Standard operating procedure on Preparation, Qualification, Usage, Storage, and Destruction of Working Standards in Pharmaceutical Labs. Working standard SOP will cover the following points:
- What are Primary reference standards?
- What are Secondary reference standards?
- What is Working standards?
- Qualification of Standards working
- Preparation of working standard
- Analysis of working standard
- Filling of working standard vials
- Usage and validity of working standard
- Expiry / Validity /Destruction
- Handling of working standard
- Storage of working standard
- Disposal of working standard
1.0 Objective: 1.1 To lay down a procedure for the Preparation, Qualification, Usage, Storage, and Destruction of Working Standards.
2.0 Scope: 2.1. This procedure applies to the Preparation, Qualification, Usage, Storage, and Destruction of Working Standards used in the Quality Control Department in Pharmaceuticals.
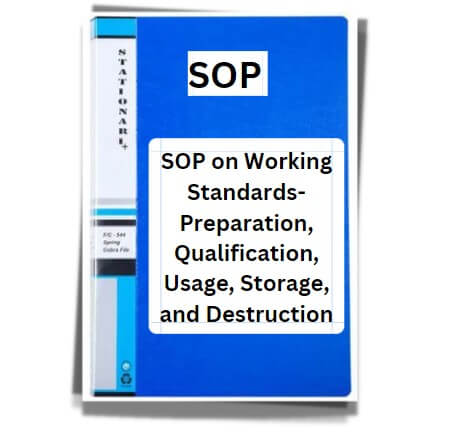
3.0 Responsibility:
3.1 Chemist/Officer/Executive QC shall be responsible for identifying the material for which Working Standard is required.
3.2 Chemist/Officer/Executive QC shall be responsible for the Preparation, Qualification, Usage, Storage, and Destruction of Working Standards.
3.3 The section in-charge shall be responsible for arranging the material in co-ordination with the Company, Various Vendors, and Material Suppliers, which is required to be Qualified.
4.0 Accountability:
4.1 Head-QC or his / her Designee shall be accountable for compliance with this SOP.
5.0 Procedure for Working Standards:
5.1 Working Standards:
5.1.1 Working Standards are the Substances that serve as the substitutes for the various Reference Standards.
5.1.2 Working Standards are qualified against the current Lot of the Reference Standards of the respective pharmacopoeia.
5.1.3 Working standards are suitable for routine usage only if they comply with the predefined acceptance criteria.
5.2 Source of Material:
5.2.1 For working standard preparation, select an approved raw material, having maximum purity, minimum levels of impurities, water content / LOD, minimum level of residual solvent, and maximum shelf life expiry date.
5.2.2 In case approved raw material is not available or its/their quantity is not sufficient, standard received from the manufacturer/ supplier, etc. with respective certificate of Analysis (COA) shall be used as a Working Standard, after assigning the Working Standard Number, as per the in-house criteria. (As described in 5.3.1 and 5.3.2)
5.2.3 Working Standard / Impurities, which were received from the manufacturer/supplier, etc. shall be accompanied by a Certificate of analysis.
5.2.4 On receipt of the respective Standard/Impurity, Certificate of analysis (COA), same shall be checked/ verified for Correctness, Completeness, and Compliance with respect to the In-House Acceptance Criteria and/or as per the respective Pharmacopoeia.
5.2.5 Certificate for the same shall be obtained either directly from the supplier/manufacturer or the same can be downloaded from the website of the respective manufacturer/supplier.
Related SOP: SOP for Analysis and Release of Packing Materials
5.2.6 The Purity mentioned on the respective Container and/or the Certificate of Analysis (COA) shall be considered for the Quantitation (Calculation) Purpose.
5.2.7 if the Purity of any such Standard is Not Mentioned on the label of the Container or in the respective Certificate of Analysis (COA), or due to some unforeseen reasons the COA is not available, then the same shall be considered as 100%.
5.2.8 After selection of the respective approved raw material, the chemist/officer-QC shall raise the requisition for the additional quantity required of Raw Materials for working standards get the approval for the same from the head / Designee-QC, and arrange from the warehouse for analysis.
5.2.9 Sampling of the material shall be performed as per the procedure followed usually for the respective raw material and draw the required quantity for use as per the Requisition slip from Container Only.
