Recall and complaints both are different things that are used for marketed products. Recall means a company’s removal and correction of a marketed product that the FDA considers to be in violation of GMP. The Recall does not include market withdrawals. Whereas for product Complaints is not good things. It shows customer dissatisfaction with the manufacturer’s products.
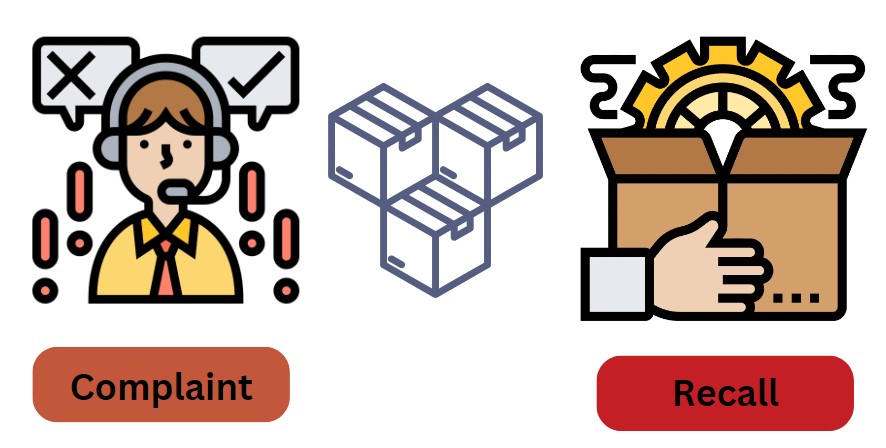
1. Complaints
Product complaint Principle:
“All complaints and different information regarding the probably defective product should be reviewed as per written procedures.”
Objectives:
- To identify the key problems in product complaint and recall handling.
- To understand the particular necessities for organization, procedures, and resources.
- To understand and develop actions to resolve current problems applicable to you.
Complaints Handling Principle:
- All complaints and different information regarding the probably defective product should be carefully reviewed as per written procedures and Should be Handled positively and thoroughly after review.
- It Must be Handled by a senior person through an investigation of the causes, which is crucial.
- Enable potential production defects to be remedied before they lead to a recall.
- Necessary actions are to be taken, even a recall and complaints.
Complaints Procedure – I
Complaints Procedure – I Must include the following:
- Must be a Designated accountable person or authorized trained person. If not, should advise an authorized person.
- Sufficient support staff.
- Access to records.
- Written procedure describing the action to be taken.
- Acknowledge and answer the complainant in an affordable reasonable manner.
- The record has written and verbal comments.
Complaints Procedure – II
Complaints Procedure – II Must include the following:
- Investigate and review
- QA review complained
- Appropriate follow-up actions
- Trends Review
Records Details of Recall and Complaint Investigation:
- Name of product
- Name of the active substance, if applicable.
- Strength and dose form.
- Manufacturing or packing Batch No.
- Name of the complainant and nature of the Complaint.
- Records, Retention sample (control sample) investigated, different batches reviewed and interviewed of the involved person.
- Result of investigation: “Justified” or “Not justified.”
- If “justified”, actions are taken to stop reoccurrence.
- Sign-off upon completion.

The Decision from a Complaint Investigation:
Justified Complaint
- Actions to stop reoccurrence.
- Ongoing observation of the processing method.
- Recall product may be needed.
Non- justified Complaint
- Advise the client of findings.
- Appropriate selling response.
Other Problems Related to Recall and Complaints:
- Regular review of trends is needed.
- Reoccurring issues
- Potential Recall or withdrawal
- Inform competent authority of significant quality issues.
Classification of Defects
“If the complaint is valid, then there has been a failure of the standard quality system. Once the defect is known, a company ought to handle it in an appropriate manner, even if it requires a recall.”
Defects Types include:
- Critical defects:
- Major defects:
- Other defects:
Read about: Types of Defects
2. Recall
Reasons for Recall:
- A Complaints from the customers.
- Detection of GMP failure when products reach the market.
- The result from the continued stability testing.
- Request by the national inspection authorities.
- Result of associate review.
- Known counterfeiting or change of state.
- Reporting any adverse reaction.
Detection of GMP failure:
Blister with empty or broken tablets in a blister pack.
Product Recall Principle:
“There ought to be a system to recall from the market promptly and effectively, product renowned or suspected to be defective.”
Recall Definition:
- Removal from the market of fixed batches of a product.
- Maybe one batch or all batches of product.
Designated accountable Recall Person:
- Maybe the well-trained person. If not, should advise a well-trained person.
- Sufficient support employees for the urgency of the Recall.
- Independent of sales and selling.
- Access to records.
SOP for Recall:
There shall be an Established, authorized procedure for action taking. It should be checked and updated. Capable of fast operation at the hospital and pharmacy level. Communication ideas to national authorities and internationally.
Distribution Records:
There shall be a well-trained person for recall functions, Distribution records shall be Accurate and must-have information on Wholesalers, Direct customers, Batch numbers, and Quantities.
Written Report and reconciliation
- Record progress as the procedure followed.
- Reconcile delivered with the recovered product.
- Issue final report.
- Effectiveness of procedures checked.
- Test effectiveness from time to time.
- Secure divided storage of products that are returned.
Possible Problems during Recall:
- No response to Valid complaints.
- Response to unreasonable complaints.
- Failure to recall.
- Failure to correct frequent complaints.
- No resources to research.
- No senior management support.
- Senior management interference.
- No distribution information/batch records.
- No access to records.
- Inability to contact the government throughout holidays/weekends.
- Disagreement on the severity of the defect.

Naresh Bhakar is the Founder and Author at Pharmaguddu.com, bringing his extensive expertise in the field of pharmaceuticals to readers worldwide. He has experience in Pharma manufacturing and has worked with top Pharmaceuticals. He has rich knowledge and provides valuable insights and data through his articles and content on Pharmaguddu.com. For further inquiries or collaborations, please don’t hesitate to reach out via email at [email protected].