESPONSIBILITY: |
The following shall be responsible; Quality assurance officer/Executive – For Preparation of Protocol /Execution Projects. Engineering Head – For the execution. Production Head – For execution support. Quality Assurance Head – For adequacy and final approval. |
2.5 | EXECUTION TEAM: |
The satisfactory operation of the Automatic capsule-filling machine shall be verified by executing the qualification studies described in this protocol. The successfully executed protocol documents that the Automatic capsule-filling machine is operational and is satisfactorily working. The execution team is responsible for the execution of the installation of the Automatic capsule filling machine. The execution team comprises of: |
DEPARTMENT | DESIGNATION | NAME | SIGNATURE | DATE |
PROJECTS/ ENGINEERING | ||||
PRODUCTION | ||||
QUALITY ASSURANCE |
3.0 | ACCEPTANCE CRITERIA: |
3.1 | It shall comply with all the designed specifications. |
3.2 | All supporting utilities of specified capacities shall be placed near the equipment. |
4.0 | REVALIDATION CRITERIA: |
The machine shall be revalidated if: | |
💡Any major changes affect the performance of the equipment. 💡After major breakdown maintenance is carried out. 💡As per the revalidation date and schedule. |
5.0 | OPERATIONAL QUALIFICATION PROCEDURE |
5.1 | EQUIPMENT DESCRIPTION: |
Equipment Name | Automatic capsule filling machine |
Supplier / Manufacturer | Manufacturer Name |
Overall Dimension (L X W x H) | Mention Your Dimension |
Working Capacity | XYZ/Hrs. |
Model | (Modal Name) |
Serial no. | XYZ |
Location | Capsule filling Area |
The automatic capsule-filling machine comprises of following components:
1. Structure Assembly 2. Drive assembly 3. Turret Assembly 4. Empty Capsule Holder Assembly 5. Powder Filling Device. 6. Tamping Station 7. Pin Plate Assembly. 8. Electrical control assembly 9. PLC 10. MMI |
5.2 | INSTRUCTION FOR FILLING THE CHECKLIST |
5.2.1 | In case of compliance of the test use the word ‘Complies’ otherwise use ‘Does not comply‘ to indicate non-compliance. |
5.2.2 | For identification of the components of the equipment and utilities use the word ‘’yes’’ to show its presence and use ‘No’ to indicate the absence of the identity |
5.2.3 | Give detailed information in the summary and conclusion part of the Operational Qualification report. |
5.2.4 | Whichever column is blank or not used ‘NA’ shall be used. |
5.3 | VERIFICATION OF FUNCTIONAL CHECKS: |
NAME OF SYSTEM COMPONENT | SPECIFIED FUNCTION | MATCHES WITH THE SPECIFIED FUNCTION(YES / NO) | VERIFIED BY(SIGN) | DATE |
1. Horizontal Finger Assembly | Turn hand wheel and check free movements of finger assembly in guides through its Stroke. Finger should not rub against its faces | |||
Movement of the fingers to be through the visual center of the rectifier block slot. The finger shouldn’t move in cross directions. | ||||
The capsule should be rectified and pushed forward in the rectifier block up to such a position that during the downward stroke of the magazine, vertical fingers will strike the cap portion 1mm from the junction of the cap and body. | ||||
After finger pushes the capsule forward, there shouldn’t be any stretch marks on capsule, specially the cap which is caused by the rough edges of the rectifier. | ||||
Finger assembly should not lift while the machine is running. Check at forward and backward strokes of figures at very slow speed (approx 20 spm speed). | ||||
No excessive rubbing of fingers with the Teflon guide check Teflon shreds. | ||||
2. Vertical finger assembly | Finger profile should guide empty capsule effectively and smoothly. The capsule should fall dead straight into the bushes below. A slightly inclined capsule will be led to capsule being thrown off in running. | |||
Check fingers at an equal distance from cap bush edge. Gap between vertical fingers and cap is to be 0.5 to 1.0 mm after cap bush plate moves up. | ______ mm | |||
Check visually if all the fingers are at center of rectifier block slot. Also, check that all fingers assembled are in one straight line. | ||||
Check the Gap between magazine bottom face/ rectifier block slot. Also, check if all fingers assembled are in one straight line. | _________ mm | |||
