SCADA stands for Supervisory Control and Data Acquisition. It is a collection of software and hardware components that enable local and remote plant monitoring and control. Furthermore, the SCADA analyzes, collects, and processes data in real-time.
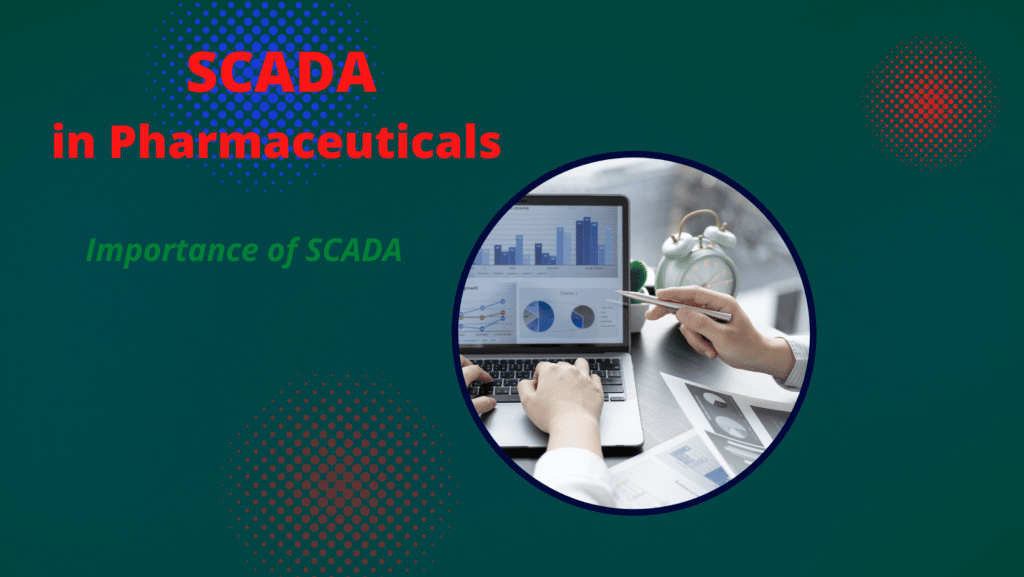
SCADA Functions
Users can communicate with field devices such as pumps, valves, motors, sensors, and more using human-machine interface (HMI) software. The SCADA software also has a logging feature for historical data. A standard SCADA structural design begins with Remote Terminal Units, or RTUs, and/or Programmable Logic Controllers, or PLCs. RTUs and PLCs, as you may be aware, are microprocessors that communicate and interact with field devices such as valves, pumps, and HMIs. That communication data is routed from the processors to the SCADA computers, where the software interprets and displays it, allowing operators to analyze and respond to system events.
Before SCADA, plant staff had to use analog signals such as selector switches, push buttons, and dials to monitor and manage industrial processes. This meant that plants needed to keep personnel on-site during production to control the processes.
Relays and timers were used to assist in the supervision and control of processes as manufacturing developed and sites became more remote in nature. With these devices in place, fewer plant personnel were needed on-site to oversee and control operations. While relays and timers provided some automation, the panels required for these devices took up valuable real estate, troubleshooting was a nightmare, and reconfiguring was at best difficult. These issues, combined with the need to build larger industrial plants, facilitated the birth of automation.
SCADA was used to describe systems equipped with PLCs and microprocessors that were used to monitor and control automated processes on a larger scale than ever before. SCADA was anything but practical back then. They were massive machines, really mainframes, and because networking was not yet available, they were stand-alone units. SCADA systems were able to connect to related systems in the following decades, the 1980s and 1990s, as computer systems became smaller, Local Area Networking (LAN) and HMI software became available.
Unfortunately, the communications were typically proprietary, which meant that connections outside of the SCADA system’s specific vendor were not permitted. The early it was known as distributed systems. Later in the 1990s and early 2000s, SCADA began to implement open system architectures with non-vendor-specific communication protocols.
Mordren SACADA System:
Because SCADA developers did not use standard databases, SCADA fell behind when other technologies changed so quickly. Modern SCADA systems have adapted to changing technologies and have a significant advantage over older SCADA systems. Today it allows real-time plant information to be accessed from anywhere in the world thanks to the adoption of modern IT standards such as SQL and web-based applications.
Having the data at the operator’s fingertips improves plant operations by allowing responses to SCADA system queues based on field-collected data and system analysis. These operator interactions can range from a computer on the plant floor to an office building in another part of the world.
Related Post:
- List of Quality Control Equipment in Pharmaceuticals
- List of Pharma Equipment in Production Sections
Indeed, advances in technology have made the world appear to be a relatively small place. And, because the current SCADA system software has typically adopted the SQL database model, historical data collection may be logged and used in trending applications to further improve plant processes while also creating mandated record-keeping for some industries. SCADA is essentially a collection of hardware and software components. The set of components starts with real-time data from plant floor devices like pumps, valves, and transmitters.
The components do not need to be from a specific vendor; they simply need to support a communication protocol that the processor can use. Data collected from field devices is then routed to processors like PLCs.
The processor transmits data to a system of networked devices. Examples of such devices include servers, end-user computers, and HMIs. On the HMI and end-user computer, graphical representations of operator interactions, such as starting pumps and opening valves, are available. The data can also be analyzed and used to improve plant output and troubleshoot issues.

Naresh Bhakar is the Founder and Author at Pharmaguddu.com, bringing his extensive expertise in the field of pharmaceuticals to readers worldwide. He has experience in Pharma manufacturing and has worked with top Pharmaceuticals. He has rich knowledge and provides valuable insights and data through his articles and content on Pharmaguddu.com. For further inquiries or collaborations, please don’t hesitate to reach out via email at [email protected].