Learn in Detail about the Procedure (SOP) of Good Documentation Practices | Good Documentation Practices FDA Guidance | 5 Principles of Good Documentation Practices.
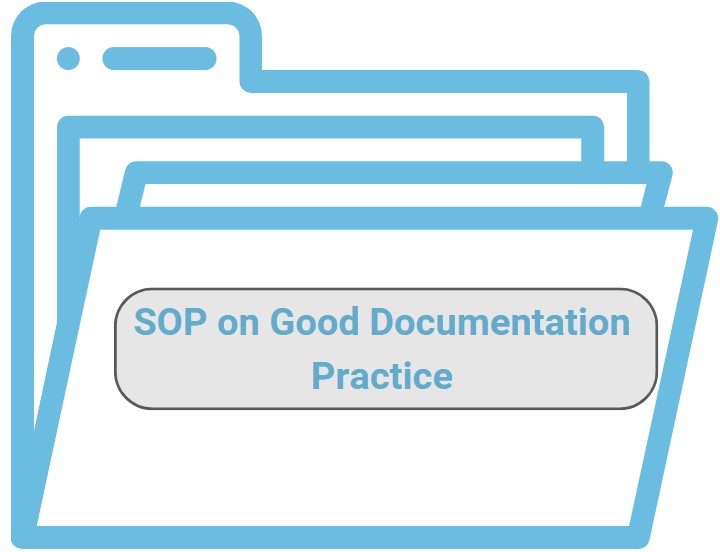
1.0 AIM: To lay down procedure on Good Documentation Practice in Pharmaceuticals areas.
2.0 PURPOSE: The purpose of this Standard Operating Procedure is to define the entry in the document records and correction in any documents.
3.0 RESPONSIBILITY
3.1 All employees of XYZ Pharmaceuticals involved in GxP are responsible for complying with Good Documentation Practices.
3.2 Respective Department Head:
3.2.1 To ensure that all personnel follow the GDP while GxP activity.
3.2.2 To ensure that all personnel involved in GxP activity are trained on GDP.
3.3 Central Quality. Technical Operations and Quality Assurance Head
3.3.1 To ensure implementation of this SOP at the site.
3.4 User Department or CFT Team:
3.4.1 To capture digital images using a digital camera.
3.4.2 To transfer digital images from the camera to a secured folder.
3.4.3 To issue forms for printing of digital images and take print of digital images on it.
3.5 Site IT:
3.5.1 To create a department-wide secured folder on the system or server for storage of digital images.
3.5.2 To ensure access control of secured folder is limited to personnel responsible for storage of digital images.
3.6 Site Quality Assurance:
3.6.1 To review print of digital images.
4.0 ACCOUNTABILITY
The head of all departments shall be responsible for overall compliance with this SOP.
5.0 DEFINITION (S)
5.1 Good Documentation Practices: GDP is a systematic procedure of preparing, reviewing, approving, issuing, recording, storing, and archival of documents associated with GMP activities.
Good Documentation Practices ensure that the documents are legible, accurate, consistent, authentic, and complete. Following Good Documentation Practices enables the preparation of the documents and making entries of data in a legible and traceable manner.
5.2 Document: A piece of written, printed, or electronic matter that provides information or evidence or serves as an official record.
5.3 GxP: Good x Practice (where x represents the function e.g. Manufacturing, Laboratory, Documentation, etc.).
5.4 Data: The information generated for quality evaluation and decision.
5.5 Raw Data: Original records and documentation, retained in the format in which they were originally generated (i.e. paper or electronic), or as a ‘true copy’.
- It is the original record (source data) that can be described as the first capture of information, whether recorded on paper or electronically.
- Raw data must be contemporaneously and accurately recorded by permanent means. In the case of basic electronic equipment which does not store electronic data, or provides only a printed paper data output (e.g. balance or pH meter or chart recorded), the printout constitutes the raw data.
5.6 Objective Evidence or Supporting Documents: Objective evidence is information that is verifiable and generally consists of records, direct original printouts from equipment, electronic data of the activity performed, and other statements of fact that are relevant to the criteria being used or referred.
5.7 Secondary Data: Data that had been constructed from raw data for analyzing the information for its intended purpose or to facilitate trends or conformity to the requirement.
5.8 Electronic Record: All original records and documentation, including data directly entered into the computer through an instrument interface, which is the result of original observations and activities and necessary for reconstruction and evaluation of raw data.
Metadata: Metadata is data that describes the attributes of other data and provides context and meaning. Typically, metadata is data that describes the structure, data elements, inter-relationships, and other characteristics of data. It also permits data to be attributable to an individual.
5.9 Metadata is structured information that describes, explains, or otherwise makes it easier to retrieve, use, or manage data. Data should be maintained throughout the record’s retention period with all associated metadata required to reconstruct the GMP activity. The relationships between data and their metadata should be preserved in a secure and traceable manner. An audit trail record is an example of metadata.
5.10 Migration: The transfer of electronic records from one format, media, or computer system to another.
Archival: Archiving is the process of protecting records from the possibility of being further altered or deleted and storing these records under the control of independent data management personnel throughout the required retention period.
5.11 Archived records should include, for example, associated metadata and electronic signatures.
5.12 Data Reliability Elements/Principle (ALCOA ++):
5.12.1 ALCOA element includes:
*Attributable_to_the person or system generating the data. It clearly indicates who recorded the data or performed the activity, and who wrote it.
It identifies the person or systemic performing an activity that creates or modifies. It is linked to the source of data:
*Legible data is clear, concise, permanent, and readable. The data is legible state shall be accessible throughout the data lifecycle. It also indicates that original data and any subsequent modifications are not obscured while making changes.
*Contemporaneous observed, recorded, and documented at the time of activity performed. This documentation should serve as an accurate. attestation of what was done, or what was decided and why, i.e. what influenced the decision at that time.
*Original data is the first recording of data or a ‘true copy’ (certified copy) which preserves content or meaning. Original data can be recorded on paper or generated electronically.
