1.0 Purpose: The purpose of this SOP is to lay down the procedure for effective training of personnel working at a manufacturing site. In order to ensure that all employee receives appropriate training which would enhance their knowledge, experience, skill, ability, and behavior to execute their appropriate duties and responsibilities in such a manner, to provide Assurance that the drug product has the safety, identify, strength, quality, and purity that it purports.
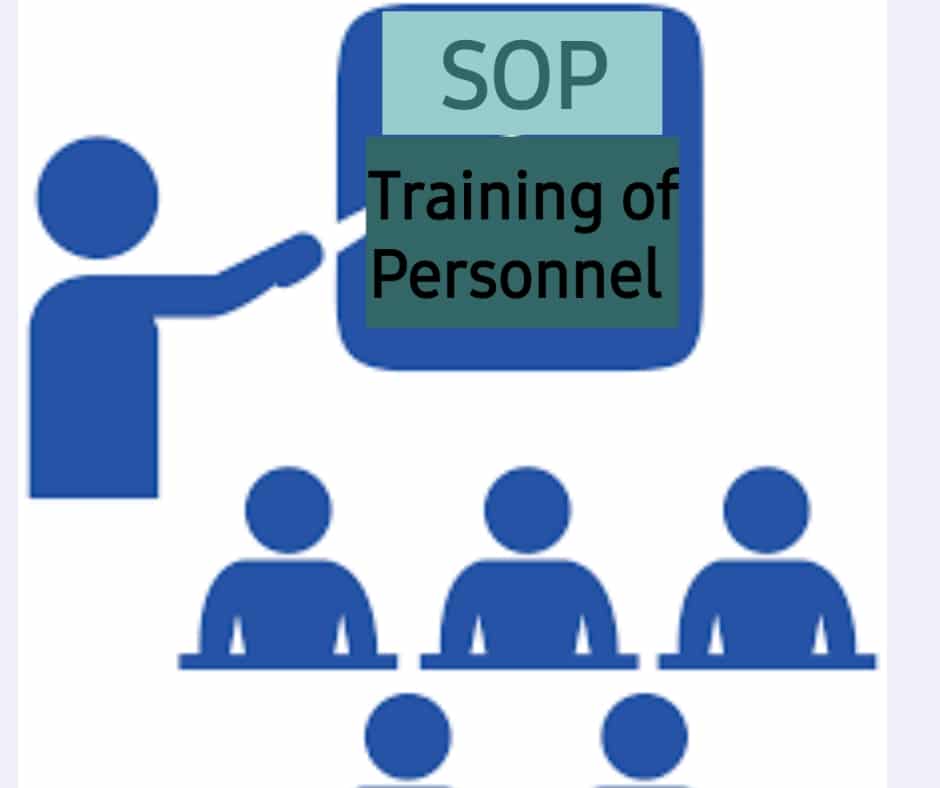
2.0 Scope: This procedure is applicable to all the employees of the company involved in manufacturing, processing, packing, and testing for holding of the drug products for commercial distribution for stability or as an exhibit batch for submission with a regulatory filling. This SOP (Training of personnel) is also applied to all maintenance, other Support Service personnel, and management associates assigned to a cGMP facility for working on the cGMP system at the plant.
3.0 Responsibility: 3.1 The P&A Head shall be responsible for providing induction training to all recruits.
3.2 Concerned department head/Designee/approved trainer Shall impart training on the relevant activity of the department.
3.3 The concerned department head shall be responsible for the identification of the training date of the individual depending on the activity he or she will perform.
3.4 The concerned department head shall be responsible for ensuring that all personnel working in the respective department are trained and how the expertise to work in their own function.
3.5 Quality Assurance head designee shall be responsible for imparting training related to cGMP.
3.6 The QA head and plant Head shall be responsible for the selection of external facilities to import training when the need arises.
3.7 The site QA head shall be responsible for certifying the qualified trainer.
3.8 Each employee shall receive training in the particular operation that he or she performs.
3.9 Training in current good manufacturing practices and good distribution practices shall be conducted by the QA head/designee on a continuing basis (at least once a year) to ensure that employees remain familiar with the current requirements applicable to them.
3.10 A person involved in the activity of manufacturing and quality areas must be educated and well-trained to ensure the quality and safety of products.
3.11 Effective training programs shall be essential to ensure that the employee has the knowledge and skills they need to perform their jobs.