Check the gap between bottom edge of vertical finger and cup bush holder after cap bush holder moves up, to be 0.75 ±0.25 mm | ||||
Check the free movement of the release finger in the magazine slot. | ||||
3. Capsule release mechanism | Release liver should have 2 positions, 1 for releasing and 2 for stopping capsule flow. | |||
The liver should sit firmly in 2 positions with a small clicking sound. This means that the ball is firmly in position in the socket. | ||||
Check the movement of release fingers. None of them should touch the magazine of the loader lever throughout its full stroke. | ||||
A single capsule should be released from each row during each stroke into a rectifier block slot. Check this at full speed /reduced speed (20 spm) | ||||
Check to seal between grommets and body bush holders (Zero gaps for all stations). | ||||
No vacuum leakage through grommets or connections. | ||||
Check the vacuum sequence. After the capsules fall from the rectifier block into the bush holder, vacuum should come ON. | ||||
4. Vacuum Separation Block Assly. | Ensure that there is no capsule/powder chip in the vacuum filter on the top plate. | |||
5. Trials with empty capsules | If the above settings are found to be in order, conduct trials with capsules as under. Do not take trials if any of the above settings are not in order. | |||
Load empty capsules in the capsule hopper. There should be no static charge on capsules. Adjust the capsule empty control flap to a pilot position and start the machine. | ||||
Cap popups due to excess vacuum. The vacuum left is 22 – 24 “ of Hg. | _______ “ of Hg | |||
Ensure proper functioning of the vacuum gauge. | ||||
Check for a proper uniform flow of capsules in the magazine. | ||||
The cavity of the magazine should not become empty due to the lack of capsules. If this happens adjust capsule flow by control flap. Once the position of the flap is set, this should not be adjusted till the end of the trial. | ||||
The capsule should get properly loaded in bushes without crushing. | ||||
When all these settings are OK and capsules are running correctly on the machine set the counter to “0” Remove all capsules from the top plate, and anywhere on the machine. Load a fresh capsule in the capsule hopper. (Do not disturb any settings now ) | ||||
Check the proper entry of capsules in the magazine. | ||||
Check the proper release of capsules in the rectifier block (one at a time). | ||||
Check proper separation of cap/body. | ||||
Removal of unopened capsules inside the unopened capsule box with an air jet. | ||||
Check the closing of capsules without denting/telescoping. | ||||
Closed joint of the capsule is to be set as per the table. | ||||
Size# 2 18.0 mmClosed joint length (±0.4 mm). | Actual_______ mm | |||
Check proper ejection of capsules through the exit chute without crushing. | ||||
If the above observations are found satisfactory, continue till the counter shows “25000” capsules. | Actual filled _____caps. | |||
Stop the machine and count the number of rejected capsules from each stationsRejected capsules on the machine surface to be less than 1% inclusive of all the defects. (for machine-related errors only). | ||||
Details of rejected capsules: A) Double capsule loaded in rectifier block. B) Crushed during loading. C) Cap pop-up. D) Body crushed during separation. E) Unopened capsules. F) Crushed during closing. G) Crushed during ejection. H) Others (Specify) Total | _____ Nos. _____Nos._____ Nos. _____ Nos._____ Nos._____ Nos. _____ Nos._____ Nos. _____ Nos. | |||
6. Powder filling operations | Rest all tamping positions for stations 1–5 on the support pad. All scales should “0” reading. | 1 2 3 4 5__ __ __ __ __ | ||
On tamping station no 6, the gap between body bush and tamping in bottom most conditions, should be 0.3± 0.1mm. | ||||
The gap between the support pad and dosing disc is less than 0.05 mm. | ||||
Check the dosing disc to aluminium guide plate alignment. | ||||
The slug does not get cut when it is being ejected from the disc and enters the body bushes. Check entry of alignment gauge “Body bush – Dosing Disc”. | ||||