*Accurate data is free from errors which confirms the truth and standard for data being captured. It also ensures that no modifications are done without documented amendments and justifications. It ensures that data are correct, truthful, valid, and reliable.
*Complete_data refers to the dataset having all data and relevant metadata including any repeat or reanalysis performed. It refers to the data set where nothing is omitted. It includes all the data generated before a problem is observed, data generated after repeating part or all of the work, or re-analysis performed on the sample contained in the data record.
*Consistent means all elements of the analysis, such as the sequence of events, follow on and data files are date and time-stamped in the expected order. It includes the application of good documentation practices throughout any process.
*Enduring means data recorded in a permanent, maintainable form for the retention period. It ensures that data is recorded on authorized media, which can be preserved for a period of time. Data recorded on other than respective authorized media are not considered enduring.
*Available means data (complete collection of records) is available and accessible for review and audit or inspection throughout the retention period.
5.13 Transcription of Data: Transfer of the data information from one document to another document as per the requirement is a transcription of the data.
5.14 Records: Records include the raw data which is used to generate other records. It provides evidence of various actions taken to demonstrate compliance with instructions, e.g. activities and in the case of manufactured batches a history of each batch of product, including its distribution.
5.15 Reports: Document the conduct of particular exercises, projects, or investigations, together with results, conclusions, and recommendations.
5.16 Dynamic Record Format: Records in dynamic format, such as electronic records, that allow for an interactive relationship between the user and the record content. For example, electronic records in database formats allow the ability to track, trend, and query data; chromatography records maintained as electronic records allow the user to reprocess the data, view hidden fields with proper access permissions, and expand the baseline to view the integration more clearly. Other examples of dynamic records are spectrum, histogram, electronic logbook, BMS data, alarm logs, PLC data (stability chamber monitoring record), etc.
5.17 Static Record Format: A static record format, such as a paper or PDF record, is one that is fixed and allows no or very limited interaction between the user and the record content. For example, once printed or converted to static PDFs, chromatography records lose the capabilities of being reprocessed or enabling more detailed viewing of baselines or any hidden fields. Other examples of static records are QC worksheets, paper logbooks, weight prints, printouts from validated Excel sheets, cleaning records, etc.
5.18 Digital Image: Digital image means any photograph taken using a digital camera.
6.0 PROCEDURE
6.1 Documentation may be divided into:
6.1.1 Documents-procedural or instructional, specifications, master plans.
6.1.2 Logbooks/records-evidence of compliance.
6.1.3 Reports- summary reports such as validation reports, investigation checklists, and reports, or any other kind of report.
6.2 Documentation shall always be done in accordance with the applicable written procedures following ALCOA ++ elements. Good documentation practices shall be followed in order to ensure all records (both static and dynamic) allow the full reconstruction of related activities.
6.3 General requirements for GxP documents:
6.3.1 All Master documents shall be typed or preprinted. The document shall be printed in black ink on white A4-sized paper. Modifications/ changes/corrections in the master document shall be carried out through a change control procedure only. No handwritten corrections shall be allowed to master documents.
6.3.2 Master documents (paper-based and electronic) shall be stored in a secure manner and accessible to authorized individuals.
6.3.3 The font size of the documents/records shall preferably be 12 with “ Times New Roman” font.
6.3.4 All instructions/master documents shall be written clearly and shall have an identification number, version number, effective date, and revision history.
6.3.5 All documents shall have page numbers in X or Y format to indicate the total number of pages in a document.
6.3.6 Attachments to a document shall have a reference to the parent document and the parent document shall have reference to the attachments.
6.3.7 The date format shall be as follows as per the annexure given SOP.
6.3.8 Fountain ink pens, gel pens, flair pens, and pencils shall not be used for documentation. Quality assurance personnel shall use a ballpoint pen having black color ink (Black ballpoint pen). Other departments including corporate quality shall use ballpoint pens having blue color ink (Blue ballpoint pen). The quality assurance person shall ensure that a minimum of one signature shall be in blue ballpoint pen on the approval page. For this case, the quality assurance person shall do a signature with a blue ballpoint pen. For example, Any document that is prepared by, reviewed by, and approved by quality assurance shall be signed as below;
Here’s the table based on the provided image:
(Ballpoint pen – Black color ink) | (Ballpoint pen – Black color ink) | (Ballpoint pen – Blue color ink) |
Prepared By | Review By | Approve By |
Quality Assurance | Quality Assurance | Quality Assurance |
This table shows the type of pen and ink color used for different documentation steps, along with the responsible department (Quality Assurance).
6.3.9 A document for review shall bear a watermark as “DRAFT” or stamp as “DRAFT” on all pages. Once the document is approved, the “DRAFT” version shall be destroyed as per point no. 6.17 and 6.18.
6.3.10 During the final review and approval of GMP documents, if the reviewer/ approver wants to give comments then it shall be signed and dated. Once the updated GMP documents are approved, the commented copy shall be destroyed as per points No. 6.17 and 6.18.
6.3.11 While performing photocopy or scanning, the legibility of the photocopy/scan document shall be ensured.
Note-1: In case of taking printouts from a printer attached to equipment/instrument, check print quality at start of shift. If the print is not legible, do not proceed further and take appropriate actions ie. change of cartridge, tonner ribbon, etc.
6.4 Entry into a GMP record [ log Books, batch records, etc.]
6.4.1 The information, data, or any information in all documents and formats shall be written contemporaneously, accurately, and maintained in a manner that prevents errors and ensures consistency.
The document shall be:
- Attributable to the person instrument device that is generating the data.
- Legible and permanent in sequential chronology.
- Contemporaneous.
- Original (or ` true copy”) (un-tampered), unaltered, and trailing to the activity; date and time stamping.
- Accurate.
- Complete, consistent, enduring, available
6.4.2 All records shall be filled in indelible ink for long-term legibility.
6.4.3 Recording formats shall be designed so as to provide sufficient space and provision to record entries, signatures, and record date/time (as applicable).
6.4.4 Recording of data on blank space of issued document shall be exceptional. However, when recorded such data shall be signed and dated by person making entry. Checker (if applicable) and reviewer shall also sign and date at such entry.
