The Restricted Access Barrier System (RABS) enhances product control but reduces operator communication in aseptic manufacturing. The main aim of the RABS in pharmaceutical products is to ensure they are free of all contamination risks.
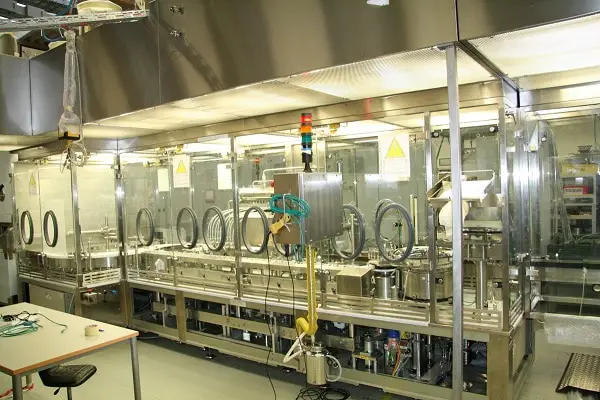
During the early 1990s, new systems were developed to help sterile pharmaceutical manufacturers ensure contamination-free sterile products at a very high level. These systems, known as isolators and restricted access barrier systems (RABS), were crucial. The first Isolator was launched to guarantee sterility by isolating a part of the machinery from the environment, keeping the product processing separate from human intervention.
Initially, technical issues and discussions on sterilization validation or decontamination of the isolator posed challenges. However, with essential improvements over time, these issues were reduced. Currently, the isolator process is considered the safest and most reliable. However, it still requires a lengthy changeover time.
Therefore, RABS can enable shorter start-up times, easier changeovers, and reduced capital costs, especially with recent improvements.
What is RABS in Pharmaceuticals?
RABS stands for “Restricted Access Barrier System.” In 2005, the FDA commissioned a study group to develop a definition and determine the components needed to ensure that a RABS system works well for the manufacturer. The International Society for Pharmaceutical Engineering (ISPE) study group comprised experts from major manufacturers.
According to the group, RABS must include well-designed equipment, and all operators must receive comprehensive training in critical practices such as proper gowning. Additionally, all RABS must include the following:
- A barrier to avoiding human enrollment directly into the critical area.
- ISO 5 environmental for airflow, at least in the critical zone.
- Different ports for glows are provided to avoid direct contamination.
- High-level disinfection.
- well-defined procedures and Highly automated processes for very few open-door interventions.
Introducing 4 Types of RABS
1. Open active RABS:
This type is characterized by a barrier wall open on one side, typically facing a cleanroom. It provides an access point for operators, however, it requires them to don sterile garments and gloves. This is because even a single microbe can lead to contamination, which in worst-case scenarios could cause product recall events (Total 3849) as recorded by the FDA between 2012 to 2024.
Note: Data includes all types of drug product recall by the FDA in different scenarios. (see: Source)
2. Open passive RABS:
This type closely resembles an open active RABS, but the barrier wall isn’t pressurized, leading to a slightly elevated risk of contamination from surrounding areas.
3. Closed active RABS:
This style features a closed barrier wall, with operators entering the work chamber through a pass-through gowning station. The work chamber is pressurized slightly higher than the surrounding area, a measure designed to reduce the risk of contaminants.
4. Closed passive RABS:
Again similar to its active counterpart, yet its barrier wall isn’t pressurized – leading to a marginally higher risk of contamination from the surrounding area.
How RABS works:
Ensure the use of a gloves port barrier system during the changeover of machine parts or product parts. The dispensing material is passed inside the closed chamber through the glow port provided at the opening. Materials shall be weighed inside it on a calibrated instrument. After weighing, the material is passed directly into stainless steel containers lined with polybags. The remaining materials (after weighing) are tied inside the chamber with a cable tie and passed at the other end.
The system should be followed during other manufacturing activities as required.
What are the best practices to use of RABS?
RABS creates a gap between products and operating personnel to ensure high product quality. However, to operate RABS effectively, operators must follow some best practices: Open-door interference is prohibited.
During operation, the barriers must not be compromised; failure to comply can result in contamination and increased product risk. Therefore, when conducting aseptic operations in a RABS, thorough cleaning and line clearance must occur before commencing operation.
Ensure the use of the Gloves port barrier system during machine parts or product changeovers.
A detailed study was conducted to configure the machine and its surrounding barrier, enabling operators to handle all areas within the machine using gloves.
The study also examined operations and potential machine interferences. Officers from various departments, such as engineering and quality assurance, participated in the study to ensure the overall functionality of the RABS system.
The barrier system should only be opened during cleaning procedures. Disinfection activities should be carried out after completing each stage of production. Following the filling process, microbial activities need to be monitored. The example of Disinfectants include Dettol and Savlon.
All used gloves should undergo periodic checks for integrity and microbial testing. Once confirmed airtight, they can be cleaned and steam-sterilized. The gloves should then undergo a pressure-decay test to detect even the smallest holes. Fit all gloves into the RABS system for the subsequent product.
Materials for products like syringes and stoppers must be sterilized using steam and dry heat. The outer packaging should be sprayed with a sterilizing agent such as IPA 70% before being moved to the ISO 5 area through a lock, where the outer packaging is discarded.
Use the glove portal system for all steps. Packaging materials shall be placed in sterilized bags or special containers. The container’s content shall be exposed to ISO 5 conditions only.
Conclusion
The RABS process keeps things secure by blending cleanroom design and aseptic safety like an isolator but with more flexibility. Automation in pharmaceuticals is more important as it reduces the variability and makes the whole process fast. This setup could really make a difference in keeping the final product clean. Plus, RABS is a great solution to face present and future challenges in making aseptic products.

Naresh Bhakar is the Founder and Author at Pharmaguddu.com, bringing his extensive expertise in the field of pharmaceuticals to readers worldwide. He has experience in Pharma manufacturing and has worked with top Pharmaceuticals. He has rich knowledge and provides valuable insights and data through his articles and content on Pharmaguddu.com. For further inquiries or collaborations, please don’t hesitate to reach out via email at [email protected].