Learn about Standard operating procedures for Camera Vision Systems and Pinhole detector including Aim, Purpose, Responsibility, Precautions, Procedure, Frequency, and Annexures.
Aim: Standard operating procedure for camera vision systems in Pharmaceutical
Purpose: To lay down the procedure for setting, operation, and in-process check for the camera vision system and pinhole detector.
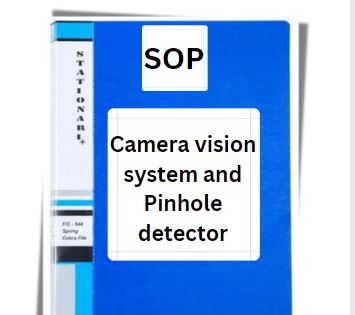
Scope: This standard operating procedure is applicable to carry out setting, operation, challenge, cleaning, and in-process checks of the camera vision system and pinhole detector at the plant.
Responsibility:
- The production officer is responsible for setting, operating, challenging, and cleaning the camera vision system and pinhole detector.
- Head Production is responsible for ensuring compliance with this SOP.
Precautions:
- Do not touch the Moving part of the machine when the machine is in operation mode.
- Do not operate the machine without a safety guard.
- Ensure that the machine is connected to the proper power supply with a socket having proper earthing.
- Before doing any maintenance work on the machine, switch off the power supply.
- Wear a nose mask and hand gloves throughout the operation.
Procedure Camera Vision System and Pinhole Detector:
For setting, operation, and cleaning of the camera vision system:
- Switch on the mains supply from UPS, and switch on the camera vision system by pressing the green button on the camera display body.
- After the start of the camera system, it shall show the option inspection, model, admin, demo, troubleshoot, change password, sign in, and quit.
- Click on the sign-in option, and then the login window will appear to select the user type options (operator, technician, and administrator). Enter the username and password.
- To start the camera inspection from the previous set-top model, click on the inspection tab and enter the batch number, and click on start inspection. Now the camera will start inspecting, and run the blister packing machine as per sop. “operation and cleaning of blister packing machine.”
- For teaching a new model, click on the option “model,” and a new window shall appear, click on the option “add model” to make a new model and enter the name for the new model And ensure that before teaching the new model old model shall be deleted and the same shall be verified by QA.
- In a new model following options will appear “object,” base film” and “color,” select the object according to the product. Select the base film color and select the number of colors in the color option.
- Click on the “Teach” tab. Followed by GRAB”.
- The next screen shows “Please run Empty blister,” then next click ok.
- Run the machine in feeding “off” mode.
- Click on the “external tab.” and then the internal tab will appear on the screen.
- Then fill the blister and Run the machine.
- The screen will show as “please run filled blister.” then next click ok.
- Run the machine in feeding “on” mode and click on the “Ok” tab to generate the image of the filled web.
- Draw the region of inspection (ROI) and click on the “next” tab.
- Draw the outline on one representative unit blister (which corresponds to the respective track) and click on the “search” tab, which leads to automatic identification and numbering of the rest of the unit blister in ROI.
- Click on the “next” tab.
- Draw the outline on one pocket and click on the “search” tab, which leads to the automatic identification and numbering operation of the pocket in ROI. .click on the “next” tab.
- Choose that color panel from the available green, blue, and red colors which images are satisfactory.
- Then press the “DONE” tabs after the click on the “Threshold tab.”
- Click on fine-tune and adjust fine-tune, then click on “Done,” then followed by “next “followed by “ok,” and then “next.”
- Then press the ok button after the screen shows “Model Teaching Complete.”
- The main window will appear, click on the option “Inspection,” enter the batch number, press “enter,” and click on the “start” button to start the inspection.
- After this camera will start the inspection, count the number of blisters in one track from the camera scanning head to the punching tool, and enter the count in the BQS machine MMI to reject the camera-rejected blister.
- Clean the MMI of the camera vision system and its inspection hood with a dry lint-free cloth after completion of the operation.
Procedure for Camera Challenge Test:
Frequency:
- At the start of the batch
- After every break
- At the end of the Shift
- End of the batch.
Procedure:
- Start the blistering operation as per sop “operation and cleaning of blister packing machine.” remove one tablet from the web from one representative unit blister (which corresponds to the respective track) before the inspection.
- Ensure that the respective blisters should be shown as rejected on the PLC of the camera when inspection.
- Ensure that the respective blister should be rejected physically at the punching station.
- Mark the tablet with the help of a black permanent marker and put it on the web for the challenge of foreign particles.
- Break the tablet and put it on the web for the challenge of the Broken tablet.
- Discolor the tablets with the help of a red marker and put them on the web for the challenge of discoloring tablets.
