In this section, we will explore the objectives, applications, and different factors which affect the mixing process, as well as the mechanisms involved in solid, liquid, and semisolid mixing. We will also discuss the principles, construction, working, uses, merits, and demerits of various mixers commonly used in different industries.
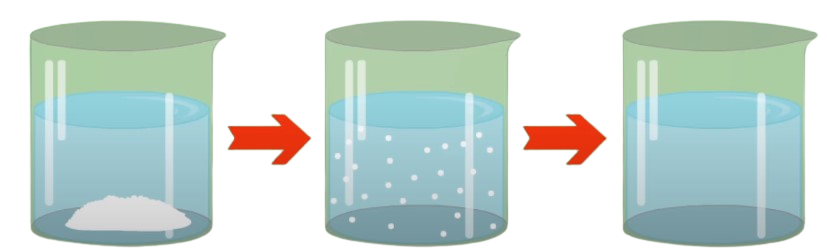
Definition
Definition: Mixing (or blending) is a unit operation in which a uniform mixture is obtained from two or more components, by dispersing one within the other. Hence it is a process that involves manipulating a heterogeneous physical system, with the intent to make it more homogeneous.
Objective of Mixing
The objective of mixing includes the following:
- Uniformity- to secure uniformity of composituion and ensure correct dose.
- Chemical reaction enhancement-Mixing encourages and at the same time controls a chemical reaction. Mixing ensures a uniform product and the degree of mixing will decide the possibility of reaction.
- To manufacture simple physical mixtures either using two or more miscible liquids or two or more uniformly divided solids.
- Physical change – supersaturated solutions are mixed to produce crystals.
- Achieving dispersion-Mixing is also aimed to include the dispersion of two
- immiscible liquids to form an emulsion or dispersion of a solid in liquid to give a suspension or paste. Usually, good mixing is required to ensure stability and effectiveness.
Applications of Mixing
Mixing plays a vital role in various applications, including:
- Mixing of powders in granulation and tablet section.
- Dry mixing of the materials by using blenders for direct compression in tablets.
- Dry blending of powders for capsule filling and compound powders.
- A blending of powders in cosmetics in the preparation of face powders, and tooth powders.
- It is used in the Dissolution of soluble solids in viscous liquids for filling soft capsules and syrups.
- Mixing of two immiscible liquids for preparation of emulsions.
Factors Affecting Mixing
Below are the following factors that influence the mixing process:
- Nature of product: Smooth particle surfaces are easy for effective mixing.
- Particle size: Mixing powders with similar particle sizes is easier, while a significant difference in particle size can lead to segregation.
- Particle shape: Spherical particles are ideal for a uniform mixture.
- Particle charge: Electrostatically charged particles may exert attractive forces, leading to separation.
- Proportion of material: Equal proportion produces fine mixing
- Relative density: If the components have different densities, high-density particles settle down.
- Viscosity: Increasing viscosity reduces the extent of mixing.
- Surface tension of liquids: Higher surface tension limits the process of mixing.
- Temperature: Viscosity changes with temperature, thus affecting the mixing process.
- Mixture volume: Mixing efficiency depends on the volume of the mixture.
- Agitator type: The shape, size, location, and type of agitator affect the degree of mixing.
- Speed/rpm of the impeller: Mixing at lower RPMs tends to be more homogenous than at higher RPMs.
- Mixing time: Adequate mixing time is essential for achieving the desired homogeneity.
Mixing Equipments:
Below is the following equipment used for mixing:
- Triple Roller Mill: Principle, Construction, Diagram, Working, and Applications
- Paddles Mixture: Principle, Construction, Working, Advantages, and Disadvantages
- Silverson Mixer: Principle, Construction, Working, Advantages and Limitations
- Turbine Mixture: Principle, Construction, Working, Advantages and Disadvantages
- Propellers: Principle, Construction, Working, Advantages and Disadvantages
- Sigma Blade Mixer for Mixing
- Ribbon Blender: Principle, Construction, Working, Varients, Advantages, and Disadvantages
- Rapid mixture granulator(RMG); working and principle
Comparison between Solid Mixing and Liquid Mixing:
Aspect | Solid Mixing | Liquid Mixing |
Definition | The process of blending solid pharmaceutical materials. This process is used for mixing dry powder. | The process of combining liquid pharmaceutical materials. It is used for the preparation of Liquid mixtures, suspensions, or emulsions. |
Type of materials | Solid powders, granules, or particles | Liquid mixture, suspensions, or emulsions. |
Mixing equipment | Mortar and pestle, blender, mixer, or granulator | Magnetic stirrer, homogenizer, or agitator |
Sample Size | Large sample sizes are required. | A small sample size is sufficient |
Mixing process | Mechanical agitation and blending | Stirring or agitation to achieve uniform dispersion |
Uniformity | Mixing solids aims for uniform particle distribution | Mixing liquids aims for a uniform solution or suspension |
Challenges | Risk of segregation, poor flow properties | Homogenization, dissolution, or emulsification issues |
Time | Solid mixing may take longer due to particle blending | Liquid mixing is usually faster |
Heat generation | Solid mixing may generate heat due to friction | Liquid mixing may generate heat due to agitation |
Clean-up | Solid mixing equipment requires thorough cleaning | Liquid mixing equipment needs cleaning but is easier |
Scale-up | Scaling up solid mixing can be challenging | Scaling up liquid mixing is generally easier |
Mechanism of Mixing
The mechanism of mixing varies and it depends on the state of the materials being mixed.
