Learn About Standard Operating Procedure on Storage and Hold time Study for Products along with their Purpose, Scope, Responsibility, Definition, Procedure, Selection of Test parameters, Sampling Interval/volume, and container, Hold time study at different stages, and Documentation.
1.0 Purpose: 1.1 To lay down Standard Operating Procedure for Storage and Hold Time of Starting Material, Intermediate, and Bulk Products.
2.0 Scope: 2.1 This SOP is applicable to Starting Materials, intermediate, and bulk materials of Tablets. Oral Hygiene, External Preparations, and Liquid Oral preparations.
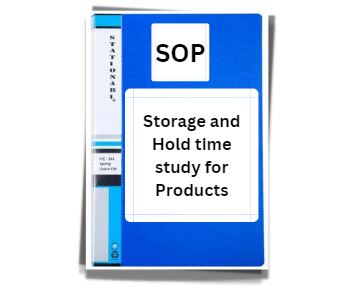
3.0 Responsibility:
3.1. Quality Assurance:
3.1.1 The quality assurance officer shall be responsible for the preparation/review & execution of the Hold Time Study protocol and Report.
3.1.2 The Quality Assurance officer shall be responsible for the collection of hold time samples during the hold time study as per approved protocol.
3.1.3 Head- QA / Designee shall be responsible for the approval of the Hold Time Study protocol and Report.
3.2 Manufacturing:
3.2.1 The Manufacturing Head / Designee shall be responsible for the review, approval, and hold time study activity as per protocol.
3.3 Quality Control:
3.3.1 The quality control officer shall be responsible for receiving and analysis of hold time samples.
3.3.2 Head — QC / Designee shall be responsible for review & approval of hold time study protocol and Report.
3.4 Engineering:
3.4.1 Head EG / Designee shall be responsible for providing the storage condition during the hold time study.
3.5 Head — Corporate Quality Assurance (If Applicable):
3.5.1 Corporate Quality Assurance shall be responsible for approval of the hold time study protocol and Report.
3.6 Marketing Authorization:
3.6.1 Marketing Authorization for approval of the hold time study protocol and Report.
4.0 Definition:
4.1 Hold Time study: Hold time can be considered as the established time period for which materials (dispensed raw materials, intermediates, and bulk dosage form awaiting final packaging) may be held under specified conditions and will remain within the defined specifications.
4.2 Bulk Product: Any pharmaceutical product that has completed all processing stages up to, but not including, final packaging.
4.3 Intermediate: Partially processed products must undergo further manufacturing steps before they become bulk products.
5.0 Procedure:
5.1 Hold time studies shall be performed on one validation batch. One or more batches of a material or Intermediate can be used for determining hold times.
5.2 The hold time for each category of material should be established on the basis of the study by keeping the material in either the original or simulated container used in production.
5.3 The containers in which hold time samples are stored should be the same pack as is used in production unless the pack is exceptionally large, in that case, one that is equivalent Above (constructed of the same material and using the same closure system as the product packaging system) may be used. Reducing the size of the container, when this is necessary for testing holding time, should be justified.
5.4 Where the headspace of containers used for bulk storage in Manufacturing and/or quarantine is important, for example, because of a risk of potential degradation as a result of oxidation, then the hold-time studies should represent worst-case conditions. In such cases, the ratio of headspace to contents in the test containers should be at least as great as the maximum that is possible in routine production.
5.5 A sampling plan should be established and followed for taking samples for testing at different intervals. The amount of sample required should be calculated based on the batch size. the intervals, and the tests to be performed.
5.6 Selection of Test parameter, Sampling Interval/volume, and container:
5.6.1. The sample shall be stored in the same pack / simulated condition used for storing the below-mentioned materials:
- Starting material: The sample shall be stored in Double polythene bags with minimum headspace and sealed in an S.S. container.
- Blend sample: A Bin made up of stainless steel is used for storing the blend hold time sample. Before the selection of the Stainless Steel bin, ensure the gasket is available to avoid moisture permeability.
- Core bulk tablets: The sample shall be stored in Double polythene bags with minimum headspace and sealed in an HDPE drum.
- Coated Tablets: The sample shall be stored in Double polythene bags with minimum headspace and sealed in an HDPE drum.