6.4.5 Documents shall have critical significant steps identified, which shall require a check by a second person while performing the task.
6.4.6 The GxP data shall be recorded directly in the approved and authorized format such as batch records, log books, test data sheets, validation formats, and no data shall be recorded in unauthorized format/paper/mote books /personnel diaries.
Any observation/malfunction that occurred during during activity (manufacturing activity/analysis/CIP etc.) shall be contemporaneously recorded in the respective document (i.e. BMR/BPR process history sheet, QC worksheet, logbook, etc.)
6.4.7 Any alteration made to the handwritten entry on a document shall be by making a single line through the error followed by signed and date.
6.4.8 The alteration shall permit the reading of the original information. The reason for the alteration shall be recorded.
6.4.9 Data shall recorded as observed as per activity performed. There shall not be any alteration or change in observed value and recorded value.
6.4.10 All attempts of activity shall be recorded in GMP documents. It shall cover activity that is repeated, before or after any problems occur, etc.
6.5 Time of entries
6.5.1 All the entries shall be made contemporaneous i.e. the data shall be recorded at the time the work is performed and date and time stamps shall follow in the order in the chronology of how the activity was performed and shall be legibly signed and dated.
6.5.2 Under no circumstances may entries be made before a step is performed.
6.5.3 Update of any record and document, signature, date, recording data, observation; after completion of activity shall be done concurrently. Any back-dated event shall be considered falsification.
6.5.4 Mention time in 24-hour format in documents as HH: MM For example for afternoon 2:30 PM; write as 14:30 hours. Change of date shall be made after 00:00 hour.
Note 2: Time shall be recorded from the synchronized and calibrated company clock/device provided in the area where the activity is being performed and not from the personal watches.
6.5.5 In case operations are continued from one shift to another where the dates are different, the date shall be recorded along with the timing if a separate date column is not available.
6.5.6 If any activity is completed in part by one individual and further executed by another individual, both persons shall sign a document for the respective part.
6.5.7 If any column or row or cell of a format is “Not Applicable“, NA shall be written with a sign and date in the provided format.
6.5.8 Multiple blank spaces/rows/columns on a record must be marked out with a diagonal single line across the whole field/space. Mark NA along the line and sign and date to show the filed/space is not applicable.
6.5.9 Where reason for making NA is not obvious a brief justification for such action shall be mentioned. This shall indicate that not completing a page or section or cell is deliberate and a record cannot be added to it at a later date.
6.5.10 In records the actual observations shall be recorded. Only putting remarks such as OK/Not OK, Comply, Done, etc. shall not be acceptable. However in certain formats such as checklists where the activity is to be conducted and recorded. Yes or No shall be written indicating whether the activity was performed or not performed. The same shall be signed by the person executing the checklist.
6.5.11 The following practices are prohibited:
- Use of ditto……”….. marks to fill repetitive entries.
- Use of ear bracket {} is not allowed for signature against multiple entries.
- Use of pencil or any removable/water-soluble ink.
- Use of eraser or ink remover/whitener.
- Recording of the data on unauthorized documents (post-it notes, sticky sheets, scrap paper, loose paper, personnel notebook, filed notebook, uncontrolled copy, reference copy, draft copy, etc.) glass board, and black/whiteboard.
- Overwriting, multiple crossing of the original entry/data.
- An entry made by a person on a GMP document but not signed and dated by the person who has made the entry.
- Recording data that is not in chronology as per process steps or not in sequential date and time manner.
6.5.12 Quality assurance shall randomly verify online documentation for the following aspects:
- Correctness.
- Accuracy
- Traceability.
- On-Time.
The quality assurance person shall sign and date on the right-hand margin of the document near the entry being verified. He/she may verify the completeness and correctness of the document since its previous check.
6.6 GMP documentation
6.6.1 All GxP activities shall be carried out with the approved current version of the instruction documents and the recording formats.
6.6.2 Paper having a specified colored watermark shall be used for printing/photocopy of documents as per Annexure. (Paper color for printing/photocopy of documents).
6.6.3 In the case of manufacturing, the instructions as written in the applicable/reference SOPs, and batch records shall be followed, step-by-step and documented concurrently.
6.6.4 For analysis, procedure, as given in the applicable SOP, GTPs, and STPs, shall be followed sequentially and observations/data shall be documented concurrently in the analytical data sheets and/or laboratory notebooks applicable).
6.6.5 The recording in manufacturing and testing records, calculations shall be complete and legible. Entries made in computerized systems such as (SAP)/LIMS or any other computer-based system (as applicable) shall be traceable to raw data.
6.6.6 Any correction to such data, once saved on the system shall be allowed through written authorization by quality assurance. The person who has made and saved the data shall not be allowed to edit the data/information, once saved in the system.
6.6.7 The audit trail for corrections made shall be maintained with justification /reason. e.g. correction in value of a parameter during review for any decision making.
6.6.8 The raw data generated as a part of the documented evidence for any activity, records shall not be destroyed and shall be retained as per the prescribed retention time for each set of the record.
6.6.9 Only validated MS® Excel sheets shall be used for the calculations. Wherever such MS® Excel sheets are not available, calculations shall be verified with calibrated calculators by a second person.
6.6.10 All weight slips, printouts, chromatograms; spectrum shall be signed after completion of the activity. Printout pasted in the record shall have signature across printout.
6.6.11 Any disregarded data shall be stamped as “DISREGARDED” with sign, date, and reason. Investigation No. shall be referred whenever applicable. Such data shall be included in the review package.
6.6.12 Rounding off of the numerical values and decimal reporting shall be done as per applicable SOP.
6.6.13 The document where a validity period is assigned shall be reviewed before the due date. Such documents may be revised or revalidated.
6.6.14 Changes to the approved documents shall be made through change control procedure and the revised version shall supersede the previous version. Copies of the superseded documents shall be retrieved and destroyed as per point no. 6.18 for the document destruction process.
6.6.15 Superseded master documents shall be archived with quality assurance department.
6.6.16 It shall be the responsibility of the personnel making use of the documents to see that the documents are maintained without any damage.