- Ensure that the respective blisters should be shown as rejected on the PLC of the camera while inspection.
- Ensure that the respective blister should be rejected physically at the punching station.
- Record the observation in BPR.
- If the camera vision system is failing for the in-process checks, stop the machine and quarantine the quantity packed between the last satisfactory test and the present unsatisfactory test and put an appropriate status label on it.
- Rise the deviation and inform to engineering department through the maintenance Requisition slip (MRS) for the same if required.
- After rectification of the fault, carry out the in-process check of the camera vision system and record the observation in the BPR, and attach the annexure.
- Re-open all the cartons that are quarantined and recheck all the blisters visually in the case of transparent PVC / pvdc/foil and by weight in the case of the PVC/ PVDC/ Aluminium foil.
Procedure for setting operation and cleaning of pinhole detector :
PINHOLE DETECTOR
- Fixes the intermediate holding plate for the guide track below the track.
- Ensure that the detection slot of the guide track and holding plate exactly coincide with each other.
- Place the transmitter unit on the guide track.
- Holding the receiver plate below the guide track.
- Connect the 10-pin D-connector cable to the connector fix on the transmitter.
- Switch “on” the power supply to the pinhole detector.
- Adjust the sensitivity of the pin holder detector, switch on the pinhole detector unit, and bring the numeric display mode on a screen.
- Ensure that the noise value displayed on the screen is as low as possible, ideally less than 300mv.
- Ensure that the shoulder level is to be approximately twice the noise value.
- Ensure that before starting the operation, the equipment is free from any foreign particles.
- Ensure that the transmitter and receiver unit are properly connected for the smooth flow of the product.
- Ensure the proper detection of any pinhole/tear/crack in the product.
- To adjust the threshold setting, Press the “edit” tab in the MMI of the blister packing machine.
- Press the “special function” Tab after pressing the “next “ tab.
- Press the “^” tab and then enter recipe” followed by “edit file.”
- Press the “v” tab and enter the count from the pinhole detector head to the punching tool in pinhole rejection offset.
- “load” tab after pressing the “save” tab.
- Clean the receiver detection slot with a dry lint-free cloth or soft brush to avoid the accumulation of dust on the screening slot after the completion of the batch.
Frequency:
- Test to be conducted for Alu-Alu base foil only at the start of the batch.
- At the end of the Shift.
- At the start of the Shift.
- At the end of the batch.
- There should be a Red Light glow on the pinhole detector when there is no fill-in pinhole detector and ensure the free moment of the Foil.
- Set the THR value three by using the upper Arrow and lower Arrow keys and press enter after selecting the value.
- Place that standard kit 100 Micron in between the pinhole detector.
- Pass the standard kit to the left-hand side slowly. Initially, when a standard kit of 100 Micron passes through the pinhole detector, the indicator should not light up.
- When the pinhole detector detects a 100 Micron pinhole, the red light on the pinhole detector should glow.
- If the result is satisfactory, proceed with the next steps. If the result is not satisfactory, recheck the settings of the pinhole detector and perform the challenge test again.
- Set the blister count from the pinhole detector to the punching station, make some pinhole/tear/ crack manually by using scissors in any one blister and check for detection of the same, and ensure that blister should be rejected at the punching station. It should be done to check the count of the blister.
- Check for the operation of the pinhole through PLC.
- Ensure the rejected blister gets collected in the rejection box.
- Start the operation only after satisfaction that found.
- Carry out the challenge test of the pinhole detector and record the observation in the annexure (if the challenge test passes right “ok” and if it fails right not ok).
- If the pinhole detector fails for the in-process check, then stop the machine and quarantine the quantity pack between the last satisfactory test and the present unsatisfactory test and put an appropriate status level on it.
- Rise the deviation and inform to engineering department through maintenance requisition slip for the same if required.
- After rectification of the fault, carry out a challenge test for the pinhole detector system and record the observation in the respective annexure (if the challenge test passes right ok and if it fails right not ok).
Abbreviations:
- Sop- Standard operating procedure
- PLC -Programmable Logic Control
- UPS -uninterrupted power supply
- ROI-region of interest
- PVC- polyvinyl chloride
- PVDC- polyvinyl dichloride
- Qs -quality system
- MMI -man-machine interface

Naresh Bhakar is the Founder and Author at Pharmaguddu.com, bringing his extensive expertise in the field of pharmaceuticals to readers worldwide. He has experience in Pharma manufacturing and has worked with top Pharmaceuticals. He has rich knowledge and provides valuable insights and data through his articles and content on Pharmaguddu.com. For further inquiries or collaborations, please don’t hesitate to reach out via email at [email protected].