1.0 Purpose: To describe the procedure for monitoring and recording critical environmental parameters of different classes at the production facility.
2.0 Aim: This Standard Operating Procedure is applicable for monitoring and Recording Critical Environmental Parameters such as temperature, relative humidity, pressure differential, and non-viable particle count of a different class (class A, B, C, and D ) in the Production department.
3.0 Responsibility:
3.1 The line coordinator shall be responsible for carrying out the procedure as per SOP.
3.2 In-Charge/ Officer shall be responsible for checking and compliance with instructions and actions as mentioned in this SOP.
3.3 Head Production shall be responsible for the implementation of SOP.
3.4 Head- Quality Assurance shall be responsible for compliance with SOP.
4.0 Procedure:
4.1 Monitoring of temperature and relative humidity:
4.1.1 Continuously monitor the temperature of various areas that are connected with the centralized BMS.
4.1.2 Note down the temperature thrice during each working session or during the process session (start, middle, and end) with the help of a digital temperature cum hygrometer or as per company procedure.
4.1.3 The temperature and relative humidity of the room should be recorded in the
Annexure -1.
4.1.4 The temperature and hygrometer are operated as per the given SOP.
4.2 Monitoring of Pressure Differential:
4.2.1 Monitor the pressure differential of different areas from centrally installed Magnehelic gauges of the respective areas.
4.2.2 Record the pressure differentials of different areas from the Magnehelic gauge twice a day once in the morning before the start of work and the second reading recorded in the evening after the finish of work or as per the company procedure.
4.2.3 Record the pressure differential readings in Annexure – 2.
4.2.4 Also record the pressure differential in BMR of formulation & blending and filling areas thrice during each process session (start, middle, and end).
4.2.5 The pressure differential of the room should be within the specified limit as shown in Annexure – 2.
4.2.6 Monitor and review the status of differential pressure of the room round the clock including working and non-working hours and verify the printout of the differential pressure reading taken from BMS (Building Maintenance System). Archive the record in the respective file.
4.3 Monitoring of non-viable particle count:
4.3.1 Formulation area: – The particle count shall be carried out once each day for grades A and B during the blending process or any working session.
4.3.2 Filling area: – Continues particle monitoring system monitors the non-viable particle in class A and the particle count shall be carried out once every day in class B.
4.3.3 Other critical areas: – The particle count shall be carried out once a day for grades A and B during the process or any working session. In grade C nonviable particle count shall be carried out once a week.
4.3.4 The sampling shall be done as per the points described in the “SOP on Procedure for Non-Viable Particle Count (Locations, limits, and Frequency).”
4.3.5 The apparatus used for airborne particle count consists of 6 channels for the detection of particle sizes of 0.3 microns, 0.5 microns, 1.0 micron, 5.0 micron, 10.0 microns, and 25.0 microns and 4 channels for detection of particle size of 0.3 microns, 0.5 microns, 1.0 micron, 5.0 micron.
4.3.6 Connect the air collection head to the counter place it near the critical point and run the counter.
4.3.7 Observe the recordings, take a printout of the results, and attach a photocopy of the printout with BPR.
4.4 Monitoring of viable count:
4.4.1 The quality department person will perform the viable particle count in the area by exposing media plates by different methods like settling plates, air sampling, and swabbing.
4.4.2 Personal monitoring (swabbing of different body parts and fingerprints) of persons working in the clean areas is to be done as per the given SOP.
5.0 Abbreviations:
SOP: Standard Operating Procedure
Rev.: Revision
No. : Number
QA: Quality Assurance
PR: Production
QC: Quality Control
BPR: Batch Processing Record
BMS: Building Maintenance System
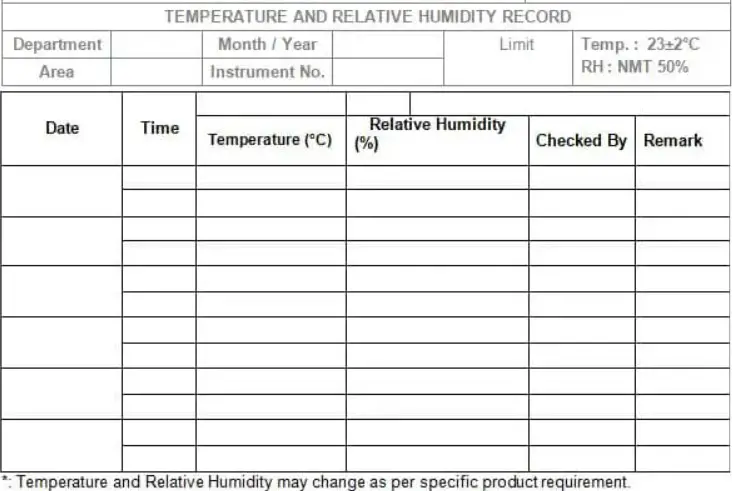
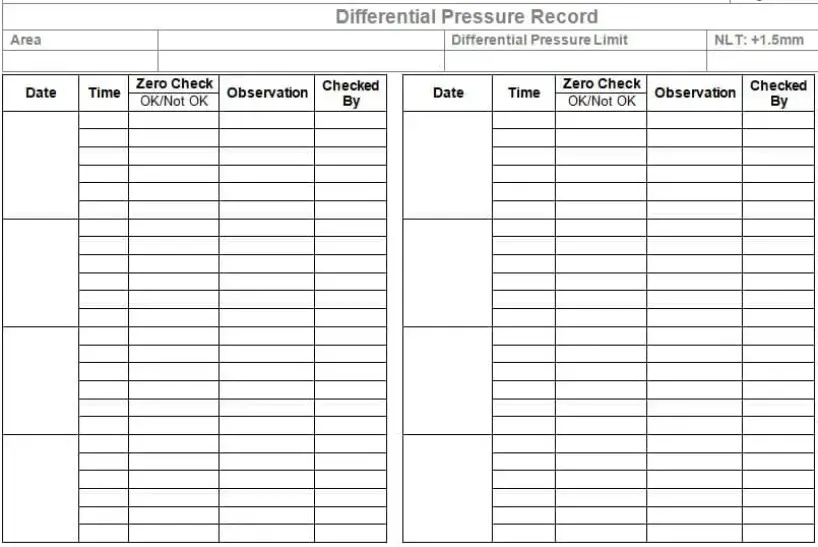