6.6.17 All documents shall be retained as per the defined retention period and on expiration of the retention period it shall disposed of as per SOP titled as “Review period and retention period of documents and records“.
6.6.18 E-mails used as a GMP system of record, shall be printed, signed and dated, and attached with original reports. Wherever these e-mails are scanned or attached to any electronic QMS in those cases sign and date are not required.
For example:
- If e-mail is used as the official system for escalation of quality issues per a firm’s SOPs, then those e-mails are GMP records.
- If e-mail is used for informational purposes to note that there has been an escalation, and there is a separate system of record for escalations, then the e-mail is not a GMP record.
6.6.19 All documents shall be retained as per the defined retention period and on expiration of the retention period it shall disposed of as per the applicable SOP.
Note-3:
- Do not destroy/delete a record/document/report because of any error/mistake; it is still required for traceability.
- Deliberately amending or destroying records/ documents/reports to hide or falsify data shall lead to disciplinary action.
6.7 Handling of attachments
6.7.1 Indicate on the original document that there is an attachment.
6.7.2 Attach one record to another e.g. if a record is to be attached to form: cross refer the record with the form e.g. the record shall have the reference of the form and form shall have reference of the record.
6.7.3 If raw data print slip artwork specimens are to be enclosed with the records e.g. batch records, records of analysis, qualification documents, etc., these shall be affixed at the specified space designated for the same.
6.7.4 All multiple-page data sheets or instrument printouts in paper form shall be signed and dated on first or last page with a note indicating the total number of pages. Each page shall have the title of the document/record.
6.7.5 Ensure sufficient identification on the attachment to ensure traceability in the event it becomes separated.
6.7.6 Compile all pages of a document/record along with the relevant attachments in chronological order in the file.
6.7.7 All printouts taken on thermal paper shall be signed and same shall be photocopied for attaching it to a batch record /report or filing so that the original information is retained. The thermal paper shall be attached along with the photocopy.
6.7.8 The photocopy shall be marked as “COPY OF ORIGINAL” along with initial and date. The thermal paper shall be attached along with the photocopy. Information on thermal paper shall not be taped over, since the tape shall cause the data to fade rapidly.
6.8 Handling blank forms
6.8.1 Quality assurance and in case of software authorized person responsible for issuance shall ensure that pages with water mark logo are kept in a controlled area/location.
6.8.2 Blank forms (including, but not limited to worksheets, laboratory notebooks, master production, and control records) shall be controlled by the quality assurance unit. Pages with colored watermark logos shall be used for controlled printing. Blank pages having colored watermark logos shall be kept under the control of Quality Assurance.
6.8.3 For example: Numbered sets of blank forms shall be issued as appropriate and shall be reconciled upon completion of all issued forms. Incomplete or erroneous forms shall be kept as part of the permanent record along with written justification.
6.9 Handling of torn/damaged and spoiled documents:
6.9.1 If any document or record has been torn/damaged during handling deviation shall be raised. All portions of the relevant pages shall be joined with transparent cello tape and a photocopy of the page shall be taken and signed off with justified reason in the footnote of the document, treating it as original document. It is necessary to retain the original pieces /portions of such pages along with a photocopy of the document.
6.9.2 In case of spillage on any document thereby making the entry illegible deviation shall be raised. Re-issuance of the format shall be requested to quality assurance with reference to the deviation number. The spoilt copy shall be retained along with the new copy. Data shall be transcribed as per point
6.10 Signature practices
6.10.1 Signature essentially means that the signatory is responsible for the accuracy of the data and information for the activity being signed for. Hence signatory shall confirm the correctness, completeness, and traceability of information /data/content before signing.
6.10.2 Sign/Signature:
- The signature identifies the person who made the entry in the logbook.
- Sign’signature can be used only in case of logbooks or labels where the signature indicates that the entry in the logbook is done by the person signed under the column.
- All entries shall be made promptly (contemporaneously), and up to the stage which is completed; the entry shall be sequential. e.g. Equipment logbook, deviation logbook.
6.10.3 Quality Assurance shall maintain a “Signature Specimen record for short (initial) and full signature” wherein each employee involved in GxP activities shall give a specimen of his/her signature and initials to ensure that the signature is traceable to a member of staff.
6.10.4 For any activity document /record, a person shall sign and date the document/record as “Done By” or Checked By“,”Checked and Recorded By ”, “ Verified By“,”Reviewed By“,” Approved By“. The same person shall not sign for multiple roles for one activity. Each signature in the document shall indicate reason for sign being made e.g., done by, checked by, reviewed by, etc.
6.10.5 There is no need to put date with sign where date and time column are maintained in the record. E.g. Training attendance sheet.
Note: Persons using “Electronic Signature” should note that these electronic signatures are legally equivalent to the signer’s traditional handwritten signatures.
6.10.6 Done By: Done by means performed by and the person is a doer.
- The doer is a person who is responsible for the activity by means of preparation, doing, or performance. In laboratory for person performing analysis, “Analyzed by” term can be used. In case of documents for person preparing document, “Prepared by” term can be used.
- Doer is personnel proficient in the task performed or the personnel who is under training and supervision of their qualified trainer.
- The done by signature, identifies the person who actually did the work and documented it; which is represented by the signature of the person executing an operation or task. The done by signature is attributable to the person performing the activity or generating the data.
- The doer is the person who actually performs the activity and shall record or make entry of observations him/her followed by signature and date.
- All entries shall be made promptly, completely at the time the procedure or activity is performed by the person performing the activity and shall clearly represent the activities executed and shall write him/herself contemporaneously e.g.:
- Performing an act of monitoring and recording of observations such as temp, pressure, RPM, etc.
- Physically adding the material to the Bowls, containers; cleaning the parts and equipment under the instructions of the officer supervisor. Performing the analysis of the samples.
- Weighing of the material.
- In-process checks performed by the quality assurance person are doer activity.
6.10.7 Helper or Assistant: To give assistance (to the doer); helper makes it easier for (doer) to do the physical activities.