Gap between the dosing disc and wiper block is to be 0.08 to 0.1 mm check size 2 as well as dosing disc supplied. | ||||
Check for the numbering of each position holder. Ensure that each position holder is in its correct position from 1 – 6 (Anti-clock wise for AF25 T (Modal Name) when seen from the top). | Anti-clockwise /Clockwise | |||
Set the powder proximity switch such that it functions 3 mm away from the powder. Using dummy powder in a plastic can do these settings. | ______ mm | |||
Start the machine. Check for proper formation of slug. The slug should not be too hard. It should break with a slight pressure on the hand. | ||||
The slug should be of even hardness throughout its length. | ||||
The slug should be flat from both sides indicating perfect compaction. | ||||
Powder should flow properly in all parts of the dosing disc. Adjust the gate flap and sensor to ensure sufficient powder & uniform distribution of powder in the tub. | ||||
The slug should pass to the slug collection box without sticking to the piston. Check for damage / Scratches to piston. | ||||
Fill a batch of 1000 capsules and check for: a) Denting b) Telescoping. c) (Unlocked) Folded | _______ Nos._______ Nos._______ Nos._______ Nos. | |||
Check weight variation. | Avg. wt. _____ mg | |||
Check the condition of spring after the above. Check for the free height of spring it should be maintained at 42 mm. | ||||
7. Unopened Capsule Collection Box Assembly. | Check the air jet from each hole of air jet block. | |||
Ensure the ejection pin doesn’t scratch cap bushes. Check bush’s inner face. | ||||
All pins are to be below cap bush surface by up to 0.2 mm | _______ mm. | |||
Pins to be in center of the bushes. | ||||
Stop vacuum and start capsules. All unopened capsules are to be ejected and collected in an unopened box & no capsule is to spill outside or get stuck. | 100% ejected & collected ____Nos. not ejected or damaged. | |||
8. Capsule Closing Assly. | Pins to be in the center of the bush. | |||
Ensure closing pins don’t stretch body bushes. Check Bush’s inner face. | ||||
Ensure the closing length of all capsules is within a segment within ±0.4 mm. (All 4 capsules/segments) | ||||
9. Exit chute assly. | Check the alignment of the guide plate and bush holder (Visual Center) | |||
Ensure uniform airjet from each block of airjet block. | ||||
The gap between guide plate and segment is to be 3 mm max. The above gap is to be checked at both ends. It should be within 005 mm | ||||
The ejection pin should come out by 2-2.5 mm from the guide hole. | ||||
Ensure the ejection pin doesn’t stretch cap bushes. Check Bush’s inner face. | ||||
Ensure that the group sampling flap is opening fully on command, also the flap closes immediately on command. | ||||
Ensure all capsules are collected in the sampling box only. Tray 100 capsules. No capsules to spill outside the box or escape to the exit point when flap is open. | ||||
10. Bush Cleaning Station | Ensure the attachment is not jammed and is removable from hand pressure. | |||
Ensure that there is at least a 1 mm gap between the attachment and loader cover. | ||||
Ensure that the attachment is tightened with a knob. | ||||
11. Setting up turret, Housing, and Pinplate. | Check the alignment gauge “bush to bush” Entry to loose / medium. | |||
Ensure air pressure pressure is 6 kg/cm2 or more. | ||||
Clamp to operate when the turret is just/ about to finish its indexing motion. The operation should result in top side pushing the cap plate down giving the bush-to-bush gap of 0.05- 0.15 m. | ||||
Ensure proper functioning of the clamp at full speed and low speed. (20 spm) | ||||
No air leakage from Festo cylinders and its fittings and M20 lock nut. | ||||
Check and confirm plat in the pin plate is not more than 0.2 to 0.3 mm. | ||||
12. Pneumatic | Ensure the functioning of the air pressure gauge. | |||
No air leakage from each connector and fittings. | ||||
Air bush cleaning, unopened caps, exit chute to be dry (Without Lubrication). | ||||
Pressure switch functions so that the machine trips below 5 kg/cm2 air pressure. | ||||
Feel air output from the FRL Filter unit. It should be dry and without moisture. | ||||