Read Also: SOP on Cleaning and Sanitizing Solution Preparation
4.0 Definition Related to Training of Personnel:
Training: Training is a continuous instructional process that enhances the employee with competency in knowledge experience behavior and necessary skills to perform assigned Job responsibilities so as to achieve the required organization goal.
Training calendar: The training calendar is a document prepared by every department listing the SOP/cGMP/quality system and other training that shall be given in the entire year to the individual department as per their training needs and identification. Based on the on-job for refresher training, the document is to be prepared by the officer/executive of the concerned department, checked by the Head of the concerned department, and approved by the Head of QA.
The master copy of the training calendar of All the departments shall be submitted to QA, and a control copy of the same shall be issued to the respective department.
Approved trainer: the approved trainer is an employee from any of the departments who has adequate knowledge of the subject, qualification, experience, and training skill and is designated for development and conducting training related to function and operation.
Trainee: the trainee is an employee from any of the departments who undergoes training for a particular job function.
Evaluator: The evaluator is an employee from the concerned department who checks the questionnaires. The trainer himself may also be the evaluator.
GMP Training: the continual and product training of personnel to maintain their level of the GMP regulation and current topics that are affecting the manufacturing, processing, packing, testing, holding, and distribution of drug products.
Good distribution practice: Good distribution practice (GDP) is the part of quality assurance that ensures that the quality of medicinal products is maintained throughout all stages of the supply chain from the site of the manufacturer to the supply of medicinal products to the public.
Training aids: Training aids are any material, item, document, procedure, and presentation used for imparting training and evaluating training effectiveness.
SOP Training: the training of personnel on written procedure either new, revised, or updated procedure as per its applicability to the specific individuals working in the department.
Training matrix: it is a guidance document that lists all the SOPs/topics on which training is required for the individual of a particular department. The document shall display for every department topics which shall be covered under training and those which are irrelevant through inappropriate legend. The document shall be prepared as a stand-alone document and shall be identified through the inappropriate number, which includes the revision number. The document shall be revised or annexed wherever a new requirement is introduced to the department or when job responsibilities have been changed.
External training: All training is presented by external faculties, who are experts in their own field, including attending a seminar, consultants, training, conferences, and professional organization meetings.
Training assessment record: The written evaluation of training, understanding of the training which will be related to their job responsibilities, a master copy of his training assessment record shall be submitted to the QA Head, and a control copy of the same shall be issued to respective departments on request.
Read Also: Entry and Exit Procedure for staff, visitors in Pharmaceuticals
5.0 Procedure for the Training of Personnel:
5.1 Every employee involved in Pharma whose activities may directly or indirectly affect the quality of products manufactured must be given sufficient and appropriate training to enable them to perform their assigned jobs. flowchart of the training process is given as an annexure “training process flowchart.”
5.2 Trainer approval:
5.2.1 The training program shall be conducted by an approved trainer
5.2.2 The Department Head shall be considered as an approved trainer by virtue of their designation and experience.
5.2.3 An employee can be the approved trainer when he or she fulfills the following requirements.
- He/ She Completed the induction schedule, including the cGMP/GLP training.
- Shall be certified as trained as per job description.
- Trained on the site training procedure “guideline for carrying out training program.”
- Attended and successfully completed the “train and trainer” course, including the delivery of the training session on any selected topic.
5.2.4 The trainer has to be a good orator and has to be well-versed in the subject.
5.2.5 On meeting the above requirements, the employee self is certified as a qualified trainer as per annexure “trainer qualification certificate.”
5.2.6 All the departments are responsible for informing the training coordinator in QA to include the name of the newly approved trainer in his or has department in the list of qualified trainers.
5.2.7 Review and update the list of approved trainers on an annual basis to ensure that the qualified trainer has undergone training on cGMP at least once a year.
5.2.8 In case of any addition or deletion in the list of trainers, update the detail in the annexure “list of qualified trainers” and attach it as a supplement to an annexure “list of qualified.”
5.3 External training:
5.3.1 For the training of personnel, training can also be conducted by a certified consultant or external trainer.
5.3.2 The external trainers should fulfill the following requirements.
5.3.3 The consultant should have sufficient education training for the experience to advise on the subject
5.3.4 The consultant or external trainer shall be a diploma holder and a graduate in Science/pharmacy/ engineering to perform laboratory training /technical training.
5.3.5 The consultant or external trainer should possess sufficient experience in the subject matter/ service provided, e.g., qualification, operation troubleshooting, etc.