- Helpers are the persons doing the motor activity and helping the doers/ supervisor in physical handling; such as moving of trolleys, lifting bags, lifting of containers; as the helper is only performing the physical motor activity in the sense of the “definition“; the officer/person getting this actives done with instructions shall be the”Doer“.
6.10.8 Checked By: The checked by signature identifies the person who ensured that the work was performed and documented correctly. It identifies the person who witnessed the activity being performed.
- A checker is a person proficient in the task performed and has been trained to perform the activity.
- Checker verifies that the doer has recorded contemporaneously.
- Checker has watched/witnessed the activity being performed.
- The checker may also perform the “supervisory recording“.
- For the checker to sign, it is must to have doer signature. The checker cannot be the only individual to sign the document.
- Checked by signature shall be done on actual date and time.
- All the critical stages/steps shall be checked by another person: Examples of activities that need a checker signature:
- Weighing of individual materials.
- Entry of process critical manufacturing parameters.
- Verification of the identity of each component or material that shall be used in a batch.
- Verification of the addition of each individual raw material to a batch (e.g. when the sequence of addition is considered critical to process control).
- Addition of multiple pre-weighed raw materials to equipment when required as a single manufacturing step.
- Critical and batch decision defining QC tests where supportive evidence (printout out for electronic data) not available e.g. Titration, recording microbiological count manually, turbidity measurement.
- For or a validated automated system that is integrated with the recorded data and or if by its design, construction, operations and security features the procedure is such that it is validated and the system assures that it is impossible to make an error, and an electronic or direct printout supports the performance of the activity done by the doer, then an independent check by another person may not be considered necessary.
6.10.9 Checked and recorded by: Checked and recorded by means the “Supervisory Recording” (Recording by Scribes).
- Checked and recorded by is the initials or signature of a person, who is checking or supervising the activity and recording the information of the activity performed, and the readings of an operation which are recorded contemporaneously.
- “Checked and recorded by” is used only if the operator (Doer) performing the operation is unable to record the raw data and to initial and date immediately, due to working in a confined or restricted space, or to avoid intervention in the process.
- Use of ‘supervisory recording’ (scribes) to record activity on behalf of another operator shall be considered ‘exceptional’ and only take place where:
- The act of recording which places the product or activity at risk e.g. manufacturing steps-such as the addition of material in batch or documenting line interventions by operators.
- The supervisory recording must be contemporaneous with the task being performed and must identify both the person performing (done by) the observed task and the person completing the record (checked by) (Supervisor signature). Only when the “supervisory recording” is permitted; the person performing the task (doer) shall countersign (i.e. sign as doer) the record, although it is accepted that this countersigning step shall be after completing the activity or sequence of activities.
- Each department shall be maintained list, of the activities to which the process of “supervisory (scribe) recording” of the documentation applies [ Refer to Annexure, Supervisory (Scribe) Recording Activity List]. This shall be preapproved by Quality Assurance.
6.10.10 Verified By: The verified by signature identifies the person who ensured that the work was performed and documented correctly.
- Verifier is a person proficient in the task performed and has been trained to perform the activity.
- Verifies that sequential steps were performed and the doer has recorded the entries, based on objective evidence, associated records/logs.
- Verified at end of the specific activity/process to ensure that activity has been completed satisfactory as specified in the respective GMP document.
- The verifier cannot perform the”supervisory recording”.
- For the verifier to sign, it is must to have doer signature. The verifier shall not be the only individual to sign the document. eg.: Line Clearance by quality assurance is “Verified By“.
6.10.11 Reviewed By: The reviewed by signature identifies the person who ensured that the work was performed and documented correctly (possibly at a later time).
- Reviewed by is the initials or signature of the person who reviews the document or record in order to confirm its accuracy and completeness, clarity and legibility, inducing checking the calculations.
- Is a person who is responsible for reviewing the documents based on evaluation of supporting data/documents/references attached and the checker comments.
- Reviewer is personnel proficient in the task performed and has been trained to perform the activity.
6.10.12 Approved By (or Authorized By): The approved by signature identifies the person who evaluates the work performed to ensure it was done accurately, completely, and in accordance with procedures and/or documentation practices.
- Approved by indicates approval to proceed to the next stage process.
- Is a person who is responsible to approve or authorize the documents based on evaluation of the critical steps, summery, final conclusion or comments by the reviewer.
- Approver may also review the documents for clarity; understanding and decision making.
- Approver is personnel proficient in the task performed and has been trained to perform the activity.
6.10.13 Designee: Designee is a person who is allocated signature and decision making authority in absence of his/her superior as per deputation matrix. Deputation matrix shall be prepared by site and support functions. The allocation of designee is based on his/her knowledge, experience and competency; the designee shall be from the same function.
6.10.14 In case of continuous processes for long duration (completed in more than a shift operation) e.g. dissolution test; routine monitoring records, the final print out on completion of the activity shall be taken. This print out shall be signed and dated by the person who prints the document. Such print out shall be attached to the record, where applicable.
6.10.15 Signature for all GxP activities shall be accompanied by the date, even if the separate date column has not been provided.
6.10.16 Unsigned documents or records are incomplete and shall not be used to perform any task or as an evidence for completed task.
6.10.17 Following signature practices are strictly prohibited: Signing not as per the specimen in the”Signature Specimen Record.”
- Signing for an activity performed by another employee.
- Signing for an activity in advance (i.e. signing with a non-current date) or signing for an activity with a back date (i.e. signing with a non-current date).
- Signing someone else name unless it is a designee or the notations is clear that the person has signed on behalf of the person.
6.10.18 Obtaining signature approval on scanned documents: Approval signatures from the staff located at different site locations time zones can be completed using scanning. Following procedures shall be adopted for the Same:
- Print the document to be approved.
- Sign and date the hardcopy and send the scan copy of the document to the appropriate signatories through mail.
- Signatory shall print, sign and date the document and send the sean to the sender.
- The approval page from each signatory shall be attached to the original hard copy and column shall be written as “Refer Signature on Sean Page“.