5.3. Batch Numbering System for Working Standards:
5.3.1 The following procedure shall be followed for the allocation of Batch Numbering of the Working Standard(s):
WS/XYZ/ZZ
Where,
WS: Stands for Working Standard.
XYZ: Stands for Unique Serial No. for each Working Standard Starting from 001.
ZZ: Stands for the last two digits of the Current Year.
5.3.2 If the working standard is received from XYZ Manufactures and is to be used directly as a working standard.
5.3.3 The Batch Number of each Working Standard shall be Unique.
5.3.4 if any Working Standard is required to be prepared More Than Once in a year, then the Batch number of the Working Standards shall be allocated as
WS/XYZ/ZZ/N
Where N, Represents the Alphabetic Numbering System,
For Example, A, B, C, D, and so on, indicate the number of times a Working Standard has been prepared again, after its initial Qualification, “A” indicates that a particular Working Standard has been prepared again, For the First time, “B” indicates for the second time, and so on.
5.4 Qualification of Working Standards:
5.4.1 Executive/ Designee QC shall assign an identification number to the working standard in Annexure-I and issue a ‘Working Standard qualification Report’ (Annexure-Il), to the analyst.
5.4.2 Working Standard Report shall contain the following:
5.4.2.1 Description / Appearance.
5.4.2.2 Identification.
5.4.2.3 Loss on Drying / Water Content (Wherever Applicable).
5.4.2.4 Assay/Purity
5.4.2.5 Miscellaneous parameter(s) (Wherever Applicable).
5.4.3 Allot the Number to the working standard Report as:
WSR/XYZ/ZZ
Where,
WSR: Stands for Working Standard Report.
XYZ: Stands for Unique Serial No. for each Working Standard Starting from 001.
ZZ: Stands for the last two digits of the Current Year.
5.4.4 Numbering of more than one report (If any working standard is prepared more than once in a year) shall be allocated as:
WSR/XYZ/ZZ/N
Where, N represents Alphabetic Numbering System e.g. A, B, C, and so on.
5.4.5 Record the Description’ Appearance of the material under analysis.
5.4.6 Test for the Identification shall be performed in single. If there are two or more identification tests mentioned in the Method of analysis then preferably perform the identification test by instrumental analysis only.
5.4.7 Loss on Drying / Water Content shall be performed in triplicate and consider the average value for the calculation of assay.
5.4.8 Test for “Assay” shall be carried out in Triplicate of the Material under qualification and Single preparation of the Reference Standard), and report the Average as the final value.
5.4.9 Report the assay value, and loss on drying /water content in two digits after decimal.
5.4.10 The analyst shall perform all the respective analysis as per Company specification and MOA or respective Pharmacopoeia monograph for the required test.
5.4.11 The Analyst, who is qualifying a Working Standard must be validated.
5.4.12 Qualify the respective working standard material against the current lot/batch of the respective Pharmacopoeia reference standard or previously approved working standard for quantitative analysis.
Related SOP: SOP on Receipt and Handling of Laboratory Samples
5.4.13 In case of qualitative estimation (i.e. Reference standard is required for identification purposes only) is to be carried out and a reference standard is not available then the following criteria shall be followed:
5.4.13.1 Previous working standard (not expired) shall be used to qualify the respective identification for new working standard.
5.4.13.2 Working standard shall be directly procured from an outside source as a secondary standard.
5.4.13.3 Working standard shall be sent for Identification against a reference standard to the outside testing laboratory.
5.4.14 Make all respective entries in the “working standard qualification report. Annexure II and attach the respective chromatogram(s), spectra, and supporting data(s) wich the report itself.
5.4.15 After the qualification of the Working Standard, the “Certificate of Analysis” shall be prepared as per annexure-lll.
5.4.16 Details of working standards shall be maintained in the ‘Working Standard summary sheet’, as per Annexure-IV.
5.4.17 A “Working Standard Usage log” shall be maintained, as per Annexure- V.
5.4.18 If the facility to perform any test is not available in the faculty, perform the same test from approved outside laboratories.