Mechanism of Solid Mixing:
Solid mixing involves the following mechanisms:
Convective mixing: Groups of particles move from one position to another by using blades or paddles, also known as macro mixing.
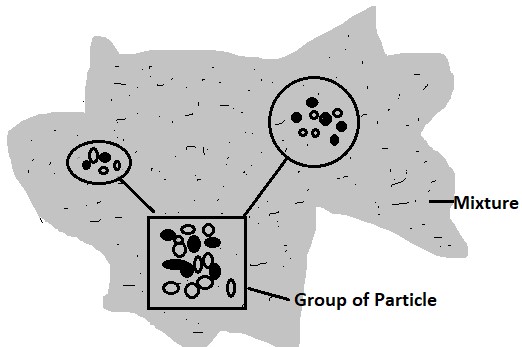
Shear mixing: Shearing forces generated by stirring arms or bursts of air create internal forces within the material. This type of mixing occurs when a layer of material flows over another layer resulting in the layers moving at different speeds and therefore mixing at the layer interface.
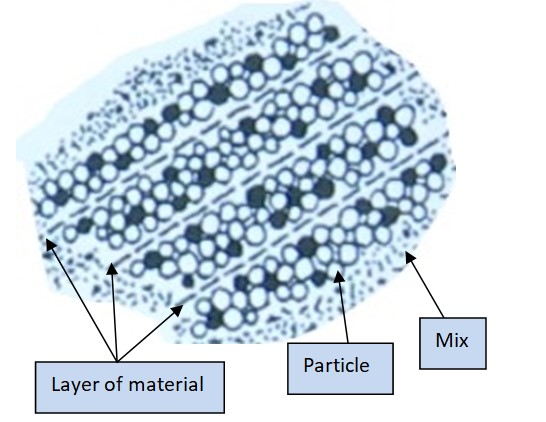
Diffusive mixing: Diffusive mechanism occurs by random movement of the particle within the powder bed and causing them to change their relative position relation to one another, known as micro mixing.
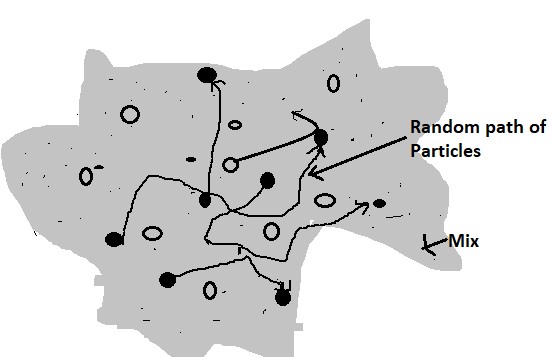
Mechanism of Liquid Mixing:
Liquid mixing has the following mechanisms:
Bulk transport: Large portions of material are moved from one location to another using rotating blades or paddles.
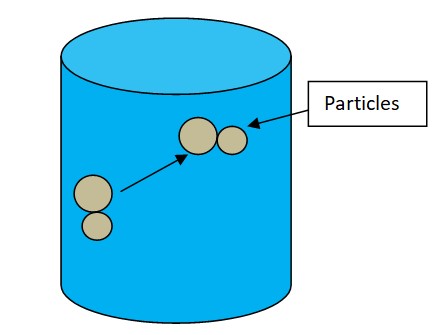
Turbulent mixing: Turbulence in the liquid creates mixing, and it is influenced by velocity gradients between adjacent layers.
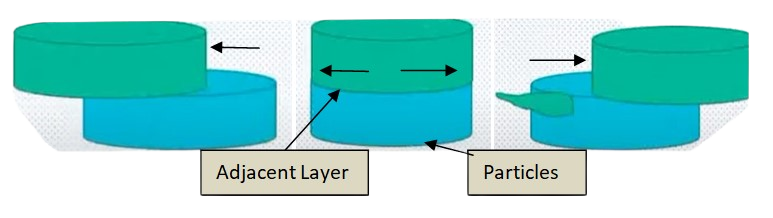
Laminar mixing/Streamline mixing: Mixing dissimilar liquids through a laminar flow results in shear forces that stretch the interface between them. The folding of the layers increases the interfacial area, promoting efficient mixing with time.