6.11 Handling field note books
6.11.1 Field notebooks are numbered, paginated, and bounded notebooks issued by the Quality Assurance department to a particular individual.
6.11.2 Quality Assurance shall keep all blank and retrieved FNB in a controlled area.
6.11.3 Such notebooks shall be used only for writing of day-to-day action items, notes during meetings, learning from training, instruction for planning of activities, notes during external audits etc.
6.11.4 FNB shall not be used for recording of any of the GMP observations, records, data, findings, investigations, monitoring values, or initiation of any GMP activity.
6.11.5 The GMP data shall be recorded only in the approved and authorized format such as batch record, log book, test data sheet, validation format, SOP format, and investigation forms.
6.11.6 Numbering of FNB shall be done as per Annexure.
6.11.7 Quality Assurance shall mention required detail in issuance log (Amexure-10) and initial book page (Refer to section A of Annexure. User shall receive FNB.
6.11.8 User shall perform sign and date on each book page after completion of page.
6.11.9 FNB shall be used by particular individual to whom it was issued. FNB shall not be shared with other employee for any type of writing.
6.11.10 All pages shall be used in chronological order.
6.11.11 The section head shall periodically review the FNB of each individual to ensure that FNB does not have any GMP record. The section head shall sign and date on the left-hand side of the bottom margin of last reviewed page.
- During the review, if any GMP data found recorded in FNB, a deviation shall be logged and an investigation shall be carried out as per the current version of SOP on “Handling of Deviation”.
- Based on the investigation, where required such filed notebooks shall be retained up to retention period applicable for respective GMP data which is recorded in field notebook.
6.11.12 The FNB shall be returned back to Quality Assurance every 3 months ± 7 days from date of issuance or before if it is full (whichever is earlier).
6.11.13 Section Head shall review FNB and provide review comment in initial page of FNB Refer to section B of Annexure.
6.11.14 Quality Assurance shall review the section Head comments on the submitted notebook.
6.11.15 Quality Assurance shall certify returned FNB for destruction (Refer to section C of Annexure within 15 days from date of receipt.
6.11.16 Quality Assurance shall retain a photocopy or scan of the first page of FNB (FNB issuance and retrieval record) for a minimum of 2 years.
6.11.17 Record of FNB destruction shall be maintained in the destruction record.
6.11.18 Respective Section Head shall ensure submission of FNB to Quality Assurance while employee relived from the organization.
6.12 Guidance on how to correct the errors
6.12.1 Refer Annexure (Guidance on how to correct the errors) for correction of errors. Review of executed documents and trending of errors
6.13.1 Errors or observations identified during review of executed documents (batch record, analysis record, validation report, qualification report etc.) shall be recorded in Annexure (Document Review Sheet).
6.13.2 During first review if any error identified then doer and checker/verifier of the activity shall be mentioned as responsible person in Annexure. However during subsequent review if any error identified, then previous reviewer (s) of document shall be mentioned as a responsible person in Annexure. Errors shall be further corrected as per Annexure (Guidance on how to correct the errors) and Annexure (Example of Good Documentation Practices).
6.13.3 Each department shall prepare trend of error observed during document review on at least a quarterly basis. Refer to Annexure (Example for Trending of GDP Errors) for example. Trend shall be reviewed by respective department head and quality assurance for further action improvement.
6.14 Handling correction in approved and master document:
614.1 In case of any error observed in approved and master documents e.g. SOPs, Batch manufacturing record, batch packing record, specification, STP, SMF, validation master plan, etc. then Annexure (Error Ratification Form) shall be filled.
6.14.2 Sequential numbering, log, and traceability of ERF shall be maintained by Quality Assurance as per Annexure (Log for Error Ratification Form).
6.14.3 Numbering for Error Ratification Form: ERF/XXXX/YYZZZ, Where ERF stands for Error Ratification Form followed by/ XXXX stands for site code (Numerical number) as mentioned in SAP followed by/ YY indicates last two digits of the current Year (e.g. 24 for 2024).
ZZZ is the sequential number starting from 001 of each calendar year.
For Example:
- Site having SAP code 0301, first Error Ratification Form
Number of year 2024 shall be ERF/0301/24001.
- Site having SAP code 0302, first Error Ratification Form
Number of year 2024 shall be ERF/0302/24001.
- Site having SAP code 0302, first Error Ratification Form
Number of year 2025 shall be ERF/0302/25001.
6.14.4 Methodology of rectification of error shall be recorded in Annexure (Error Ratification Form) e.g. updating the documents, preparing addendum, training etc.).
6.14.5 Photocopy of approved error ratification shall be attached and retained with respective document.
6.14.6 The original error ratification form shall be maintained by Quality Assurance.
6.14.7 Errors which lead to confusion or complete deviation from actual meaning or have direct impact on product quality shall be routed through deviation procedure,
6.14.8 If document is filed or submitted to regulatory agencies; the corrections shall not be done on the original document or on the copy submitted to regulatory agency. Deviation shall be raised and document shall be updated with correct value with reference of filled deviation.
6.14.9 Depending on nature of error, impact assessment shall be performed. Whenever required regulatory agency shall also be notified.
6.14.10 However if any discrepancy is observed during an ongoing activity in such master document, an annotation mark near the error shall be put and the correct information shall be presented with reference to ERF number. If required prepare and attach an addendum with the document with correct data/ information, duly authorized by Quality Assurance. For particular correction, the addendum shall be referred to perform the activity.
6.14.11 Not more than three ERF shall be allowed for a single master document.
6.14.12 Quality Assurance shall prepare trends of ERF (status vise, department wise, type of document wise, etc.) on at least quarterly basis to review status and identification of further action/improvement.
6.15 Transcription of the Data
6.15.1 In case of need to transcribe the data information,(for example form batch record to process validation summary) the data shall be taken from the original source document and transcribed data shall be verified, signed, and dated by a second person for completeness, accuracy, and traceability.
6.15.2 The transcribed data/information shall be legible and accurate in terms of date, quantity, figures, observation, etc.
