The Standard Operating Procedure (SOP) for the in-process Quality check is applicable to all areas in the production line and packing line at different stages, as described in this SOP. In-process Quality checks are crucial for maintaining product quality and safety at every stage.
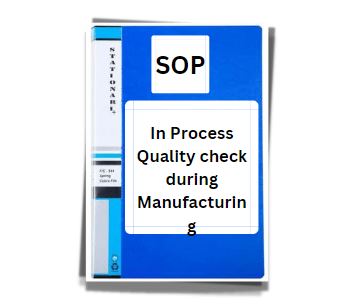
Purpose: SOP for carrying out in-process Quality checks during the manufacturing and packing of products.
Responsibility: The QA Officer is responsible for the overall implementation of this SOP.
Head Quality Assurance is responsible for ensuring overall compliance with this SOP.
Procedure: The QA Officer shall monitor the manufacturing and packing activity on a routine basis.
When the QA Officer enters any area, he/ she shall check the following points:
- Verify the area Status label where the Process is going on.
- Verify the cleanliness of the area and equipment.
- Verify the status label of the equipment.
- Verify whether the activities are carried out following relevant SOPs and instructions in respective BMR and BPR or not.
- Verify Batch record completion up to the last stage.
- Verify practices, including gowning.
- Verify pressure differential, temperature, and Relative humidity to comply.
- Verify quality control status labels where relevant.
- Verify the calibration status of the balances.
Tablet Granulation:
Cheek Moisture Content of Lubricated / Unlubricated Granules:
Procedure :
- Collect the Sample for the Test from three different locations and composite of all to be analyzed.
- Check Moisture Content by Operating Moisture Analysis as per respective SOP.
- Record Observations in the batch record.
Acceptance Criteria:
- Moisture Content should be within the specified limit given in the respective batch manufacturing record.
Tablet Compression:
Monitoring of Environmental Conditions In Tablet Manufacturing Area:
Related: Compression Machine and Tooling
Frequency:
- At the Start of Batch
- Thereafter Every four Hrs. ± 15 Minutes.
Procedure :
- Monitor the Temperature, Relative Humidity, and Pressure Differential and record the same.
Acceptance Criteria: Temperature and Relative Humidity should be within the Specified Limit record in the respective Batch Record.
To Check the appearance of Tablets:
Frequency:
- At the Start of Batch
- After any Maintenance, Break down the Machine.
- After Every Four Hrs. ± 15 minutes. (If the duration of the Process is less than four hours, then the Process shall be done at the start and near the end of the Process).
Procedure:
- Initially collect Tablets from both sides (LHS & RHS) of the Compression Machine at least covering a minimum of one full rotation and thereafter 20 tablets from each side.
- Check the Appearance of the tablet individually and ensure that is free from any Tablet defects.
- Record Observation in the Format as per Annexure I.
Acceptance Criteria:
- The appearance of Tablets should be as per the specification given in the respective Batch Manufacturing Record.
To check the Tablet’s Diameter /Dimension:
Frequency:
- At the Start of Batch
- After Any Maintenance breakdown of the Machine.
Procedure:
- Collect Tablets from the Container of Each Side LHS & RHS) of the Compression Machine.
- Check the Diameter of 5 Tablets from each side (LHS and RHS) by Using Calibrated Vernier Caliper as per the respective SOP.
- Record Observation in the Format as per Annexure.
Acceptance Criteria:
- The diameter of the Tablet should be within the Specified Limit given in the respective Batch Manufacturing Record.
To Check the Tablets Disintegration Test:
Frequency:
- At the start of the Batch After Any Maintenance Breakdown of the Machine
- After Every Four Hrs ±15 minutes (If the duration of the Process is Less than four hours, then the In-process shall be done at the start and near the end of the Process.
Procedure:
- Collect Tablets from the Container of Each Side (LHS and RHS) of the Compression Machine.