5.4.19 If the Reference Standard Quantity is less than that of the specified in the respective test procedure, the dilution for the preparation of the same can be reduced without changing the final concentration of the solution, and the same shalt be documented with prior permission of the Head/ Designee-Qc.
5.4.20 Any instruction given on the label of the Reference Standard shall be followed accordingly.
5.4.21 In the case of vitamin working standard, validity is of six months only.
5.5 Acceptance Criteria for the Qualification of Working Standard:
5.5.1 All the Results/Observations should be within the pre-defined Acceptance Criteria (i.e. should comply with the specification of the respective material).
5.5.2 Acceptance criteria for the determination of Water Content / LOD:
Water Content / LOD, (Spec. Limit) % RSD (for Triplicate Determinations)
- Up to 1.0% Not More Than 20%
- 1.0% To 3.0% Not More Than 15%
- 3.0% To 5.0% Not More Than 10%
- 5.0% To 10.0% Not More Than 7.5%
- Above 10.0% Not More Than 5.0%
5.5.3 All the Results/Observations should be within the pre-defined Acceptance Criteria (ie. % RSD of the triplicate assay results should not be more than 1.0%).
5.5.4 The Report and Supporting documents (For Example Weight Printouts, GC/HPLC/TLC Chromatograms, UV/ IR Spectra, etc.) shall be handed over to the Section head/ Designee QC.
5.5.5 After the review of the report and other supporting documents the same shall be submitted to Head/designee -QC for Approval.
5.5.6 If the Working Standard is Not Complying with the acceptance criteria, then the same shall be investigated as per the SOP for “Investigation of out of Specification Results” till phase-IW/Laboratory investigation stage.
5.5.7 If during Investigation, No Assignable cause for failure is found, either re-sample the material! From the same batch of the respective material or if available, sample and reanalyze the material from another batch, which satisfies the basic requirements mentioned under 5.2.
5.5.8 If the Assay (Average Value) of the Working Standard is More Than 100%, then it shall be considered as 100%, except that of vitamins.
5.5.9 If the COA of the working standard is required to be sent to an outside laboratory/country, take a printout of the same with the word “reprint” below the remark and all signatures shall be made on the current date.
5.6 Preparation, Labeling and Storage:
5.6.1 Fill a sufficient quantity of the Working Standard in each of the clean, dry, amber-colored, glass vials.
5.6.2 Close the vials tightly with screw cap / Crimp with the help of a rubber closure and aluminum seal, to protect it from moisture and light.
5.6.3 Prepare 15 vials of each Working Standard for the usage in entire year. In the case of vitamins prepare 8 vials (6 vials for each month, 1 vial as backup, and 1 master vial)
5.6.4 A total of 12 vials should be prepared for routine (Monthly) usage and 2 vials shall be prepared as a backup for the routine (Monthly) usage vials, so that in case of any contamination/ breakage of any vial / more consumption of the respective standard, the same can be replaced from the backup vial. 1 Master Vial, Containing about three times the quantity filled in individual vials of the respective Working standards shall be prepared. The material from this vial shall be used in case the same is required to be sent to the company, regulatory affairs, other locations of the company, Extemal-approved contract laboratories, Government agencies, Any Regulatory Agency, etc.
5.6.5 Paste the label on the vial(s) as per Annexure-VII.
5.6.6 The record of working standards sent to the above-mentioned location shall be recorded in a register/logbook having required information e.g. Sr. no., Name of working standard, Pharmacopoeia status, date of request, quantity required, vials required, required for, requested by, sent on, sent by, and remarks, etc.
5.6.7 Keep only one vial for routine use and store the rest of the vials separately in the refrigerator, in accordance with the Storage Condition(s) of the respective material. If the working standard procures in a single vial from any external source then the same vial should be used up to the validity of the working standard.
5.6.8 All the Vials for routine usage shall be stored as specified on the label of the respective vial in desiccators.
5.6.9 Once a vial is opened for usage, it should be tightly closed to protect it from moisture and light.
5.6.10 Ensure that the desiccant (Self-indicating Silica gel) is not decolorized, in case it is decolorized, regenerate the same or replace it with fresh silica gel.
