Standard operating procedure for Microbiological Testing of In-Process Packing Material, SOP for Bioburden Test.
I.0 Purpose: This SOP outlines the steps for conducting Microbiological Testing of In-Process Packing Material.
2.0 Scope: This SOP is applicable for the Microbiological Testing of In-Process Packing Material.
3.0 Responsibilities: All Quality Control personnel are responsible for adhering to and implementing this SOP.
4.0 Procedure:
4.1 Introduction:
In our sterile block, we use different types of primary and secondary packing materials, such as rubber bungs, glass vials, and aluminum seals. For packing purposes, rubber bungs and glass vials are terminally sterilized, and aluminum seals are sanitized using 70% filtered IPA.
To ensure sterility during the filling process, these materials need to be checked for bioburden.
4.2 Sampling Kit Requirement and Transfer:
- For the analysis of Depyrogenated Glass Vials and Sterilized Rubber Bungs, the required media are Soybean Casein Digest Medium (SCDM) and Fluid Thioglycollate Medium (FTGM).
- For the analysis of Sanitized Aluminum Seals, the required media are Buffered Peptone Sodium Medium and Dey Engley Neutralizing Agar Medium.
- These media should comply with Sterility and Growth Promotion Tests, which are conducted before or in parallel with the actual analysis.
Keep ready the necessary materials for sampling purposes:
- Soybean Casein Digest Medium (SCDM) and Fluid Thioglycollate Medium (FTGM) tubes.
- A sterile empty bottle was designated for the sampling of aluminum seals.
- An SS Sampling Kit (SS Drum) for organizing the sampling kit.
- Transfer the prepared Sampling Kit into the washing area of the sterile block.
- Follow the designated entry Procedure for this transfer.
- Sanitize the sampling kit using a 70% Filtered Isopropyl Alcohol (IPA) solution. After sanitization, keep the kit in the Dynamic Pass Box located in the Washing Room.
- Following the appropriate entry procedure, proceed to enter the Filling Area of the Cephalosporin section.
- Retrieve the sanitized sampling kit from the Dynamic Pass Box and proceed to perform the sampling process.
4.3 Examination of Rubber Bung and Glass Vial:
- To ensure accurate results, follow these steps: when sampling and analyzing rubber bungs and glass vials using the direct inoculation method.
- Maintain aseptic behavior and prevent external contamination during the sampling process.
- A sampling of depyrogenated glass vials and sterilized rubber bungs must be conducted within a Laminar Air Flow (LAF) of the Filling Machine.
4.4 Sampling of Depyrogenated Glass Vials:
- For each type of media, Soybean Casein Digest Medium (SCDM) and Fluid Thioglycollate Medium (FTGM), take approximately 2 to 4 depyrogenated glass vials.
- Use the direct inoculation method for sampling.
- Transfer the glass vials to their respective media tubes.
4.5 Sampling of Sterilized Rubber Bungs:
- Similar to the glass vials, take around 10 sterilized rubber bungs for each type of media, SCDM and FTGM.
- Employ the direct inoculation method for sampling.
- Place the rubber bungs in their corresponding media tubes.
4.6 Post-Sampling Steps:
- After sampling, store all the sampled tubes in a sampling kit designed for this purpose.
- Transfer the sampling kit to the Microbiology department for further incubation.
4.7 Incubation Conditions:
- Incubate the tubes containing Soybean Casein Digest Medium (SCDM) at 20 to 25ºC for a duration of 14 days.
- Incubate the tubes with Fluid Thioglycollate Medium (FTGM) at 30 to 35ºC for the same 14-day period.
- Log the samples in the Inward Register of Sterility Testing to maintain proper documentation.
- Observe each tube daily and record the results accurately.
4.8 Control Measures:
- Maintain Negative Controls:
- Incubate tubes with negative controls of Soybean Casein Digest Medium (SCDM) and Fluid Thioglycollate Medium (FTGM) at 20 to 25ºC and 30 to 35ºC respectively for 14 days.
4.9 Positive Control Using Fluid Thioglycollate Medium:
- Inoculate the same lot of Fluid Thioglycollate Medium with 10-100 cfu/ml viable microorganisms of Clostridium sporogenus (ATCC 11437).
- Incubate positive control tubes at 20°C to 25°C for a maximum of 3 days for bacteria, and not more than 5 days for fungi.
4.10 Positive Control Using Soybean Casein Digest Medium:
- Inoculate the same lot of Soybean Casein Digest Medium with 10-100 cfu/ml viable microorganisms of Bacillus subtilis (ATCC 6633).
- Incubate positive control tubes at 20°C to 25°C for bacteria and not more than 3 days, and at 30°C to 35°C for fungi, not exceeding 5 days.