6.15.3 If original record, transcribed document is soiled during handling; report the deviation. Retain the original soiled document; attempt shall be made to transcript the details from raw data, computerized data, and original Document.
6.16 Electronic documents
6.16.1 The documents control electronically shall be maintained securely with an audit Trail.
6.16.2 If a document format is issued or controlled by an electronic system or is processed for information flow approval, the personnel authorized for issuance or control of such document shall be allowed to take print, enter data, and/or generate the report.
6.16.3 Document/format control by electronic system/ software shall have proper user authorization level/matrix and individual users shall be assigned based on role and responsibilities.
6.16.4 In case a format is required to be issued again, it shall be through a fresh requisition with reason and justification. The fresh format shall be issued after written authorization by Quality Assurance.
6.17 Destruction/Shredding of Documents
6.17.1 All the documents due for destruction shall be destroyed in a controlled manner. This would include, at a minimum, identification of the appropriate documents and retention timelines, documentation (listing) of what and when was destroyed, and the names and signatures of those who performed and witnessed the destruction.
6.17.2 GMP documents
- Documents within validity/retention period:
- Shall not be destroyed and shall be retained as per SOP titled “Review period and retention period of documents and records“.
- Changes to the Quality Assurance approved reports shall be through change control only and with version control e.g.: Qualification and process validation Report: Errors identified can be corrected through change request form only.
- Documents after the validity/retention period of the documents. E.g. SOPs retrieved copies can be destroyed as per the SOP titled “Review period and retention period of documents and records“.
- Direct Printouts from instruments/machines as raw data, shall not be destroyed and shall be retained with respective GMP documents.
6.17.3 Documents which are not retained:
- Status labels that are changed after change/modification in status as per SOP (area status label or sanitization/ cleaning agent labels).
- Cleaning labels post validity.
- The user shall not directly destroy status labels used at different levels of the process. The user shall defile the same with a cross “X”, sign, and drop whole in the drop box.
- Documents with comments (comments received from reviewer/ approver during final signatures as per point no. 6.3.10)
6.17.4 Working documents which are Non GMP documents:
- Email copies (Generated for information and not to satisfy a GMP requirement).
- Typed reports or documents Prior to approval by quality assurance which are stamped with a draft watermark or crossed and marked as draft.
- Any document printed for review, having a watermark as “DRAFT”.
- Any printout from the stored electronic data of the instrument/ machine taken for review (applicable to printouts that are not raw data and raw data for the same is electronically available in a secured manner in the instruments/machine.
- Any photocopy of the document used for reference purposes, having a watermark/stamp’ handwritten mark as “FOR REFERENCE” or “UNCONTROLLED COPY“.
- Any document printed for reference purposes, having a watermark/ stamp handwritten mark “FOR REFERENCE” “UNCONTROLLED COPY“.
- The working documents before destruction shall be stamped/handwritten and marked as “ CANCELED” by user and dropped (whole) in the box.
6.18 Document Destruction Process
6.18.1 For disposal of documents (e.g. labels/working documents), bins with lock and key arrangements shall be kept in each section of all departments at the site. Such bins shall be labeled as “Bins for Disposal of Documents“.
6.18.2 The quality assurance department shall maintain a record of the list and location of bins kept in each section as per Annexure (List of Bin for Disposal of Documents). Each bin shall be identified with a unique number as BN/S/XXX: Where BN indicates Bin, S indicates section/area (e.g. QA QC, EN, HR, etc.) where it kept, and XXX is the sequential number starting from 001.
6.18.3 On a daily basis, the Quality Assurance person accompanied by the section in charge shall open the bin for removal of the disposed document. The section in charge shall ensure that documents are required and appropriate for destruction and shall enter the details of the documents being taken for disposal in the logbook. (Annexure, Log for Documents to be shredded).
6.18.4 The Quality Assurance person shall check the documents and on completion of the checking, these documents shall be transferred to a labeled transparent poly bag. The label shall bear the status as “Document For Destruction“, bin No., sequential reference number of lock tag, sign, and date of Quality Assurance.
Docuemnts for Destructions |
Bin No.: Lock Tag No.: Approved By QA Sign/ Date: |
6.18.5 If any objectionable document (i.e. filled checklist, signed documents, etc.) observed. Deviation shall be initiated as per SOP “Handling of Deviation” and shall be investigated as per SOP “Investigation“.
6.18.6 The bag shall be locked by above said tag having a sequential reference number for traceability purposes. Such reference shall be maintained in the logbook before sending the document.
6.18.7 Custody of numbered cable ties shall be with QA department only.
6.18.8 Locked polybag containing documents shall be sent to the paper shredding room. The paper shredding room shall be a controlled room. Such room shall have limited access (i.e. access control or lock and key facility). The paper shredding room shall not be involved in the generation and archival of GMP documents.
6.18.9 On receipt of polybag, tag and label shall be verified by the paper shredding operator. The operator shall record detail of received bag in Logbook, Log for Shredded Documents).
6.18.10 The paper shredding operator shall shred only those documents/papers that are received in the sealed bag with identified tag numbers.
6.18.11 Only one bag shall be opened at one time. The operator shall log the sequence number of lock tag in Annexure (Log for shredded documents), break the tag, and then start shredding of the documents,
6.18.12 The shred shall be collected in a transparent polybag of suitable size. The operator shall cross-mark the original label and put it in the bag. A separate polybag shall be used to collect the shred of each polybag received for document destruction.
6.18.13 The operator shall lock the above bag with another tag having a sequential reference number and mention the details of the same in a logbook, Log for Shredded Documents).
6.18.14 Shredded paper shall be further disposed of as per SOP on “Scrap Disposal“.
6.18.15 Don’t for Document Destruction Process
6.18.15.1 Tearing off paper is strictly prohibited.
6.18.15.2 Throwing paper in a dustbin is strictly prohibited.
6.18.15.3 Directly shredding any paper is strictly prohibited.
6.18.15.4 Tearing off the paper before throwing it into the bin is strictly prohibited.
6.18.15.5 Tempering of polybag and cable tie is not allowed once the bag is tied.
6.18.15.6 Partial shredding or disposing without shredding is not allowed.
6.18.15.7 Throwing of paper into area bin without a logbook entry is not allowed.
6.18.15.8 Mixing of shredded paper of two different polybags is not allowed.
6.19 Control of Scanner and Photocopy Machine
6.19.1 Access to the scanner and photocopy machine shall be restricted with password control.
6.19.2 A list of scanners and photocopy machines and authorized users shall be prepared by the respective Department Head and approved by Quality Assurance. The approved list shall be displayed near the respective scanner or photocopy machine.
