1.0 Objective: To lay down a procedure for the Operation and cleaning of Fluidized Bed Drier.
2.0 Scope: This SOP is applicable to the Operation and cleaning of a Fluidized Bed Drier in the production area.
3.0 Responsibility: Operator, Officer, Executive- Production Department
Manager- Production Department
4.0 Procedure for Operation and Cleaning of Fluidized Bed Drier:
4.1 Machine setting:
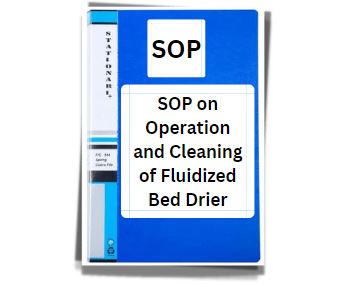
4.1.1 Ensure the ‘CLEANED’ label duly filled and signed is affixed on the equipment. Ensure cleanliness of the area and the equipment. Record the observations in the equipment usage log sheet as per SOP “Making entries in equipment usage and cleaning log sheet” Affix the ‘UNDER PROCESS’ label duly filled and signed on the equipment.
4.1.2 Open the lock of the control panel. Reading on the main air pressure gauge will start increasing. Ensure the Compressed air pressure should be between 5.5 to 6 bar.
4.1.3 Go to the menu and ‘LOGIN’ by putting in the password.
4.1.4 Go to Manual mode from the main screen.
4.1.5 Go to ‘FBG LIFT LOWR’ on MMI. The pneumatic cylinder will come down.
4.1.6 Fix the FBT supporting ring at the fringes of the finger bag and tighten the rope.
4.1.7 Fix each finger one by one on the respective hook on the finger bag hanger.
4.1.8 Clamp the finger bag hanger on the pneumatic cylinder.
4.1.9 Attach the compressed air supply pipes to the FBT supporting ring.
4.1.10 Touch ‘FBG LIFT LOWR’ on MMI. The pneumatic cylinder will start lifting up. Manually guide the guide rollers into the track.
4.1.11 Place the FBD bowl containing material to be dried in between the lower plenum and retarding chamber and lock the clamps. Insert the product bed temperature sensor in the temperature sensor port of the product container.
4.1.12 Increase the Pressure reading from HMI on the PC pressure gauge shall to 2.5 to 3 bar.
4.1.13 Increase pressure reading from HMI on the FBT pressure gauge shall to 2.5 to 3 bars.
4.1.14 Now go to the main menu
Note: Turn OFF the main compressed air while hanging the FBD finger bag or whenever the pneumatic cylinder is lifted lower.
4.2 Recipe Edit / Load / Delete
4.2.1 Recipe can be edited/loaded/deleted in both auto and manual mode.
4.2.2 Open ‘RECIPE’ from MMI to open the recipe screen.
4.2.3 Edit recipe details by changing product details.
4.2.4 Load Product Name, Batch No., Lot No., FBD Tag No., Product Code, Batch size, Manufacturing Date, Expiry Date as per respective BMR.
4.2.5 Now next edit the following details menu: ‘Process Time, Air Dry Time, Spray Time, Spray OFF Time, Spray ON Time, Shaking Interval, Shaking Duration, Piston Up, Piston Down, Cooling Time, End Shaking Time, Piston Up, Piston Down’.
4.2.6 Load Process Time, Air Dry Time, Shaking Interval, Shaking Duration, and Cooling Time, as per respective BMR.
4.2.7 Now next edit the following details menu: ‘Inlet Temperature, Outlet Temperature, Inlet High, Spray Temperature, RH Set Point, print Interval, DP across HEPA Set, DP across FBT set, Spray Pump speed’.
4.2.8 Load inlet temperature, outlet temperature, inlet high temperature, RH set point, print Interval, DP across HEPA, and DP across finger bag.
4.2.9 Touch ‘LOAD’ on MMI. The recipe load screen will open and it displays the loaded process parameter’s details.
4.2.10 Now give the recipe name and save it. The recipe will be get loaded in the PLC memory under the given name or code.