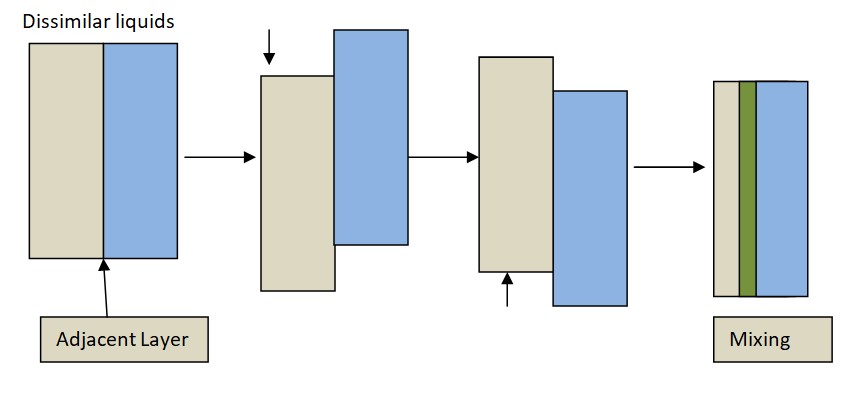
Molecular diffusion: Mixing at the molecular level occurs through diffusion, which is a result of the thermal movement of molecules.
Mechanism of Semi-Solid Mixing:
Semi-solid mixing mechanisms depend on the characteristics of the materials being mixed. While considerable variation exists, many semi-solids form neutral mixtures without a tendency to segregate, although sedimentation may occur. The three commonly used semi-solid mixers are:
(a) Sigma blade mixer: This mixer consists of two blades operating in a double-trough-shaped vessel, moving at different speeds toward each other. It is used for products such as granulation masses and ointments.
(b) Triple-roller mill: In this Differential speed and narrow clearance between the rollers generate high shear over small volumes of material. Roller mills are commonly used to grind and achieve homogeneity in ointments.
(c) Planetary mixers: These mixers utilize a rotating mixing arm about its own axis and a common axis, typically the center of the mixing wheel. The blades provide kneading action, while the narrow passage between the blades and the can wall generates shear.
Mixer selection
When selecting mixing equipment, several factors should be considered, including:
(a) Physical properties of materials: Density, viscosity, and miscibility of the materials being mixed.
(b) Economic considerations: Operating efficiency, cost, and maintenance.
(C) Fill Volume: The working volume depends on the mixer’s construction and generally, it is considered between 50% to 70% of the maximum volume
(d) Residence time: It is the duration of ingredients spent in the mixer, which is important for proper mixing.
(e) agitators: Agitators types also play an important role in mixing, so as below:
Ribbon: Suitable for powders, granules, and some slurries, especially free-flowing materials.
Paddle: Effective for powders, granules, some slurries, free-flowing materials, and light pastes.
Sigma: Specifically designed for sticky materials, thick pastes, and slurries.
Mixing Indices: Analyzing Homogeneity
The choice of a mixer depends on the mixing index or degree of mixing, which involves assessing the standard deviation of a sample from the mixer. To quantify the mixing index, Lacey’s equations are used. Two of them are particularly relevant:
Maxing Index, M:

Here, σ0 represents the standard deviation of the unmixed powder sample. The resulting ratio will always be less than 1. The higher the M value, the greater the homogeneity achieved. These equations are instrumental in determining the homogeneity of a mixture based on specific objectives. Selecting the appropriate equation is important when analyzing the mixing mechanism, and practical outcomes can be achieved through statistical analysis.
Discrepancies in the mixing process may indicate issues such as poor or inadequate sampling, unsuitable mixing operations, improper handling of the powder sample, or unfavorable operational conditions. It becomes important to identify these factors to ensure proper mixing.
Before starting the mixing process, the materials inside are present in two separate layers: one is tracer material, and the other consists of tracer. Under these initial conditions, the standard deviation at zero time, denoted as σ0, can be calculated using the expression:
σ0 = √(a(1 – a))
Here, a represents the overall fraction of tracer material in the mixture at the start.
Conclusion:
In conclusion, Mixing is an important aspect in pharmaceuticals and other industries to get consistency in formulation, or mixture.
FAQs (Frequently Asked Questions):
Ans: Mixing is important in industries to get uniformity in mixtures and to maintain the quality of the end product.
Ans: Factors including the nature of the product, particle size, shape, charge, proportion of material, viscosity, temperature, relative density, and agitator type can significantly impact the mixing process.
Ans: Solid mixing involves convective mixing (macromixing), shear mixing, and diffusive mixing (micromixing) mechanisms.
Ans: Liquid mixing can occur through bulk transport, turbulent mixing, laminar mixing (streamline mixing), and molecular diffusion.
Ans: Commonly used mixers for semi-solid mixing include Sigma blade mixers, triple-roller mills, and planetary mixers.
Ans: Proper mixing ensures uniformity in mixtures, accurate dosing, enhanced product quality, and improved overall performance in various industries.

Naresh Bhakar is the Founder and Author at Pharmaguddu.com, bringing his extensive expertise in the field of pharmaceuticals to readers worldwide. He has experience in Pharma manufacturing and has worked with top Pharmaceuticals. He has rich knowledge and provides valuable insights and data through his articles and content on Pharmaguddu.com. For further inquiries or collaborations, please don’t hesitate to reach out via email at [email protected].