5.6.11 In the case of Excipient working standards, the pre-approved batch can be used as a working standard.
5.6.12 In case of a working standard that is used more frequently or on a regular basis, more than 15 vials can be prepared.
5.6.13 A list of working standards will be prepared on a monthly basis as per Annexure -I
5.7 Expiry / Validity /Destruction:
5.7.1 All Working Standards shall be Valid for 12 Months from the date of effective Qualification.
5.7.2 If material expiry is less than one year, then the validity period of the respective standard shall be assigned accordingly.
5.7.3 Individual vials of Working Standard Shall be Valid for One Month.
5.7.4 Every month on the first week, a new vial shall be taken for routine usage, and destroy the existing vial as per respective SOP for destruction and the destruction record shall be maintained as per Annexure-VI.
5.7.5 In cases where a specific material is non Pharmacopoeial, and no reference standard is available, in such cases, Standards received from the Company R&D / ADL Centre, Other locations of the Company, From the respective Manufacturer / Supplier, any Government / Regulatory agency, Authenticated Chemical / Reagents manufacturers (e.g. Fluka, Merck, Lancaster, Sigma Aldrich, Rankem, JT Baker, etc.), or other Primary Standards shall be considered as Reference Standard and the Working Standard shall be qualified against it.
5.8 Precautions:
5.8.1 Always transfer only the required quantity of working standard from the respective vial during usage.
5.8.2 Never transfer the remaining quantity of working standard back to the original vial.
5.8.3 If the respective Working Standard is stored at 2 to 8°C, Never use it for analysis immediately after taking it out from the refrigerator; keep the vial in a desiccator to attain ambient temperature.
5.8.4 Never keep the vial open for longer durations, extra care shall be taken while handling hygroscopic materials.
5.8.5 Always use Photosensitive (Light sensitive) materials under the prescribed conditions only,
5.8.6 Never insert any external device, such as a spatula, glass rods, or butter Paper into vials, as it may contaminate the working standard.
5.8.7 Use ‘resh capillary tubes only while weighing the liquid working standard.
5.8.8 Immediately return the respective Standards to their designated storage location after usage.
5.8.9 Only the standards that are not expired (are within the validity period) shall be used for analysis.
5.8.10 Always follow the safety instructions and wear the appropriate Personal Protective Equipment.
6.0 Reference:
AS Per GMP Guideline.
7.0 Annexures / Attachment:
Annexure – I: List of Working Standards
Annexure – II: Working Standard Qualification Report
Annexure – III: Working Standard Certificate of Analysis
Annexure – IV: Working Standard Summary sheet
Annexure – V: Working Standard Usage Log
Annexure – VI: Working Standards Vial Destruction Record
Annexure – VII: Specimen label for Working Standard.
8.0 Distribution:
Master Copy: Quality Assurance Department.
Cont~olled Copy: Quality Control Department.
Display Copy: Chemical Analysis Lab.
10.0 Abbreviations:
SOP: Standard Operating Procedure
Qc: Quality Control
IP : Indian Pharmacopoeia
BP : British Pharmacopoeia
USP : United State Pharmacopoeia
MSDS: Material Safety Data Sheet
COA: Certificate of Analysis
LOD: Loss on Drying
MOA: Method of Analysis
LAF: Laminar Air Flow
RSD: Relative Standard Deviation
R&D: Research & Development
ADL: Analytical Development Lab.