- Introduce One Tablet in each of the Six tubes; add a disc to each tube wherever applicable
- Suspend the Assembly in the Beaker.
- Perform the Disintegration Test by Operating the Disintegration Test Apparatus as per the respective SOP.
- Record the Observation in the Format as per Annexure 1.
Acceptance Criteria:
- The Disintegration test is passed if all Six Tablets disintegrate within the Specified Limit given in the Batch Manufacturing Record.
To Check the Tablets Hardness:
Frequency:
- At the Start of Batch
- After Every Four hours ± 15 minutes (If the duration of the Process is less than four hours, then the In-process shall be done at the start and near the end of the Process.)
- After Any Maintenance Breakdown of the Machine.
Procedure:
- Collect 5 Tablets from the Container of Each Side (LHS and RHS) of the Compression Machine.
- Check the Hardness of 5 Tablets collected from each side (LHS & RHS) using a Hardness Tester as per respective SOP.
- Confirm the results with the Specified Limit Given in the Respective Batch Manufacturing Record.
- Record Observation in the Format as per Annexure 1.
Acceptance Criteria:
- The hardness of the Tablets should be within the Specified Limit given in the respective Batch Manufacturing Record.
To Check Tablet Thickness:
Frequency:
- At the start of the batch
- After Every Four Hrs. ± 15 minutes (If the duration of the Process is less than four hours, then the In-process shall be done at the start and near the end of the Process.)
- After Any Maintenance Breakdown of the Machine.
Procedure:
- Initially Collect Tablets from Each Side (LHS & RHS) of the Compression Machine at least covering a Minimum of One Full Rotation and thereafter 20 tablets from each side.
- Check the Thickness of Tablets using a Calibrated Vernier Caliper as per the respective SOP.
- Confirm the results with the specified limit given in the respective Batch Manufacturing Record.
- Record Observation in the Format as per Annexure 1.
Acceptance Criteria:
- The thickness of the Tablets should be within the Specified Limit Given in the Respective Batch Manufacturing Record.
To Check the Tablet’s Friability:
Frequency:
- At the Start of Batch
- After Every Four Hrs. ± 15 minutes (If the duration of the Process is less than four hours, then the in-process shall be done at the start and near the end of the Process.)
- After Any Maintenance Breakdown of the Machine.
Procedure:
- Collect Tablets from each Side (LHS & RHS) of Compression machine
- For Tablets with a unit weight equal to or less than 650 mg, take a sample of whole tablets corresponding as near as possible to 6.5 gm.
- For Tablets with a unit weight of more than 650 mg, take a sample of 10 Tablets.
- Operate the Friability Test Apparatus As per Respective SOP
- Record Observation in the format as per Annexure I.
Acceptance Criteria:
- The friability of Tablets should be within the Specified Limit Given in the Respective Batch Manufacturing Record.
To Check the Average Weight of Tablets:
Frequency:
- At the start of the Batch.
- After Every Four Hrs. ± 15 Minutes. (If the duration of the Process is less than four hours, then the in-process shall be done at the start and near the end of the Process.)
- After Any Maintenance Breakdown of the Machine.
Procedure:
- Collect 20 Tablets from Each Side (LHS & RHS) of the Compression Machine.
- Record Observation in the Format as per Annexure I.
Acceptance Criteria:
- The average Weight of Tablets should be within the specified limit given in the respective Batch Manufacturing Record.
To Check the Uniformity of Weight:
Frequency:
- At the start of the Batch.
- After Every Four Hrs. ± 15 Minutes. (If the duration of the Process is less than four hours, then the in-process shall be done at the start and near the end of the Process)
- After Any Maintenance Breakdown of the Machine.
Procedure:
- Initially Collect Tablets from Each Side (LHS & RHS) of Compression Machine at least covering a Minimum of One Full Rotation and thereafter 20 tablets from each side and check the uniformity of weight.