4.11 Examination of Sanitized Aluminum Seals:
- Aluminum seal analysis is conducted using the Membrane Filtration method.
- The required items include an empty sterilized bottle, Buffered Peptone Water, and Dey Engley Neutralizing Agar.
5.0 Sampling:
- Sanitized aluminum seal sampling is performed within the Laminar Air Flow (LAF) of the Sealing Machine.
- Approximately 10 sanitized aluminum seals are randomly selected and placed in an empty sterilized bottle.
- The bottle with samples is then transferred to the Microbiology department for further analysis.
- Analysis Entry: The analysis is recorded in the Inward Register of Packing Material, referring to Annexure I.
6.0 Analysis Process:
- The analysis continues under the LAF of the Microbiological Testing (MLT) Room.
- Approximately 100ml of Sterile Buffered Peptone Water solution is transferred to a sample bottle containing the aluminum seals.
- The bottle is vigorously shaken for 1 minute to mix the solution.
- The solution is then filtered through a sterilized filtration assembly using a 0.45 µ membrane filter paper with a size of 47mm.
- After filtration, the membrane filter is carefully lifted with sterilized forceps and placed on the surface of the Dey Engley Neutralizing Agar (DENA) Plate, avoiding air bubbles.
- The plate is incubated in an inverted position.
- A dual-temperature incubation condition is followed for the incubation of plates.
- First, the DENA plates are incubated at 20-25°C for 72 hours for the determination of Total Fungal Count (TFC).
- Then, the same plates are incubated at 30-35°C for 48 hours for the determination of Total Bacterial Count (TBC).
- After 5 days, the number of colony-forming units (CFUs) observed on the plate is counted by using the Colony Counter.
- The Total Viable Aerobic Count (TVAC) is calculated by adding TBC and TFC counts. The count is expressed as CFU.
- The results are recorded in Annexure II.
6.1 Control Measures:
- For positive control, refer to the media fertility test conducted during media preparation.
- Keep one plate of the same media lot used for testing as a negative control.
- Incubate the negative control plate at the respective temperatures along with the test plates.
6.2 The limits and frequency:
Activity | Maximum Limit | Frequency |
Total Bacterial Count | 02 CFU/plate | During Filling Activity of Each batch |
Total Fungal Count | 02 cfu/plate | During the Filling Activity of Each batch |
Note:
- If the microbial count exceeds the limit, the Microbiologist informs the Head of Quality Control and Quality Assurance.
- An Out of Specification investigation is initiated as per the specified SOP.
7.0 Annexures:
Annexure I: Inward Register of Bioburden Analysis of Primary Packing Material
Annexure II: Bioburden Report of In-Process Sample of Primary Packing Material
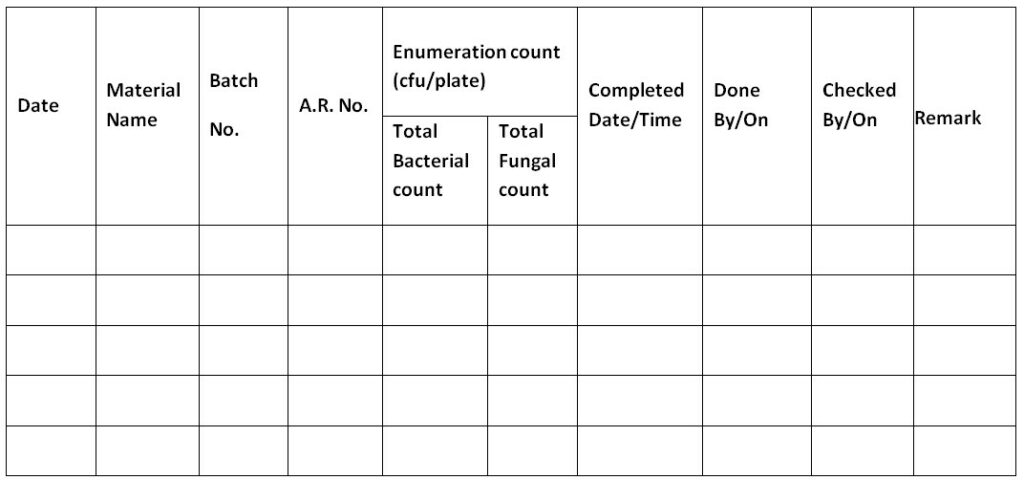
Name of Material | Type of Material | Batch No. | A. R. Number | Date of Sampling | Date of Analysis | Media Lot Number | Analysis Done by | Incubation Condition | Incubator ID No | Incubation Condition | Incubator ID No | Date of Completion | Observed by |
20-25°C For 72 hours | 30-35°C For 48 hours |