RSD: Relative Standard Deviation
GC: Gas Chromatography
HPLC: High-Performance Liquid Chromatography
TLC: Thin Layer Chromatography
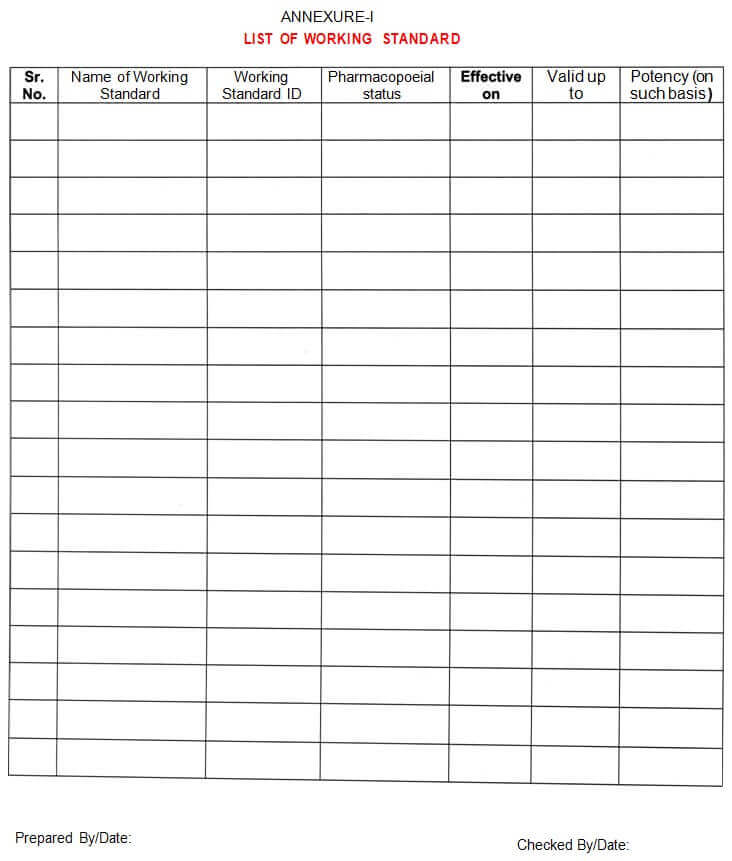
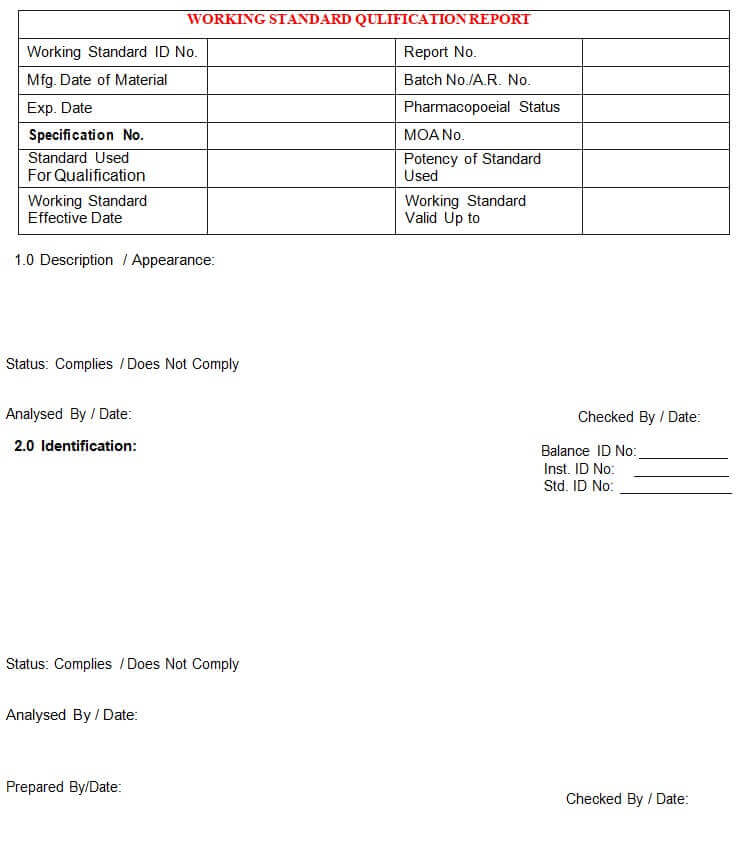
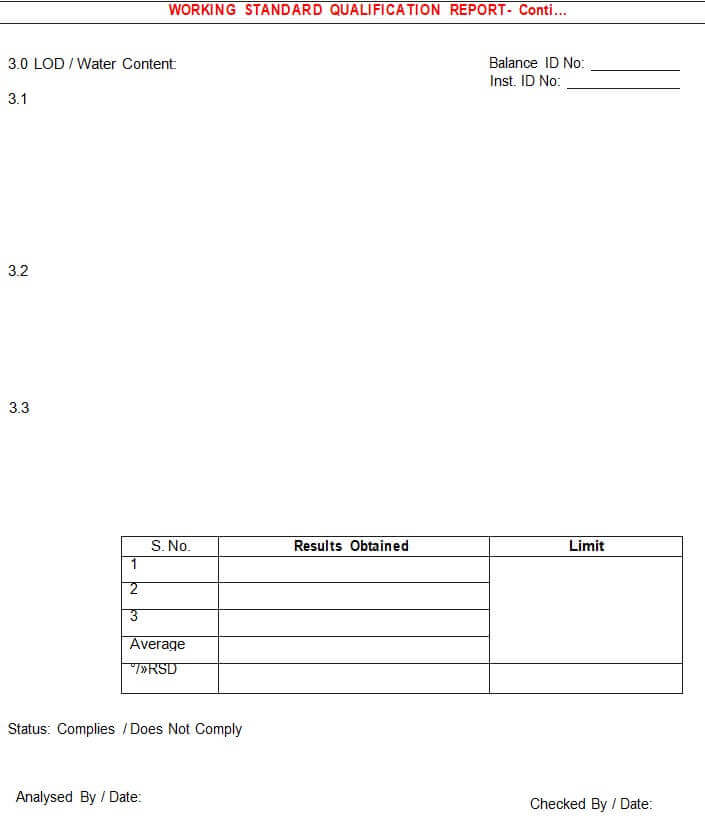
