Learn about Standard Operating procedure for the Water Purifier including their Scope, Purpose, Responsibility, Procedure, maintenance, calibration frequency, and Records used in various Industries and Pharmaceutical formulation Departments.
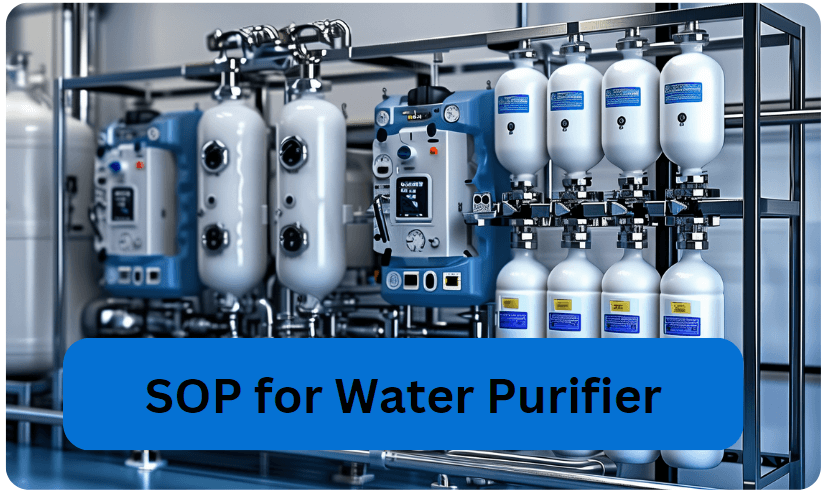
Purpose: To establish SOP (Standard Operating Procedure) for a Water Purifier intended to keep Reverse Osmosis water purification system in functional mode, To keep Water Purifier ready to use.
Scope:
This SOP is applicable for Water Purifiers (Reverse Osmosis water purification system) used in the pharmaceutical formulation process/Laboratory use.
Responsibility:
- Department Head: Responsible for preparation and implementation of this procedure.
- Quality Assurance: Responsible for review, approval, control, and release of this procedure.
- Machine Operator: Responsible for operation of the machine.
- Maintenance Head: Responsible for maintenance activities.
Accountability:
Management
Procedure:
- Check the water line for any obstructions.
- Check the pump rotation to coincide with the arrow on the pump.
- Verify all equipment is installed and operational.
- Tighten all plumbing fittings.
- Open pressure regulator valve on the panel, and ensure the optional recycle valve is partially open. Open pump throttling valves (if provided with your model) one-half open.
- Disconnected product (permeate) water tubing and directed to drain for the first hour only after starting up the system.
- Vent air from pre-filter housings using the pressure relief button.
- Turn the on/off switch “ON.”
- Verify the solenoid after the pump has opened and water has begun to flow through the system.
- When the RO high-pressure pump is turned on (it has a time delay to enable the unit to fill with water), the time has come to progressively close the pressure regulator valve by 2/3 open to reconfigure the balance of the system. (Remove valve cover with a wrench).
- On larger systems with pump throttling valves, begin to increase pressure by opening the gate valve to balance the system.
- Allow the unit to produce at 100 psi of pressure on the concentrate pressure gauge.
- Re-adjust the pump throttle valve to the correct specific recovery and permeate production rates indicated. (keep in mind, system pressure shall not be exceeded above 225 psi).
- Allow the unit to process water to drain for approximately one hour.
- Turn the unit ‘OFF’, reconnect the permeate line to the storage tank, and turn the unit back on.
- Allow to fill the storage tank.
- Monitor conductivity on the permeate line to verify 97% TDS reduction.
- Verify the level control turns the RO system ‘ON’ and ‘OFF’ when the high level is reached.
- Fill in the log sheet with the final flow, pressure, temperature, and conductivity readings.
- Water Purifier Control Panel includes the following:
- Power “ON” (Controller provides a 60-second delay, to allow for flushing).
- TDS / Timer (this is the key button that allows switching from the timer in the cumulative mode to the TDS counter). When TDS is exceptionally high, “99” will be indicated. Push the button again to switch to the accumulated timer display.
