Tablet excipients generally have no medicinal properties, although excipients are used to fill the drug’s bulk mass. Excipients also facilitate sustaining the drugs for a long time and help increase bioavailability in systemic absorption. Excipients might help in disintegration, lubrication, masking the test, and tablet hardness. The different types of Tablet excipients are explained below with their properties.
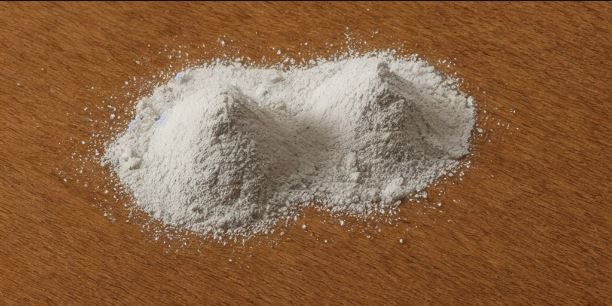
Pharmaceuticals Tablet excipients and their importance:
Diluent/ Fillers:
They are used to Produce tablets of reasonable size, i.e., a minimum diameter of 3mm, potent drug <60mg
A) Lactose is a disaccharide and alpha-Lactose monohydrate (wet granulation), which is used widely. Hydrous lactose causes the Maillard reaction. interaction of amine drugs with hydrous lactose in the presence of lubricant like magnesium stearate resulting in yellowish decoloration from time to time
Spray-dried lactose (3% moisture): is used for direct compression. However, it is prone to darkening in the presence of excess moisture, amines, and furaldehyde.
Hydrous lactose –Wet granulations
Anhydrous lactose- No Millard’s reaction/direct compression
B) Starch: It may give rise to soft tablets. Moisture content 11-14%. Sta- Rx — 1500 free-flowing & directly compressible. It is a diluent, binder, disintegrating agent, self-lubricating, and glidant (0.25%). Emdex & celutab (contains 90-92% dextrose, 3-5% maltose) are hydrolyzed starches & are free-flowing and directly compressible. They are sweet and can be used to replace Mannitol.
C) Dextrose: It is sometimes used to replace the spray-dried lactose to reduce the tablet to darken.
D) Mannitol: Mannitol has Negative heat of salvation properties, slow solubility & pleasant feeling in the mouth, used mainly in chewable tablets. It is non-hygroscopic, so it can be used in vitamin formulation, which is moisture sensitive.
Mannitol: has poor flow, so requires high amounts of lubricants.
E) Sorbitol is an optical isomer of Mannitol, but sorbitol is hygroscopic above 65% humilities.
F) Sugar based diluents: Sugar tab- 90-92% sucrose+ 7-10% invert sugar
Dipac- 97% Sucrose + 3% dextrin
Nutab – 95% sucrose + 4% invert sugar with a small quantity of corn starch & magnesium stearate.
G) Microcrystalline Cellulose (Avicel) Direct compressible: Avicel -101 Powder
Avicel 102 – Granules produce cohesive compacts, disintegrating agent
H) Calcium Slats: DCP (Dibasic calcium phosphate) and calcium sulfate have a low concentration of unbound
moisture. The bound water of calcium sulfate is not released up to 80 °C. DCP is virtually insoluble in water and is hence used in conjunction with a disintegrating agent. Calcium-based diluents can cause interaction with tetracyclines API.
Binder and Adhesives excipients for tablets:
- Acacia & Tragacanth-10-25%
- Starch- 5-10%
- Gelatin- 5-20%
- Glucose- 50%
- Sucrose- 70%
A) Acacia & Tragacanth: it is a Natural origin, so variable in composition and easily attacked by microorganisms.
B) Starch paste: Prepared by dispersing starch into the water when heated. The paste must be translucent rather than transparent. On heating, starch hydrolyzed to dextrin & glucose. In contrast, transparent paste indicates complete conversion to glucose.
C) Methylcellulose, Hydroxypropyl methylcellulose (HPMC), and Hydroxypropyl cellulose (HPC) [for both alcoholic & aqueous solutions], are common binders for direct compression & their aqueous solution are adhesive. Polyvinyl pyrrolidone (PVP) is adhesive in either aqueous or alcoholic solutions. Its concentration used is 0.5- 3%.
D) Ethylcellulose: is used only with the alcoholic solution. Ethylcellulose retard the disintegration & dissolution of drugs.
Disintegrates as a tablet excipient:
Disintegrates help in the penetration of water and swell up.
Mechanism of Disintegrants: Those that enhance the action of capillary forces in producing rapid intake of aqueous liquids. So disintegrants have porous structures and show low interfacial tension towards aqueous fluids—rapid penetration by water in the tablet matrix resulting in the breakup of the tablet. E.g., Starch, MCC, Cationic resins, and sodium starch which swell in contact with water. E.g. Acacia, Tragacanth. One problem can be they produce glycolate sticky/gelatinous mass that resists the break up of tablets, so optimize concentration within granulation.