- Binder Preparation and Coating Solution: A Bin with an S.S. lid shall be used for the hold time study.
5.6.2 Hold time study shall be performed for the below-mentioned stage:
Test Parameters and sampling intervals may vary according to the specification and Product requirement. The sample size depends on the average weight of the product/specification or as defined in the respective Hold time study protocol.
ANNEXURE-1

5.6.3 The starting material/bulk / Intermediate material subjected to hold time study shall be stored as per the environmental condition mentioned in the respective SOP or specified in the protocol.
5.6.4 The Hold time period of the different stages as mentioned below:
- For Starting Material: 30 days / or specified in the respective protocol / BMR.
- Blend: 15 days / or specified in the respective protocol.
- Core Tablet: 45 days / or specified in the respective protocol.
- Coated Tablets: 45 days / or specified in the respective protocol.
- Binder preparation Solution: 5 hours / or specified in the respective protocol.
- Coating Solution: 12 hours / or specified in the respective protocol.
5.6.5 For Oral Hygiene, External Preparations, and Liquid Oral, the in-process material is the bulk product awaiting Filling and packing. The bulk product should be stored in an S.S. container or storage tank, properly closed, and adequately labeled. The bulk product can be stored for a maximum period of 15 days at a temperature of 15 to 25°C or at a temperature and RH specified in the hold time study protocol.
5.6.6 If the hold time of intermediate / Bulk exceeds from established hold/time. Material shall be retested again before use for every further process. The same shall be handled through deviation SOP.
5.6.7 In such cases, starting material/intermediate / Bulk Materials should be tested as per the specification before it is Released for Further Processing. In addition, the sample also will be analyzed for the Above assay and microbiological testing (As applicable).
5.6.8 Any deviation observed during the execution of the hold time study/protocol shall be handled through the deviation SOP.
5.6.9 Any incident / OOS / OOT observed during the analysis is of hold time study shall be handled through the “Handling of Out of Specification” and “Out of Trend Situations” SOP and “Laboratory Incident Reporting”.
5.6.10 Risk Assessment shall be performed if there are any changes in the process, equipment, storage condition, and starting material, which assesses whether further hold time study shall be performed or not.
5.7 Documentation:
5.7.1 The quality assurance officer shall prepare Validation of the Hold time study protocol for different stages as per Annexure-1 (“Template for Hold Time Study protocol”). The numbering of the Hold Time study Protocol shall be given as per the SOP “Preparation, Checking, Approval, Execution, Organizing and Preservation of Validation Documents.”
Hold Time Study protocol should include but not be limited to the following:
- Pre-approval
- Objective
- Scope
- Responsibilities
- Reference Documents
- Products Details
- Storage Condition /Storage Containers
- Procedure
- Sampling Locations Method
- Sampling Plan
- Sample Quantity and Acceptance Criteria
- Deviation Details
- Annexure
- Hold Time Report And Summarization Of Test
- Result
- Recommendations
- Abbreviations
5.7.2 A separate report shall be prepared for Hold Time Study. The Report shall include a Concise description and summary of all studies performed. A detailed result and discussion shall be part of the Report which contains observations and data results obtained during the Hold time study, and the Hold time period shall be summarized in the Report.
A summary of any incident and corresponding root cause, its impact on the study, any unexpected observation (if any), or deviation shall be captured in the Report. A recommendation (if any) should be documented in the Report.
ABBREVIATION:
- °C -Degrees Celsius
- QA -Quality Assurance
- QC -Quality Control
- QS- Quality System
- SOP- Standard Operating Procedure
- SS -Stainless Steel.
- RH- Relative Humidity
- CCF- Change Control From
- WHO -World Health Organization
- OOT- Out of Trend
- OOS- Out of Specification
- EG- Engineering

Naresh Bhakar is the Founder and Author at Pharmaguddu.com, bringing his extensive expertise in the field of pharmaceuticals to readers worldwide. He has experience in Pharma manufacturing and has worked with top Pharmaceuticals. He has rich knowledge and provides valuable insights and data through his articles and content on Pharmaguddu.com. For further inquiries or collaborations, please don’t hesitate to reach out via email at [email protected].