Laboratory Incident Definition: Any unintentional or unexpected event occurring during, discovered within, or arising after analysis that may adversely impact the quality of data and the resulting outcomes.
Types of Common Laboratory Incidents:
Below are the different common types of lab incidents in the pharmaceutical field that often occur.
- Human errors: e.g., Wrong weight taken, the wrong solution prepared, wrong selection of instrument method, and lack of training.
- Instrument errors: e.g., System suitability failure, standard bracketing failure, column leakage, connectivity failure, and power failure.
- A standard error also includes Method errors: e.g., Poor column performance, diluent or mobile phase ratio, and distorted peak.
Type of Lab incident:
Laboratory incidents may be of general and Instrumental types as follows:
1. General incident:
- Is the sample taken wrongly?
- Lack of knowledge of the person who is working in a laboratory
- Error in standard sample preparation
- Weighing error happened
- Error in diluent volume/ or diluent used
- Glassware breakdown during the standard solution process.
- Error with the mobile phase or maybe a mixing error
- Error in pH management
- HPLC/ GC handling
- Power failure during instrument operation
- The wrong injection volume injected
2. Instrumental error:
- Use out-of-calibrated instruments.
- Failure of lamp intensity
- Column Leak, Poor Plate Count, Poor Resolution
- It may be a Connection problem between the software and Instrument.
- The wrong specification selected in LIMS was observed while registering Product brand/material before product/material release.
- A Chromatographic peaks failure between the sample subset.
- Improper separation (merging the components) was observed in chromatograms during the chromatographic analysis.
- System failure was observed during the analysis because of column’s high pressure/ Instrument.
- End value may affect calculation errors or false reporting observed after the release of materials/products.
- In the case of bracketing of standards in assay, content uniformity, dissolution, dissolution profile, and deviation from specified limits.
- It may be due to Calibration failure during the quarterly/daily calibration procedure.
Flow Chart for How to Handle Laboratory Incident

Handling of Laboratory Incident Steps:
- When an analyst identifies atypical results or becomes aware of laboratory or procedural errors occurring during testing, they will annotate the atypical results or known laboratory errors in the appropriate lab logbook.
- Inform to laboratory supervisor.
- The investigation report ensures the proper preservation of all starting materials, solvents, and intermediate materials. It also includes the standards for intermediate and final solutions used in the testing.
- These materials will be retained and preserved until the completion of the investigation or until they are no longer helpful. Laboratory investigations will be initiated within one business day after discovering the OOS/atypical result. They will be completed within 15 business days unless the laboratory supervisor and QA grant a written extension.
- The supervisor immediately reviews the results, lab logbook, starting materials, all used solutions, raw data, and the calculations used to generate the final results. A comprehensive error review of the laboratory investigation report is conducted using the Report Errors Checklist (a blank Errors Checklist is attached to the Guidelines utilized in each factory).
- The checklist will be completed by the supervisor and analyst together. The supervisor will interview the analyst and can check relevant documents in order to answer questions that can help identify whether common or obvious laboratory errors were the basic explanation for the OOS/atypical result.
These Questions will include the following, provided as examples, and not intended to be inclusive.
- Did the analyst receive training on the test method?
- Did we use the latest version of the method?
- Was the correct test method utilized?
- Was the test method procedure appropriately followed?
- Does the logbook documentation indicate any procedural errors?
- Did the review of starting materials, solvents, solutions, and glassware take place?
- Does the laboratory work area show any gaps?
- Was the sample used during the process correct?
- Was the sample spilled or contaminated before testing?
- Ensure that the proper standard reference solution is prepared and used.
- Is the laboratory area under environmental control (e.g., temperature and humidity)?
Read more: Calibration of UV-visible spectrophotometer
Note: We also need to analyze incident trends to easily identify the types of incidents that occurred before and their frequency.