5.3.6 The consultant /external trainer should possess a certificate from the agency he or she belongs to stating he or she is authorized to train personnel.
5.3.7 The information for the external trainer shall be recorded on annexure “consultant/external trainer record,” which shall be evaluated by the quality assurance head and maintained by the concerned department.
5.4 Self-training and certification:
5.4.1 A qualified trainer shall be trained on the standard operating procedures and various systems by self-reading the respective standard operating procedures and training models.
5.4.2 the same shall be documented in the annexure “self-training and training record” and shall be self-certified by the qualified trainer.
5.4.3 self-reading of the standard operating procedure shall be carried out followed by answering the training assessment record as per annexure “training assessment record” Any difficulty in understanding shall be clarified by approaching the subject expert before solving that training assessment record.
Read Also: SOP on handling scrap and disposal in pharmaceutical
5.5 Training for new recruits:
5.5.1 For new recruits, a training program “basic induction training module for new entrants” shall be conducted by quality assurance during the induction schedule as per SOP number “procedure for induction for the new entrants to plant”
5.5.2 Quality Assurance share covers all the basic requirements related to the Pharmaceutical quality system cGMP, Data integrity, GDP safety, and health hygiene, etc.
5.5.3 The induction program shall cover a brief overview of the organization and department-wise teams, systems, and functions.
5.5.4 After the completion of induction training, the new employee shall be sent to his or her department as per the SOP number.
5.5.5 The Head of the department shall brief the expectation and prepare the job responsibility as per SOP for the new joiner. After completion of induction training the same shall be effective after completion of on-job training.
5.5.6 Identify the training needs of the person to perform the assigned Job responsibility as per annexure “list of topics to be covered for the training of personnel” in the annexure “job-specific training need identification form.”
5.5.7 All the departments should prepare a training matrix on an annual basis and update the same on a monthly basis as per the annexure “departmental training Matrix,” which includes a list of SOPs and training modules (if any). The quality Assurance head should approve the training matrix.
5.5.8 Departmental training metric will be numbered as DD/TM/YY/VV
5.5.9 Where, DD-Department code (eg. QA for Quality assurance, QC for Quality control, MI for microbiology, TB for tablet manufacturing, TP for Tablet packing, WH for warehouse, EG for engineering, IT for information technology, and PA for personnel and administration)
TM- Training matrix
YY- Last two letters for the current year(e.g., 24 for the year 2024).
VV- Version number of the training matrix.
5.5.10 In the case of new recruitment for the induction of new SOPs, the training Matrix shall be appended with the training requirements, and the same is to be attached to the parent list. Amendment to the training metric to be numbered as ADD/XX/DD/TM/YY/VV. wherein ADD stands for Addendum and XX stands for the serial number of the Addendum.
5.5.11 In case the employee is shifted from one role to another from one department to another department, the job responsibility is to be updated, and the additional training required is to be identified as per the annexure “list of topics to be covered for the training of personnel” and “job-specific training need identification form” respectively
5.5.12 As per the identification of training needs, the training will be imparted to each individual.
Read Also: SOP for Footwear Cleaning in Pharmaceutical
5.6 Training evaluation:
5.6.1 Carry out the training evaluation Of each training session to determine the effectiveness of the training programs and understanding of the subject covered in the training program. The document is an assessment in the “training assessment record” as per the annexure.
5.6.2 All the training (on-the-job training and classroom training) shall be evaluated through a written assessment only.
5.6.3 in exceptional cases where oral feedback for group discussion can be done on pre-defined parameters prepared as per annexure “oral feedback /group discussion questionnaire,” which are to be assessed by the evaluator after the oral feedback or group discussion.
5.6.4 in case of written assessment, grade the individual based on a percentage as follows: (100% “satisfactory”) and ( 80% 99% “discussion required”)
5.6.5 The trainer should personally call the trainee and discuss a topic in brief with the trainee. So to find out if the trainee has understood the topic properly. In such a case, oral feedback is satisfactory. The same shall be entered in the evaluation sheet.
5.6.6 Below (80% “not satisfactory”) trainees should be trained within a week.
5.6.7 in case the trainer has to discuss the topic with the trainee due to performance in the assessment is 80% to 99%, the same shall be done within one day from the evaluation of the training.
5.6.8 An evaluator can carry out re-evolution on the basis of the training assessment record answer sheet.
5.6.9 That attendance is to be documented as per annexure “training attendance sheet.”
5.6.10 After completion of each training, the individual training index is to be updated in the “job-specific training index.”