- Use the reset button to reset the accumulated timer.
Water Purifier LED Lights:
The following five lights are shown on the face of the controller:
- Tank full: Light is illuminated when the tank is full (Pick up a signal from pressure switch or level switch to stop the system when the storage tank is full).
- Flushing: Light is on during the period of time RO membranes are being flushed.
- Producing: the green light is present whenever the booster pump is in use.
- Water supply pressure is adequate: light is ON permanently while water is being supplied. When water supply pressure is not sufficient, the light will flash (Connect to the pressure switch to keep the system from running without incoming water).
Note: Pressure switch is set at the factory to activate when inlet pressure falls below 25 psi.
- Manual flushing: Light is on during manual flush of the RO membranes.
Controller Functions:
Flushing: Automatically accomplished when the tank is full, power is first turned on, and the system has been continuously running for twenty-four (24) hours.
Delay: This is programmed into the controller to provide a twenty (20) second delay when the tank is practically full or when there is a low water supply to prevent the system from picking up the wrong signal.
Maintenance:
- If the RO system will not be in use for 72 hours or more, store membranes in a 0.2% solution of Hydrogen Peroxide.
- Check the RO system daily and enter operational parameters in the Machine Log Sheet.
- The operators ought to pay attention to trends and make adjustments in case there is an increase in pressure, a decline in production, or even if the water quality begins to deteriorate.
- Monitor pressure gauges on pre-filters.
- Remember to change out activated carbon pre-filters every three (3) months.
- Check pump seals every three months. Note: It is advisable to change pre-filter cartridges when the feed water pressure differential doubles from the initial.
- Optional pressure gauge To better determine when this is necessary, an optional pressure gauge should be installed on the feed water line before the system,
Membrane cleaning:
- Washing out membranes externally at intervals can enhance the operational characteristics of the systems, Under conventional operation, mineral deposits, biological matter, colloidal and large macromolecules, and organics clog the membranes.
- Cleaning agents and chemicals are hazardous and can lead to bodily harm and property damage.
- Make sure to check safety and disposal instructions and follow them.
Inorganic anti-fouling cleaning:
- The inorganic salts of CaCO3, CaSO4, BaSO4, and iron-containing metal oxides from reverse osmosis membranes can be treated with an acid-cleaning solution.
- Do not use sulfuric acid since it may precipitate the calcium sulfate onto the membranes.
Recommended cleaning solutions for inorganic cleaning include:
- Solution of 0.2% Hydrochloric acid
- Solution of 0.5% Phosphoric acid
- Solution of 1.0% Sodium Hydrosulfite organic anti-fouling cleaning.
- Use a membrane cleaning solution that removes silica, biofilms, and organic matter using alkaline cleaning liquids.
Acceptable cleaning solutions for organic cleaning include:
- 0.1% Sodium hydroxide (NaOH) solution
- Solution of 0.1% sodium hydroxide (NaOH) and 0.1% tetra-sodium salt of ethylene diamine tetra-acetic acid (Na-EDTA).
- Solution of 0.1% sodium hydroxide (NaOH) and 0.05% sodium salt of dodecyl-sulfate (NaDDS)
- Solution of 1.0% sodium triphosphate (STP), 1.0% trisodium phosphate (TSP), and 1.0% Na-EDTA.
The above solutions should be that their pH should typically be 12 and the temperature of the solution should be less than 86 °F. Disinfection Hydrogen peroxide may be used for disinfection.
Records Related to Water Purifier:
- Machine cleaning records
- Machine log book
- Machine preventive maintenance record
- Machine maintenance -breakdown record
- Machine inspection records
- Water test reports
Don’t Miss This…

Naresh Bhakar is the Founder and Author at Pharmaguddu.com, bringing his extensive expertise in the field of pharmaceuticals to readers worldwide. He has experience in Pharma manufacturing and has worked with top Pharmaceuticals. He has rich knowledge and provides valuable insights and data through his articles and content on Pharmaguddu.com. For further inquiries or collaborations, please don’t hesitate to reach out via email at [email protected].