Size reduction refers to the process of reducing the size of drugs into smaller particles or fine powder. It involves cutting or breaking particles of solids into smaller pieces. Size reduction becomes necessary when the starting material is too coarse and the desired final product needs to be in the form of a fine powder.
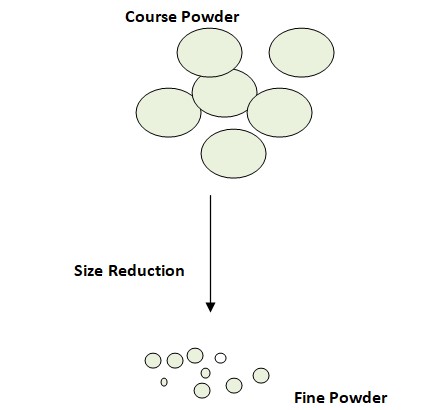
Significance of Size Reduction:
- Enhanced stability of certain pharmaceutical dosage forms, such as suspension, as reducing the particle size of the drug significantly reduces the rate of sedimentation.
- It helps in the separation of solids from liquids through filtration, as the rate of filtration depends on the particle size.
- Increases the rate of absorption of drugs since smaller particle sizes allow for greater absorption.
- Enhance the rate of solution for chemical substances, as reducing the particle size increases the surface area available for solvent action.
- Enables the design of different types of drug dosage forms, including tablets, capsules, suspensions, and emulsions.
Mechanisms:
Size reduction mechanisms depend on the type of equipment used and the nature of the material being processed. Here, below is some common mechanisms:
Compression: This mechanism involves applying pressure to compress the material, causing it to fracture. Examples of equipment using compression include crushers, roll mills, and tablet presses.
Impact: Impact-based size reduction involves subjecting the material to high-speed collisions with the help of stationary or rotating objects. Impact mills, hammer mills, and impact crushers are commonly used for this purpose.
Attrition: Attrition occurs when particles are rubbed or sheared against each other, resulting in size reduction. Attrition mills, ball mills, and fluid energy mills mainly use this mechanism.
Cutting: Cutting mechanisms involve using sharp blades or knives to slice or shear the material. Cutting mills and knife cutters are commonly used in this type of size reduction.
Laws:
Law | Description |
Kick’s Law | The energy required for reduction is directly proportional to the surface area produced. |
Rittinger’s Law | The energy required for reduction is proportional to the new surface area created during the process. |
Bond’s Law | Work required to reduce particle size is directly proportional to the square root of the reduction ratio. |
Hukki’s Law | Energy required for size reduction is proportional to the new surface area created during the process. |
Factors Affecting Size Reduction:
Hardness: The hardness of the material affects the production process. Soft materials are easier to break down into smaller sizes compared to hard materials. Material hardness also impacts drug solubility and the modification of dosage forms.
Toughness: Fibrous crude drugs tend to be resistant to breaking down into smaller particles, exhibiting toughness. Fibrous materials are layered and attached to each other, which affects their solubility.
Material structure: Material structure also causes a significant challenge during size reduction. Because in this case a special machine/Equipment is to be used to reduce the size of materials.
Moisture content: The presence of moisture in the material may cause hardness and stickiness, which later, affect particle reduction. Moisture levels of 5% in the case of drying grinding and 50% in wet grinding do not cause significant issues.
Stickiness: Stickiness of the material creates difficulties in size reduction. it adheres to the grinding or sieve surfaces of the mill. Material stickiness also affects the accuracy of material weighing.
Softening temperature: Waxy substances or drugs containing oil or fat tend to soften during the size reduction process. If excessive heat is generated, the material does not break down easily and sticks to the mill. Higher temperatures generated in the machine can impact material stability and may also alter its activity.
Required purity: Some mills used for reduction may cause the grinding surface to wear off, leading to impurities in the powder. If a high degree of purity is required, such mills should be avoided.
Physiological effects: Some drugs release dust particles during their reduction, which can have adverse effects on manpower. In such cases, enclosed mills should be used to minimize dust exposure.
Bulk density: The output of material size reduction in a machine depends on the bulk density of the substance.
Ratio of feed size to product size: To achieve a fine powder in a mill, it is necessary to use a relatively small feed size. Because of this, the size reduction process is carried out in several stages using different equipment, such as preliminary crushing, followed by coarse powder, and then fine grinding.
Methods of Size Reduction:
Cutting: The material is cut on a small scale using sharp blades, knives, or other cutting instruments. On a larger scale, a cutter mill is used for cutting drugs, often to expedite the drying process.
Compression: In this method, pressure is applied to crush the material. On a small scale, a mortar and pestle are used, while a roller mill is used on a larger scale.
Impact: Impact occurs when a stationary material is struck by an object moving at high speed, or when moving particles collide with a stationary surface. In both cases, the material breaks into small pieces. For this no small-scale instrument used is used in industries, Hammer mill is generally used for large-scale production.
Examples of impact-based size reduction equipment include hammer mills and ball mills.
Instrument used:
Below are the following Instruments that are used for size reduction:
Conclusion
In conclusion, It is a process used across pharmaceuticals and other industries to get size reduction. Knowing the above Mechanism, Factors, Significance, and methods may help to enhance knowledge, resulting a significance growth in process and production.

Naresh Bhakar is the Founder and Author at Pharmaguddu.com, bringing his extensive expertise in the field of pharmaceuticals to readers worldwide. He has experience in Pharma manufacturing and has worked with top Pharmaceuticals. He has rich knowledge and provides valuable insights and data through his articles and content on Pharmaguddu.com. For further inquiries or collaborations, please don’t hesitate to reach out via email at [email protected].