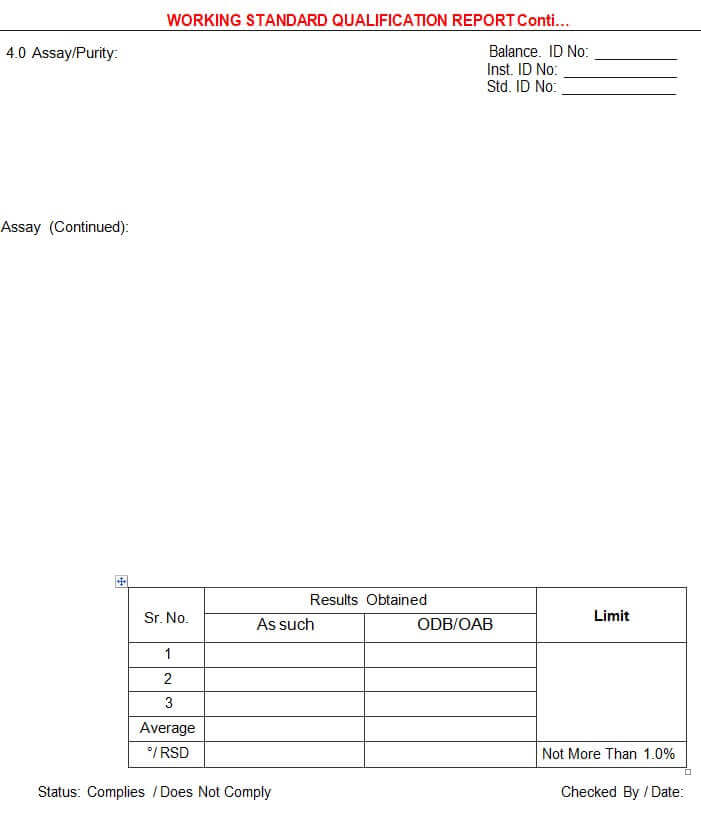
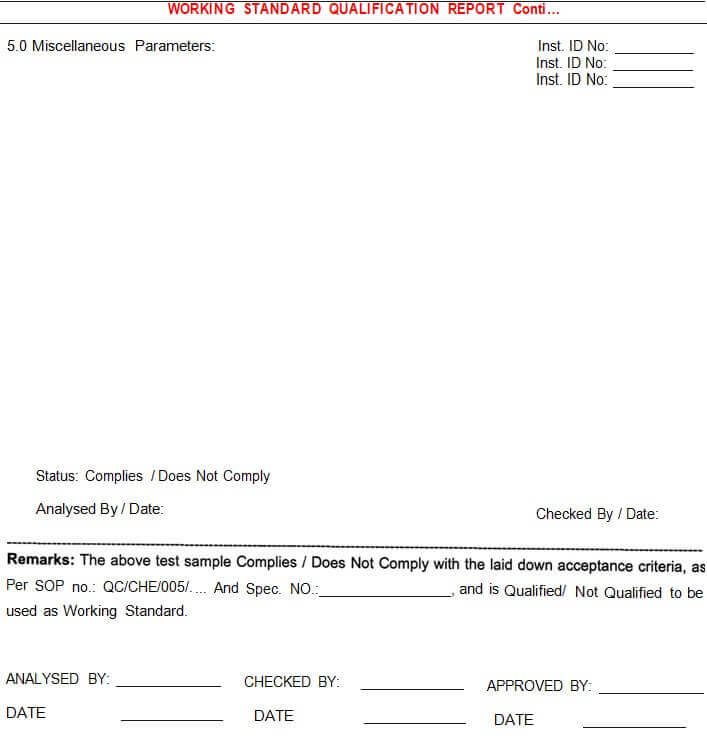
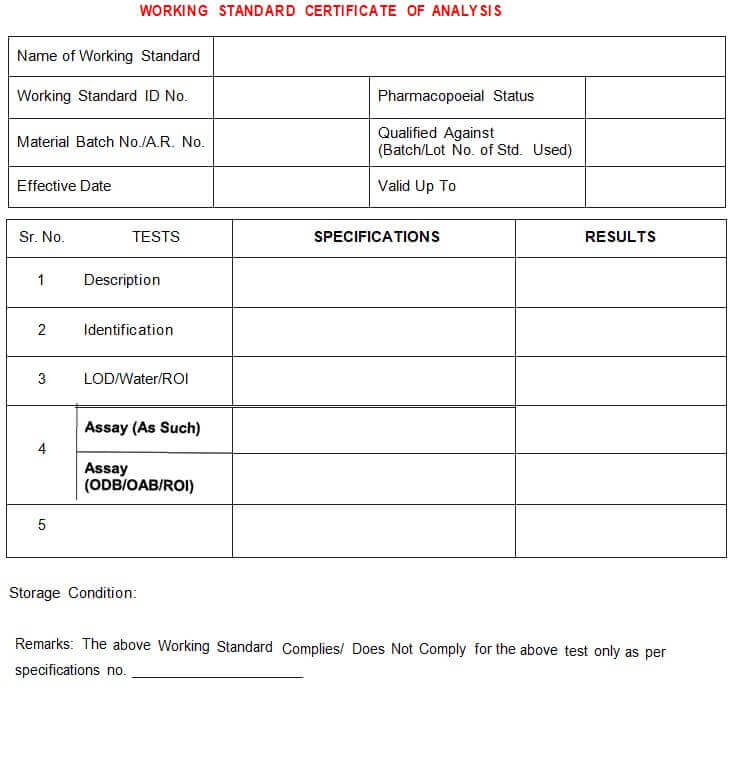
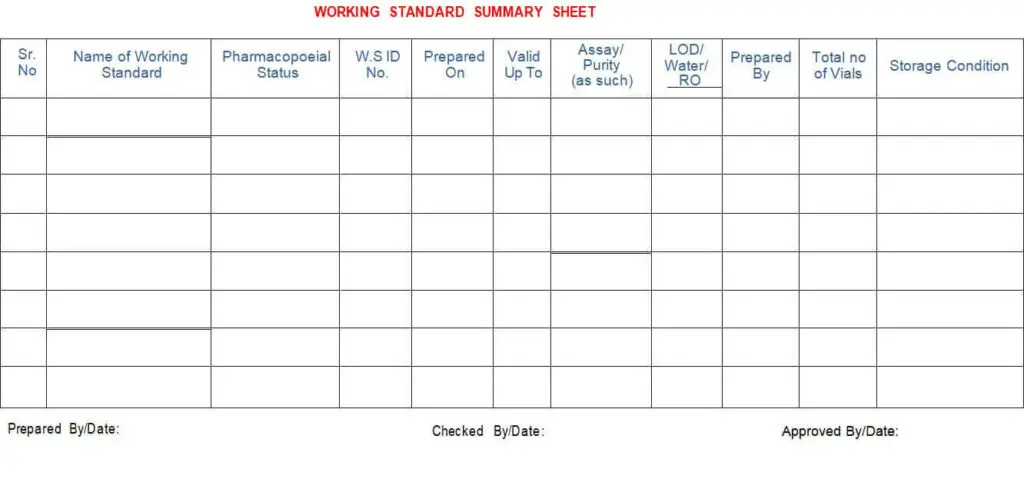