5.6.11 During the training period, the person shall be trained in all topics related to the department and more specifically to the duties to be assigned to the individual.
5.6.12 The trainee should work along with trained personnel, and training relevant to the task has been satisfactorily completed, assessed, and documented.
5.6.13 After valuation, the job responsibility Shall be effective and approved by the Department Head as per SOPs “stabilizing job responsibility.”
5.7 Certification:
5.7.1 After completion of initial training, the experienced person shall be issued a “training certificate for experienced personnel” as per annexure, and a new recruit shall be issued a training certificate for new recruit as per annexure, and then the new recruit/experience person shall be permitted to work in his/ her designated area.
5.7.2 Original copy of the Training Certificate to be filled in the respective training file and one copy to be given to the respective department head.
5.8 Ongoing training:
5.8.1 Prepare a training calendar on an annual basis identifying the training plant in each month as per the “training calendar.”
5.8.2 Conduct training programs individually or in a group so as to include the person working in the department.
5.8.3 Ensure that each person receives training on various subjects, which include training on cGMP, GDP (Good Distribution Practice), and Data integrity governance at least once annually. This annual training shall be evaluated through a “written assessment record” or “oral feedback /group discussion questionnaire” whenever applicable as per the annexure.
5.8.4 In case any person is absent for training sessions, then conduct the training for the absentees within four weeks after he/she resumes duty. Annual training shall be Reconciled as per annexure “annual training employee reconciliation format,” and separate training sessions shall be organized irrespective of the planner to train all the employees in-plant if required.
5.8.5 Training shall be completed as per the “training Matrix,” indicating departmental and cross-departmental standard operating procedures. The date of actual completion shall be recorded in the space provided in the matrix on completion of training.
6.0 Type of personnel training
6.1 Classroom training:
6.1.1 Classroom training shall be imparted as per the pre-defined training need identification schedule for SOPs, cGMP, system, health, safety, behavioral activities, and other types of training.
6.2 On-the-job training:
6.2.1 on job training such as SOPs training and operational training shall be identified based on the activities/functions to be handled by the personnel.
6.2.2 Training shall be imparted by explaining the basic requirements/Precautionary measures to be followed during the activity.
6.2.3 on-job training in the presence of trained personnel shall view the operations/activities for which he will be responsible during his routine activity.
6.3 Retraining for the training of personnel:
6.3.1 Conduct retraining within a week’s time in case of individual performance and satisfaction.
6.3.2 in case of any laboratory error or deviation identified for any individual, retraining should be imported to all the laboratory/ department personnel.
6.3.3 All employees shall be given refresher training on a particular subject at least once every two years if no change in the SOP for the procedure has occurred in that time span.
6.3.4 in case there is a change in SOP or procedure, refresher training shall be imparted irrespective of the calendar matrix.
7.0 Documentation for the training of personnel:
7.1 Maintain the record of each training session and its evaluation conducted for each training in the individual training file. Maintain the record of the training attendance sheet in the general training file.
7.2 The general training file consists of a training attendance sheet.
7.3 The individual training file concept of induction schedule job-specific training needs identification form (for new recruit),job-specific training index, training assessment sheet, training record, Training Certificate, and trainer qualification certificate as applicable.
7.4 Maintain the training Matrix in the respective department and the older version is to be submitted to the Quality Assurance department for archival on an annual basis.
8.0 Visitors or Un-trained personnel:
8.1 As far as possible, avoid taking a visitor or untrained personnel into the production and quality control area. In case it is unavoidable brief them in advance about personal hygiene, gowning system, entry/ exit procedure, and safety requirements.
8.2 A site-trained person shall always accompany this person.
9.0 Abbreviations:
- Dept – Department
- QA – Quality assurance
- QC – Quality Control
- % – Percent
- SOP – Standard operating procedure
- cGMP – Current good manufacturing practice
- P&A – Personnel and Administration

Naresh Bhakar is the Founder and Author at Pharmaguddu.com, bringing his extensive expertise in the field of pharmaceuticals to readers worldwide. He has experience in Pharma manufacturing and has worked with top Pharmaceuticals. He has rich knowledge and provides valuable insights and data through his articles and content on Pharmaguddu.com. For further inquiries or collaborations, please don’t hesitate to reach out via email at [email protected].
great job sir , thanks for good information , I hope you provide protocols ,annexures , attachments , to support these documents , thanks again .