1.0 Purpose: To describe the procedure for decontamination of used material that comes in contact with API.
2.0 Aim: This Standard Operating Procedure is applicable for the decontamination of used material in the production department.
3.0 Responsibility: 3.1 Trained line coordinators shall carry out the decontamination process of used materials.
3.2 Officers/Sr. Officers shall be responsible to supervise the process.
3.3 Warehouse department shall be responsible for the decontamination of expired ARM/ liquid.
3.4 Manager Production shall be responsible for the implementation of SOP.
3.5 Head-Quality Assurance shall be responsible for the compliance of SOP.
4.0 Safety Consideration.
4.1 Wear safety equipment (goggles, Gloves, and nose mask) while handling the hot WFI and NaOH.
4.2 Take care while handling the glass accessories.
5.0 Procedure:
5.1 Decontamination of filling accessories Batch to Batch.
5.1.1 Receive the used filling accessories from the filling area through a dynamic pass box after completion of filling activities.
5.1.2 Paste the status label “TO BE CLEANED”.
5.1.3 Dip the filling accessories (which are directly in contact with the product) in 1 N NaOH for 40 to 45 minutes.
5.1.4 Clean the glass accessories with purified water and then wash the remaining accessories (First wash).
5.1.5 Wash the inner as well as the outer surface of filling accessories with high pressure of purified water.
5.1.6 Then wash the filling accessories with hot WFI from the outer and inner surfaces (second wash).
5.1.7 Send the final wash rinse sample to QC for testing.
5.1.8 Keep the cleaning accessories in racks and paste the status label “CLEANED”.
5.1.9 If any one of the tests fails follow the cleaning steps again till the results come positive.
5.1.10 After getting the release report from QC paste the label in accessories “RELEASED FROM QC”.
5.1.11 Pack all the accessories.
5.1.12 Keep the filling accessories under LAF for the next batch.
5.2 Decontamination of filling accessories in case of Product to Product :
5.2.1 Repeat step no 5.1.1 to 5.1.6
5.2.2 Then keep the washed accessories in a decontamination autoclave for decontamination.
5.2.3 Repeat Step no. 5.1.4 to 5.1.12.
5.3 Decontamination of glassware
5.3.1 Take out the glassware in the washing area through the dynamic pass box connecting the Material Air Locks of the filling area to the respective washing area.
5.3.2 Paste status label ‘To be decontaminated’.
5.3.3 The bottles which are used in ARM should be filled with WFI followed by alkaline extra solution or 1 N NaOH solution along with silicon tubing and siphon assemblies into the chamber of decontamination autoclave as per the validated load pattern in annexure-1.
5.3.4 Cap should be fitted loose on the bottle to prevent breakage.
5.3.5 Start the decontamination cycle.
5.3.6 After completion of the decontamination cycle unload the glassware and other accessories carefully.
5.3.7 Follow the cleaning procedure of glassware and other accessories.
5.4 Decontamination of Vials and syringes
5.4.1 Take out the rejected vials and syringes which come out for decontamination from the filling area in biohazard bags through the dynamic pass box.
5.4.2 Check the status label for the material if not present then paste the status label to be decontaminated.
5.4.3 Load the biohazard bags filled with syringes/vials into the chamber of decontamination autoclave as per load pattern No 02 given in annexure-1.
5.4.4 Start the decontamination cycle for the vials/syringes.
5.4.5 After completion of the decontamination cycle unload the material and send it for disposal.
5.5 Decontamination of Garments (Cleanroom dresses)
5.5.1 Take out the garments and booties which had accidentally (spillage during filling & formulation) come in contact with Active raw material into the biohazard bags from the de-gowning area.
5.5.2 Load the garments into the chamber of decontamination autoclave as per the load pattern in annexure-1
5.5.3 Start the decontamination.
5.5.4 After completion of the decontamination cycle transfer the garments to the laundry area as per the given SOP.
5.5.5 Wash the garments in the washing machine followed by drying them in the tumble dryer as per the “Washing, sterilization of clean room Garments” SOP.
5.6 Decontamination of expired ARM/Liquid
5.6.1 Receive the expired ARM from the warehouse.
5.6.2 Treat the expired ARM as per the given SOP.
5.6.3 Decontamination of the above-treated ARM as per the given SOP.
5.6.4 Fill in the format for the destruction of active raw material.
5.6.5 Transfer the treaded material to the effluent treatment plant for discarding.
6.0 Abbreviations:
ID No. : Identification number
No. : Number
QA: Quality Assurance
Rev.: Revision
SOP: Standard Operating Procedure
VFP: Vaccine Formulation Plant
DPB: Dynamic Pass Box
Annexure 1
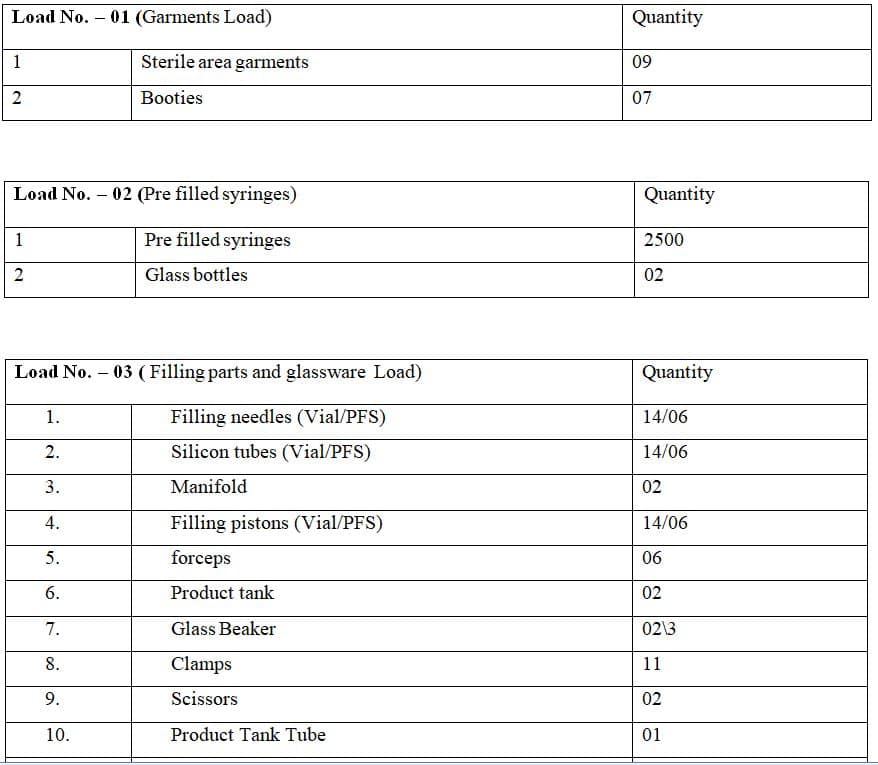

Naresh Bhakar is the Founder and Author at Pharmaguddu.com, bringing his extensive expertise in the field of pharmaceuticals to readers worldwide. He has experience in Pharma manufacturing and has worked with top Pharmaceuticals. He has rich knowledge and provides valuable insights and data through his articles and content on Pharmaguddu.com. For further inquiries or collaborations, please don’t hesitate to reach out via email at [email protected].