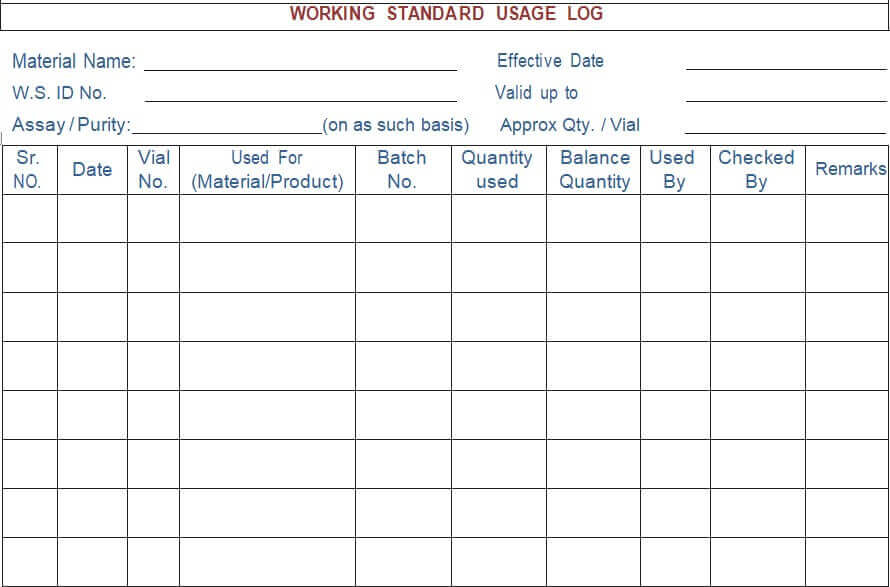
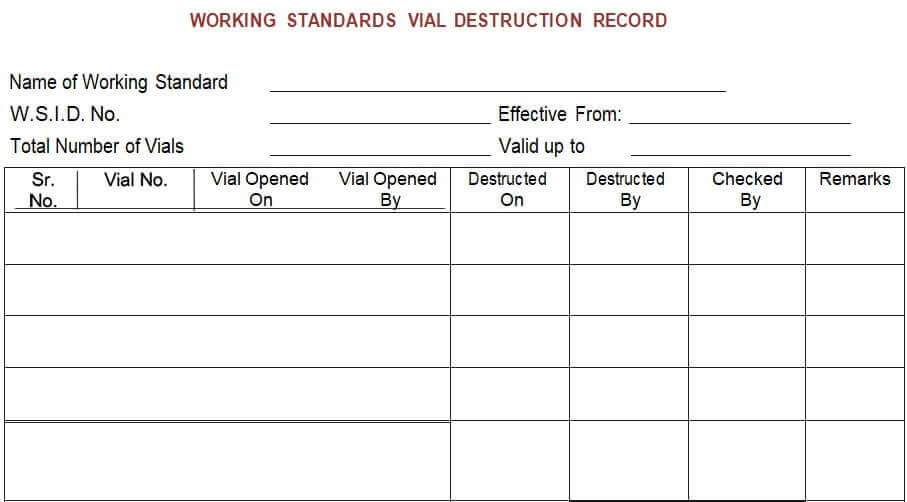
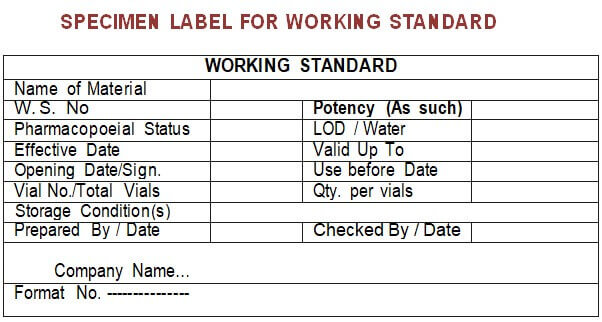