4.2.11 Touch ‘MAIN SCREEN’ on MMI. The recipe main screen will open.
4.2.11.1 To load an already existing recipe Touch ‘LOAD’ on MMI. The stored recipe list will open. Select the recipe and touch ‘ESC’ on MMI. Warning ‘LOAD RECIPE XYZ’ (XYZ indicates name or code for a particular recipe). Touch ‘YES’ to load the selected recipe.
4.2.11.2 To delete an already existing recipe touch ‘DELETE’ on MMI. The stored recipe list will open. Select the recipe and touch ‘ESC’ on MMI. Warning ‘DELETE RECIPE XYZ’ (XYZ indicates name or code for a particular recipe). Click ‘YES’ to delete the recipe.
4.3 Manual Mode Operation
4.3.1 Ensure the main switch of the control panel is at the ‘MAINTAIN’ position.
4.3.2 Touch ‘LOGIN’ and enter the password.
4.3.3 After completing of machine setting touch ‘MANUAL’ on screen. Manual mode main screen will open.
4.3.4 Start the blower from HMI
4.3.5 From HMI, open ‘BYPASS DAMPER’. The bypass Damper screen will open. The current status of the inlet air temperature, outlet air temperature, product bed temperature, air velocity, and DP across HEPA and finger bag will also be displayed on this screen. Set the bypass damper ON/OFF % depending on the inlet air, outlet air, and product bed temperature. Touch ‘BYPASS DAMPER’ ON MMI to ON / OFF the bypass damper.
4.3.6 Touch ‘PRV’ to open the previous screen.
4.3.7 At the end of the operation touch ‘BLOWER’ on MMI. A blower will stop.
4.3.8 Now go to the main menu by touching‘ MAN’ on MMI. Manual mode main screen will open.
4.4 Auto Mode Operation
4.4.1 Ensure main switch of control panel is at the ‘AUTO’ position.
4.4.2 Enter login with passwords
4.4.3 Click on the ‘AUTO’ screen will open and it displays inlet, outlet, and product bed temperature.
4.4.4 Start the process from HMI
4.4.5 Set Hot water ON and OFF time.
4.4.6 Go back from HMI to check the current process status for example ‘Air Dry Time Started’. Set and actual values for Inlet, outlet, and product bed temperature, DP across HEPA and finger bag, and air velocity will also be displayed on the screen.
4.4.7 From HMI Screen will also show the set and actual RH and % of FC damper opening, set, and actual % opening of the bypass damper.
4.4.8 Process will run as per set parameters and stops automatically on completion of a cycle.
4.4.9 Now logout the screen from HMI
4.5 Product Unloading
4.5.1 Open Manual mode main screen.
4.5.2 Decrease the Pressure reading on the PC pressure gauge shall to 0 bar.
4.5.3 Decrease the Pressure reading on the FBT pressure gauge shall to 0 bar.
4.5.4 Go to the main screen.
4.5.5 Open the screen
4.5.6 Remove the product bed temperature sensor.
4.5.7 Open the Clamps and remove the product container.
4.5.8 Touch ‘FBG LIFT LOWR’ on MMI for the Pneumatic cylinder down
4.5.9 Remove the individual finger of the finger bag from the hooks of finger bag hanger.
4.5.10 Remove the compressed air supply pipes from the FBT supporting ring.
4.5.11 Uptight the rope around FBT supporting ring and take out the finger bag.
4.5.12 Turn off the mains and the reading on the main air pressure will reduce to 0 bar and lock the control panel.
4.6 Affix the ‘TO BE CLEANED’ label duly filled and signed on the FBD and record the observations in the equipment usage log book.
5.0 Procedure for Cleaning of Fluidized Bed Drier:
5.1 TYPE A
Change over from one batch to next batch of the same product and same potency and of a similar product with ascending potency.