Check the machine speed of 106 strokes per minute (SPM). | ||||
Counter to flip 4 per/stroke | ||||
13. Electrical and Electronics | Check the critical values of the AC. Mitsubishi: A) ACC – 10 sec. B) DEC – 0.5 sec. |
5.5 | VERIFICATION OF KEY FUNCTIONALITY OF THE CONTROL PANEL: |
COMPONENT OF CONTROL PANEL | SPECIFIED FUNCTION | MATCHES WITH THE SPECIFIED FUNCTION(YES / NO) | VERIFIED BY(SIGN) | DATE |
1. ON / OFF | Machine to start and stop. | |||
2. SS button | If the press sampling flap opens. | |||
3. Capsule Counter Button | It displays a flapping count. | |||
4. Capsule Counter Button | It displays the correct machine speed by physically counting a number of strokes in a minute. | |||
5. Check potentiometer knob. | It locks at Min. / Max. Positions. | |||
The machine shall be at full speed at a full revolution of the potentiometer. | ________ SPM | |||
The machine shall be at zero speed at the minimum speed of the potentiometer. |
5.6 | VERIFICATION OF SAFETY FEATURES: |
SAFETY FEATURES DESCRIPTION | FUNCTION | VERIFIED BY(SIGN) | DATE |
1. Earthing | To avoid electrical shocks due to leakage current. | ||
2. Emergency stop button | To stop the machine if the problem appears in running condition. | ||
3. Safety Y | The machine is to stop if any polycarbonate door opens. |
5.7 | VERIFICATION OF STANDARD OPERATING PROCEDURE (SOP): |
The following Standard Operating Procedures were verified as important for the effective performance of the Automatic capsule-filling machine.
Sr.No. | SOP TITLE | SOP NUMBER | VERIFIED BY | DATE |
1. | ||||
2. | ||||
3. | ||||
4. |
5.8 | VERIFICATION OF COMPONENTS TO BE CALIBRATED : |
COMPONENT / PART TO BE CALIBRATED | IDENTIFICATION NO. | EXTERNAL CALIBRATION(Attach Certificate) | VERIFIED BY(SIGN) | DATE |
1. Pressure Gauge. |
5.9 | TRAINING RECORD OF PERSONNEL (S) : |
Sr. No. | Name of Personnel | Designation | Sign. & Date | Trained By | Remark |
1. | |||||
2. | |||||
3. | |||||
4. | |||||
5. |
5.9 | DEFICIENCY AND CORRECTIVE ACTION(S) REPORT(S): |
The following deficiency was verified and corrective actions were taken in consultation with the Engineering Department. |
Description of deficiency : |
Corrective action(s) taken : |
Reviewed By:
Date:
6.0 | OPERATIONAL QUALIFICATION FINAL REPORT: |
6.1 | SUMMARY: |
6.2 | CONCLUSION: |
6.3 FINAL REPORT APPROVAL
It has been verified that all tests required by this Automatic Capsule Filling Machine Protocol have been completed, reconciled, and attached to this protocol or included in the qualification summary report. It has been verified that all amendments and discrepancies are documented, approved, and attached to this protocol.
The signature in the block below indicates that all items in this qualification report of Automatic capsule filling machiner have been reviewed and found to be acceptable and that all variations or discrepancies have been satisfactorily resolved.
NAME | DESIGNATION | DEPARTMENT | SIGNATURE | DATE |
PROJECTS / ENGINEERING | ||||
PRODUCTION | ||||
QUALITY ASSURANCE |
Related Topics:
- Auto Coater Installation Qualification Protocol/ Annexures
- Auto Coater Operational Qualification Protocol/ Annexures
- Auto Coater Performance Qualification Protocol
- Blender Installation Qualification Protocol/ Annexures
- Blender Performance Qualification Protocol/ Annexures
- Blister Machine Operation Qualification Protocol/ Annexures
- Design Qualification in Pharmaceutical Industry
- Design Qualification of Electric Stacker
- Design Qualification Protocol for Vertical Laminar Reverse Flow
- Installation Qualification Protocol for Automatic Capsule Filling Machine
- Installation Qualification Protocol for Blister Packing Machine with Annexures

Naresh Bhakar is the Founder and Author at Pharmaguddu.com, bringing his extensive expertise in the field of pharmaceuticals to readers worldwide. He has experience in Pharma manufacturing and has worked with top Pharmaceuticals. He has rich knowledge and provides valuable insights and data through his articles and content on Pharmaguddu.com. For further inquiries or collaborations, please don’t hesitate to reach out via email at [email protected].