Gas Production: They are sensitive to small changes in humidity levels.
A) Starch: Most commonly used (5-20%). Modified starch primogel and explotab are low-substituted carboxymethyl starches (1-8%).
B) Clays & bentonite: commonly used 10% but can give off a white appearance.
C) AC-Di Sol: Internally cross-linked sodium carboxymethyl cellulose, i.e., Na CMC.
D) Cross-linked polyvinyl pyrrolidone: These two are called super disintegrants. E.g., sodium starch glycolate, croscarmellose (cross-linked CMC), crospovidone, palacrillin K+. It is a cation exchange resin.
E) Sodium glycine carbonate: Source of CO2 for effervescent tablets.
Disintegrates used in effervescent tablets: The most common is a mixture of citric acid & tartaric acid plus carbonates/bicarbonates, and Sodium glycine carbonate.
You may Like: 3 Types of Tablets Manufacturing Processes
Lubricants, Antiadherants & Glidants:
A) Lubricants: They are intended to reduce the friction during tablet ejection between the tablet walls and the die cavity walls in which the tablet was formed—E.g. Magnesium stearate but not glidant.
B) Antiadherents: They are used to reduce the sticking & adhesion of any tablet granulation/powder to the punches of the die wall.
C) Glidants: helps in promoting the flow of tablet granules from the hopper and reduce friction between the Particles Eg. colloidal silicon dioxide (No lubricant activity, Aerosil, cab-O-Sil, Soluble), calcium, and magnesium Stearates 0.25 to 1%.
D) TALC: (5%) Both glidant + lubricant activity (Contains Iron, so Carefully used if any formula contains drugs whose breakdown is catalyzed by Fe²+ )
Others: PEG, Colloidal silicas 0.25 -5%, Starch, Liquid Paraffin 5%.
Lubricants based upon fatty acids are insoluble in water & hence can retard the disintegration & dissolution time. Water-soluble lubricants: PEG 6000, [Macrogol 6000 or carbowax], Magnesium Lauryl Sulfate, Fumaric acid.
E) Microcrystalline cellulose/Avicel: Low coefficient of friction when compressed MCC particles deform physically and surfaces form H-bonding. MCC is hygroscopic & water causes the weakening of inter particulate hydrogen bonds.
F) Glidants: They get absorbed or interpose their particles between those of other components, which reduces adhesive tendencies or lowers the interarticular friction system. So they are also called flow promoters: Eg, Colloidal SiO2 Starch, and talc.
G) Calcium stearate: (Lubricant) can cause Maillard’s reaction with amine drugs like aminophylline with lactose.
During tablet granulation adding both disintegrant & lubricant at a time, results in the disintegrant being coated with lubricant & often results in decreases in disintegrants porosity and a decrease in efficiency of disintegrants.
Colors, Flavors & Sweeteners:
A) Lakes: They are dyes that have been absorbed on hydrous (Al(OH)3) oxide and are usually employed as dry powders for coloring. They contain 10-30 % of pure dye & a maximum of up to 50%.
Lakes: During the wet granulation, care must be taken to prevent color migration during drying (mottling) [mainly with soluble dyes 1. Colorant should not be more than 2%. Flavor oil maximum up to 0.5-0.75%.
B) Mannitol is 72% solvent as sucrose.
C) Saccharin is 500 times sweeter than sucrose, but it is carcinogenic.
D) Aspartame is a (Dipeptide aspartic acid + Phenylalanine) replaced by saccharin, but aspartame lacks stability in the presence of moisture because of its hygroscopic nature.
Wetting agents:
Wetting agents are tablet excipients used to increase water uptake, enhance disintegration, and assist dissolutions. E.g., Sodium Lauryl Sulfate (LSL) or Docusate sodium is known to enhance the dissolution as it is an anionic surfactant that destroys the membrane of the intestines. These wetting agents are added when the drug is hydrophobic.
Conclusion:
In conclusion, tablet excipients play a crucial role in ensuring quality and safety in pharmaceutical manufacturing. They serve various functions such as improving drug stability, enhancing drug absorption, and masking unpleasant tastes or odors. However, the use of tablet excipients also presents some challenges and risks during the manufacturing process, which must be carefully handled with allowable quantity. To ensure high quality it must be used as per the R&D, validation criteria.

Naresh Bhakar is the Founder and Author at Pharmaguddu.com, bringing his extensive expertise in the field of pharmaceuticals to readers worldwide. He has experience in Pharma manufacturing and has worked with top Pharmaceuticals. He has rich knowledge and provides valuable insights and data through his articles and content on Pharmaguddu.com. For further inquiries or collaborations, please don’t hesitate to reach out via email at [email protected].