5.1.1 Remove the “ TO BE CLEANED “ status label and affix the new“ UNDER CLEANING “ label to the machine.
5.1.2 Enter the cleaning start time in the equipment usage log sheet as per
SOP “Filling of Equipment Usage Log Book”.
5.1.3 Shake the finger bag in manual mode to dedust.
5.1.4 Remove the remnants of the previous batch from the equipment and the area with a vacuum cleaner.
5.1.5 Allow sucking the powder attached to the wall and return the raiser using a vacuum cleaner.
5.1.6 Clean the plenum, bag chamber, inlet, and outlet air ducts from outside using a dry clean lint-free duster.
5.1.7 Clean the product container bowl with a dry lint-free cloth to remove any leftover material.
5.1.8 If the same product is processed for more than a week, then follow the procedure of cleaning during product changeover as per ‘Type B’ Cleaning.
5.1.9 Replace the” UNDER CLEANING“ status label with the “CLEANED“ status label with the date and signature of the production officer.
5.1.10 Record the cleaning completion time in the equipment usage log sheet as per
SOP “Making Entries in Equipment Usage Log Book”.
5.2. TYPE B
This is a cleaning procedure for Changing over products with different APIs/ color / descending potency or after the machine maintenance.
5.2.1 Follow the procedure from steps 5.1.1 to 5.1.4.
5.2.2 Bring down the finger bag by operating the finger bag handle towards the lower side.
5.2.3 Remove the bag from the finger-holding ring and clean the bag as per SOP “Cleaning of Filter bags“.
5.2.4 Pull out the product container bowl; dismantle the view glass (1 nos.) of the product container bowl and viewing glass (2 nos.) of the bag chamber.
5.2.5 Scrub the bag chamber, explosion chamber, and finger bag holder ring and view glasses with gasket, inflated gasket (2 nos.), and inflated tube ring with a nylon scrubber using purified water from inside and outside to remove any adhered material.
5.2.6 Use the ladder to clean the outer surface bag chamber.
5.2.7 Rinse all the above parts with 135-150 liters of purified water.
5.2.8 Scrub the product container bowl and trolley with a nylon scrubber using purified water.
5.2.9 Remove the gasket Dutch weave sieve and the supporting plate.
5.2.10 Place the sieve in a horizontal position. Scrub the sieve with a nylon scrubber using 35-40 liters of purified water.
5.2.11 Scrub the supporting plate with a nylon scrubber using purified water.
5.2.12 Rinse the product container bowl, sieve, and supporting plate with 45-50 liters of Purified water.
5.2.13 Place the sieve and the supporting plate on a clean S.S. pellet. Reassemble the sieve and the supporting plate.
5.2.14 Scrub the outside of the FBD, supporting arms inlet air duct, and the inlet chamber with a nylon scrubber using 45-50 liters of purified water.
5.2.15 Clean the outer surface of FBD; supporting arms inlet air duct and inlet air chamber with 15-20 liters of purified water.
5.2.16 Clean the utility cables limit switches and control panel with a dry lint-free duster.
5.2.17 Reassemble the view glasses of the product container of the bowl and bag chamber.
5.2.18 Fix the duly cleaned finger bag on the finger bag holder ring and position the finger bag.
5.2.19 Assemble the FBD and operate the FBD at an inlet temperature of 70-80°C for 30 to 40 minutes to dry the sieve and finger bag. Remove the finger bag and transfer it to the granulation spare area.
5.2.20 Rinse the bag chamber, and explosion chamber, and view glasses with 45-50 liters of purified water.
5.2.21 Wipe out the body of FBD, bag chamber, explosion chamber, trolley, and bowl with a clean dry lint-free duster.
5.2.22 Wipe all the above parts with 70% w/w IPA solution.
5.2.23 Affix the status label on FBD “CLEANED” with the date and signature of the production officer.
5.2.24 If FBD is idle for more than 72 hours, then wipe with a lint-free duster dipped in 70% w/w IPA before use.
5.2.25 Replace the previous ‘CLEANED’ status label with the current date ‘CLEANED’ status label with the date and signature of the production officer.