Laboratories incident form no. (Annexure-1)
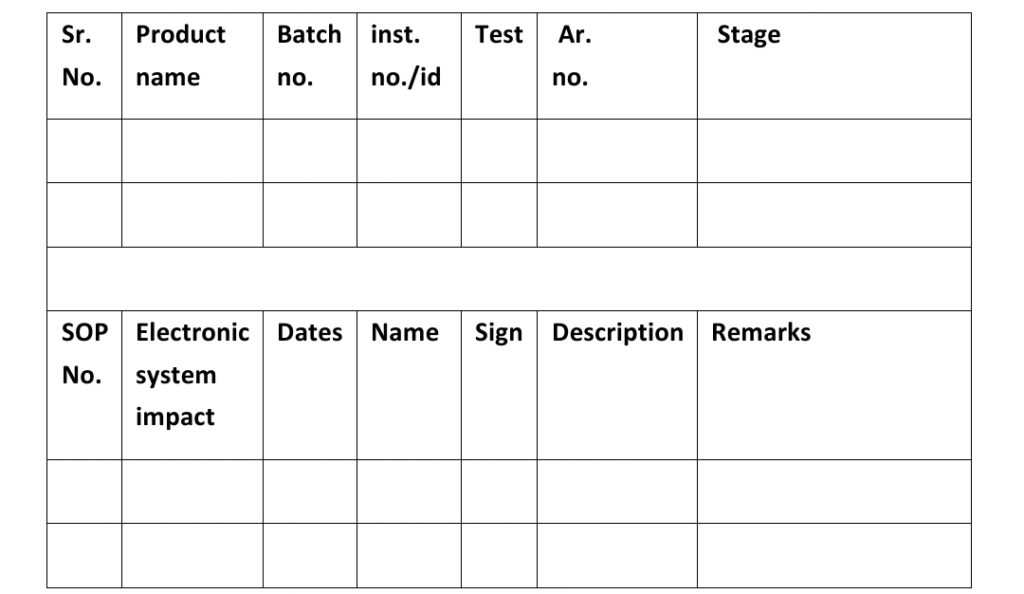
Lab Incident Checklist point :
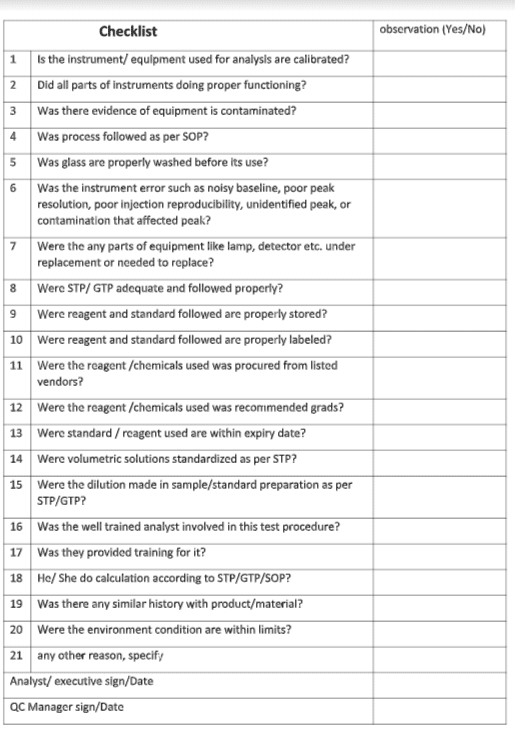
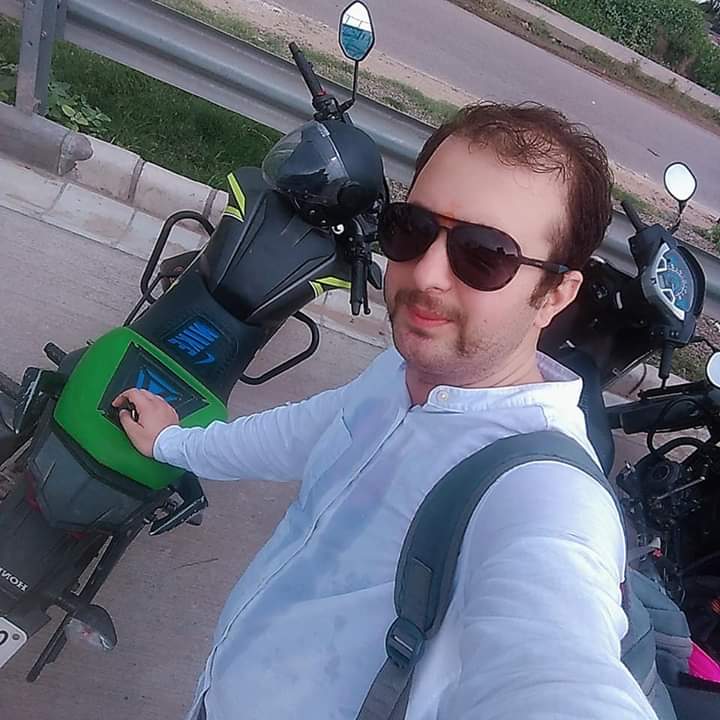
Panks Pamyal is a Author and Editor at Pharmaguddu.com. He Worked in Top Pharmaceuticals MNCs in India had a more then 10 years experience in Quality control department. He Delivering most valuable insights and knowledge through this website.