The procedure is applicable to the general procedure for filling the vaccine in the manufacturing area.
Preparation of Primary packaging material for filling:
- Receive the primary packaging material from the store as per the requisition slip.
- Transfer the rubber stopper and seals to the material preparation area for sterilization.
- Transfer the glass vials to the box-cutting area and Process of rubber stoppers.
- process the aluminum seal and De-cartoning of glass vials followed by Washing of glass vials and Depyrogenation of glass vials.
Preparation of Filling Machine parts :
Note: If required take the change over to the required format size 2ml, 3ml, or 5 ml format.
Wash and prepare filling machine accessories and pack the required size of Piston’s needles and manifold as per the fill volume requirement.
Check Points Before Filling:
- Before the start of the operation check for a complete changeover of the machine parts and their fixation.
- Recirculation of product from the machine product tank to the formulation vessel shall be required in case of Gel-based batches and in clear solution-based batches this recirculation is not required.
- Physically check the sterilization status of filling machine parts, stoppers, and seals.
- Before starting filling activities ensure that LAF shall be in operation before 30 minutes.
- Check and record the differential pressure of the filling room and filling LAF.
- Ensure that environmental monitoring activities in the filling area start before filling.
- Ensure that caps of online particle count probes are removed and data is recorded.
- Line clearance shall be taken from the IPQA person.
- Records the activity like; filling, record the temperature, relative humidity, room pressure, and differential pressure of LAF as per given frequency.
Procedure for filling:
- Take the line clearance from the IPQA person.
- Aseptically fix the filling machine parts, In case of gel-based batches connect the recirculation connections for recirculation of product from the machine product tank to the formulation vessel.
- Recirculation of the product shall be done with a peristaltic pump having reset parameters
- Aseptically transfer the sterilized rubber stoppers into the stopper hopper.
- Check all the parameters required for the operation of HMI
- Start the batch on the filling machine
- Calibrate the IPC weighing module and check the printout.
- Then start the priming process of filling needles for removal of air from filling needles.
- Collect the priming volume in the “Priming collector”.
- Aseptically transfer the Priming volume into the Nalgene bottle and send it to QC for sterility testing.
- For small batch sizes, the priming shall be done directly into glass vials which shall be sent to QC for sterility testing.
- Start the filling of the vaccine in vials.
- The filled & stoppered vials are sealed with an aluminum seal.
- Transfer the sealed vials to the cold room till visual/Automatic Inspection, labeling & packing.
- After completion of filling stop the batch and aseptically collect the leftover bulk in a sterile Nalgene bottle for sterility testing.
- Decontaminate the rejected vials during the filling.
- Transfer the leftover sterilized material (stopper and seal) to the decontamination area.
- Decontaminate the opened or intact sterilized rubber stopper bags.
- Remove the machine parts and send for decontamination.
- Clean the machine with 70 % IPA and fill the area as per the area cleaning process.
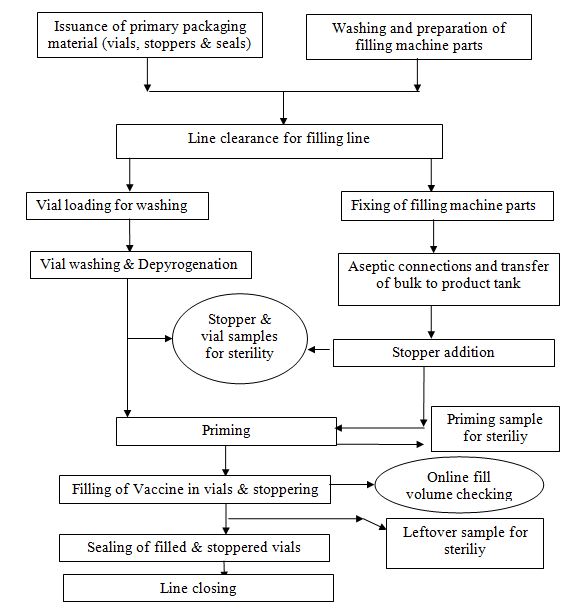
Sampling During Filling:
Collect the priming sample aseptically and send it to QC for sterility testing as per the sampling plan.

Naresh Bhakar is the Founder and Author at Pharmaguddu.com, bringing his extensive expertise in the field of pharmaceuticals to readers worldwide. He has experience in Pharma manufacturing and has worked with top Pharmaceuticals. He has rich knowledge and provides valuable insights and data through his articles and content on Pharmaguddu.com. For further inquiries or collaborations, please don’t hesitate to reach out via email at [email protected].