5.2.26 Record the cleaning completion time in the equipment usage log sheet.
5.2.27 Record the cleaning checklist as per Annexure –I for Operation and Cleaning of Fluidized Bed Drier.
5.3 Frequency
5.3.1 Type ‘A’ cleaning is applicable after the completion of every batch of the same product
5.3.2 Type ‘B’ cleaning is applicable in case of product changeover or the same product is run for a week whichever is earlier
6.0 Abbreviations:
FBD: Fluidized Bed Drier.
IPA: Iso Propyl Alcohol
Q.A.: Quality Assurance
S.S.: Stainless Steel.
SOP: Standard Operating Procedure
BMR: Batch Manufacturing Record
MMI: Man-Machine Interface
HEPA: High-efficiency particulate air
PC: Product Container
DP: Differential Pressure
w/w: Weight/weight.
Annexure-I for Operation and Cleaning of Fluidized Bed Drier
Activity | Activity performed | Checked by |
Shake the finger bag manually mode to dedust. | ||
Remove the ruminants of the previous batch from the equipment and the area with a vacuum cleaner. | ||
Allow suck the powder attached to the wall and return the raiser using a vacuum cleaner. | ||
Bring down the finger bag by operating the finger bag handle towards the lower side. | ||
Remove the bag from the finger-holding ring and clean the bag. | ||
Pull out the product container bowl; dismantle the view glass (1 nos.) of the product container bowl and the viewing glass (2 nos.) of the bag chamber. | ||
Scrub the bag chamber, explosion chamber, and finger bag holder ring and view glasses with gasket, inflated gasket (2 nos.), and inflated tube ring with a nylon scrubber using purified water from inside and outside to remove any adhered material. | ||
Use the ladder to clean the outer surface bag chamber. | ||
Rinse all the above parts with 135-150 liters of purified water. | ||
Scrub the product container bowl and trolley with a nylon scrubber using purified water. | ||
Unclamp the bowl from the trolley and lift the product container. | ||
Remove the gasket Dutch weave sieve and the supporting plate. | ||
Place the sieve in a horizontal position. Scrub the sieve with a nylon scrubber using 35-40 liters of purified water. | ||
Scrub the supporting plate with a nylon scrubber using purified water. | ||
Rinse the product container bowl, sieve, and supporting plate with 45-50 liters of Purified water. | ||
Place the sieve and the supporting plate on a clean S.S. pellet. |
Reassemble the sieve and the supporting plate. | Activity performed | Checked by |
Scrub the outside of the FBD, supporting arms inlet air duct, and the inlet chamber with a nylon scrubber using 45-50 liters of purified water. | ||
Clean the outer surface of FBD; supporting arms inlet air duct and inlet air chamber with 15-20 liters of purified water. | ||
Clean the utility cables, limit switches, and control panel with a dry lint-free duster. | ||
Reassemble the view glasses of the product container of the bowl and bag chamber. | ||
Fix the duly cleaned finger bag on the finger bag holder ring and position the finger bag. | ||
Assemble the FBD and operate the FBD at an inlet temperature of 70-80°C for 30 to 40 minutes to dry the sieve and finger bag. | ||
Remove the finger bag and transfer it to the granulation spare area. | ||
Rinse the bag chamber, and explosion chamber, and view glasses with 45-50 liters of purified water. | ||
Wipe out the body of FBD, bag chamber, explosion chamber, trolley, and bowl with a clean dry lint-free duster. | ||
Wipe all the above parts with 70% w/w IPA solution. |

Naresh Bhakar is the Founder and Author at Pharmaguddu.com, bringing his extensive expertise in the field of pharmaceuticals to readers worldwide. He has experience in Pharma manufacturing and has worked with top Pharmaceuticals. He has rich knowledge and provides valuable insights and data through his articles and content on Pharmaguddu.com. For further inquiries or collaborations, please don’t hesitate to reach out via email at [email protected].