6.19.3 Scanner and photocopy machine shall not be placed in the manufacturing shop, floor, and quality control department.
6.20 Handling of Digital Images:
6.20.1 During the investigation of any QMS events and as a part of any QMS document, if it requires attaching a photograph with it as objective evidence then the user department or CFT team shall capture digital images using a digital camera.
6.20.2 The following points shall be considered before capturing digital images.
- The date and time settings in the digital camera are correct. If date and time settings are not correct then it shall be corrected first before capturing photographs.
- The function of date and time shall be kept enabled while capturing digital images to record date and time in the digital image.
6.20.3 The site IT team shall create a department-wide secured folder on the system or server for storage of digital images and shall ensure that access control of that folder is limited to personnel responsible for that department for storage of digital images. The folder shall be maintained year-wise.
6.20.4 After capturing the digital images, User department or person from CFT team shall transfer required digital images from digital camera to computer system and they shall be saved in the respective secured folder which is created as per point no. 6.20.3.
6.20.5 All digital images shall be given a unique file name as below in chronological order.
- First image of year 2024 saved in folder of manufacturing department shall be given file name as 2024 MFG_0001.
- First image of year 2025 saved in folder of manufacturing department shall be given file name as 2025_MFG_0001.
- First image of year 2024 saved in folder of QC department shall be given file name 2024 QC 0001.
6.20.6 After the successful transfer of required digital images from digital camera to computer system, it can be deleted from the storage of digital camera.
6.20.7 The user department or CFT team shall issue the form as per Annexure (Form for printing of digital images).
6.20.8 Form shall be issued as per SOP “Operation of Documentum Software for Category 1 Documents” on issuance of forms through Documentum.
6.20.9 User department or CFT team shall take print of digital image on Annexure (Form for printing digital images) which is issued from Documentum or from QA.
6.20.10 All the required details shall be filled in Annexure and it shall be signed by user department or person from CFT.
6.20.11 QA shall review the print of digital images against soft copies of digital images and do his/her sign.
6.20.12 Print of all digital images shall have date and time stamp on it.
6.20.13 Print of digital images shall be attached with the respective investigation report or QMS document.
6.20.14 Soft copies of digital images saved in the respective secured folder shall not be deleted or altered.
6.20.15 Soft copies of digital images shall be kept as per the document retention time of respective document to which print of digital images attached.
6.20.16 Folders containing images should be backed up by IT as per site data backup SOP.
6.21 Handling of Duplicate multiple prints of Batch specific documents:
6.21.1 If any batch-specific document is printed in multiple/duplicate copies then all copies of the documents shall be kept with respective batch manufacturing/packing records.
6.21.2 No additional copy shall be dropped in the “Bin for disposal of documents“.
6.21.3 Multiple/duplicate printouts of batch specific documents shall be marked NA/Not applicable along the line and signature and date shall be performed.
6.21.4 Appropriate reason for multiple/duplicate prints shall be mentioned on the same.
7.0 ANNEXURE (S)
7.1 Guidance on How to Correct the Errors.
7.2 Examples of Good Documentation Practices.
7.3 Document Review Sheet.
7.4 Example for Trending of GDP Errors.
7.5 Error Ratification Form.
7.6 Log for Error Ratification Form.
7.7 List of Bins for Disposal of Documents.
7.8 Log for Documents to be Shred.
7.9 Log for Shredded Documents.
7.10 Issuance and Retrieval log of FNB.
7.11 Template of FNB
7.12 Supervisory (Scribe) Recording Activity List.
7.13 Do’s and Don’ts
7.14 Form for Printing of Digital Images.
7.15 Paper color for printing/photocopy of documents.
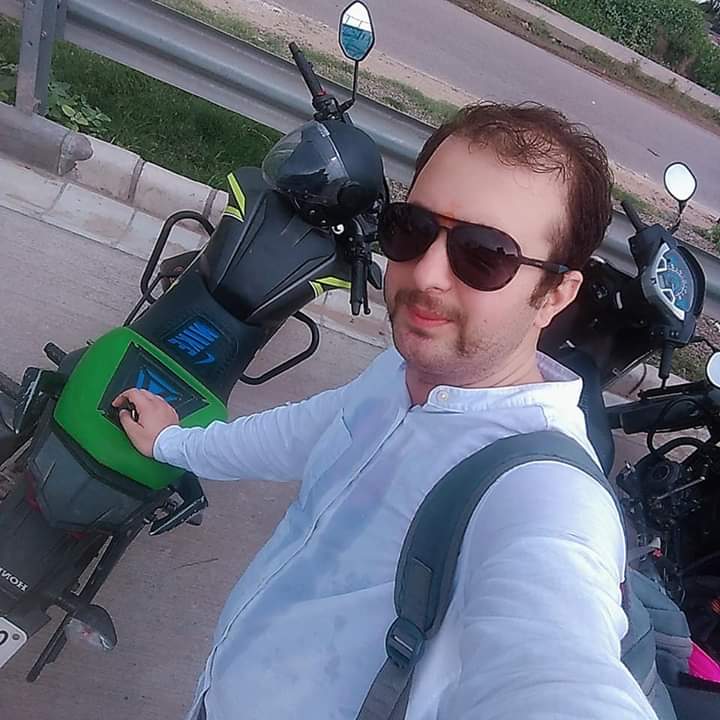
Panks Pamyal is a Author and Editor at Pharmaguddu.com. He Worked in Top Pharmaceuticals MNCs in India had a more then 10 years experience in Quality control department. He Delivering most valuable insights and knowledge through this website.