- Record Observation in the Format as per Annexure 1.
Acceptance Criteria:
- The uniformity of Weight of Tablets should be within the Specified Limit Given in the Respective Batch Manufacturing Record.
Film-Coated Tablets:
Carry out the following In-Process checks Lot wise.
To Check the Average Weight of Tablets:
Frequency:
After Completion of Coating of Each Lot.
Procedure:
- Collect 20 Tablets randomly from the Coating Pan.
- Check the Uniformity of Weight of 20 Tablets; Note the Average Weight.
- Record Observation in the Format as per Annexure-II.
Acceptance Criteria:
- The average Weight of Tablets should be within the specified limit given in the respective Batch Manufacturing Record.
To Check the Tablets Disintegration Time:
Frequency:
After completion of Coating of each Lot.
Procedure:
- Coiled 6 Tablets Randomly from the coating Pan.
- Put One Tablet in each of the six tubes; add a disc to each tube wherever applicable.
- Suspend the Assembly in the Beaker.
- Perform the Disintegration Test of the Tablet by Operating the Disintegration Test Apparatus as per the respective SOP.
- Record the Observation in the Format as per Annexure 11.
Acceptance Criteria:
- The Disintegration test is passed if all six Tablets disintegrate within the specified limit given in Batch Manufacturing Record.
To Check the Tablet’s Uniformity Of Weight:
Frequency:
After Completion of Coating of Each Lot.
Procedure:
- Collect 20 Tablets randomly from the Coating Pan.
- Check the weight of 20 Tablets individually.
- Record Observation in the Format as per Annexure-II.
Acceptance Criteria :
- The uniformity of Weight of Tablets should be within the specified limit given in the respective Batch Manufacturing Record.
To Check the Thickness of Tablets:
Frequency:
After Completion of Coating of Each Lot.
Procedure:
- Collect 10 Tablets Randomly from the Coating Pan.
- Check the Thickness of 10 Tablets individually using a calibrated Vilnier Caliper per Respective SOP.
- Record Observation in the Format as per Annexure-II.
Acceptance Criteria :
- The thickness of the Tablets should be within the specified limit given in the respective Batch Manufacturing Record.
In-process Quality check for Enteric Coated Tablets:
Carry out the following In-process checks Lot Wise.
To Check the Tablet’s Average Weight:
Frequency:
After Completion of Coating of Each Lot.
Procedure:
- Collect 20 Tablets randomly from the Coating pan
- Check the Uniformity of Weight of 20 Tablets and note the Average Weight.
- Record Observation in the Format as per Annexure.
Acceptance Criteria:
The average Weight of Tablets should be within the specified limit given in the respective Batch Manufacturing Record.
To Check Tablets Disintegration Time:
Carry out the in-process Quality check as follows during Disintegration time.
Frequency:
- After completion of Coating of each Lot.
Procedure:
- Collect 6 Tablets randomly from the Coating Pan.
- Introduce One Tablet in each tube of a basket.
- Suspend the Assembly in the Beaker containing 0.1N Hydrochloric Acid.
- Operate the Disintegration Test Apparatus without the addition of a disc for two hours.
- After Two Hours, remove the Assembly from the solution.
- Replace the solution in the Beaker with Mixed Phosphate Buffer pH 6.8.
- Operate the Disintegration Test Apparatus with the addition of disc for One Hour.
- Record Observation Format as per A inexure II.
Acceptance Criteria:
- In 0.1N HCI, No Tablet should show signs of cracks.
- Tablets pass the Test if all tablets have disintegrated within One Hour in buffer solution pH 6.8.
Tablet Packing:
Status Labeling of Area and Equipment:
Frequency:
- At the Start of Batch
Procedure:
- Check the Status labeling of the Area / Equipment and Machine.
- Check the “Cleaned” Status Label Mentioning the Name of the Previous Product., B.No., Type of Cleaning, Cleaned by and Date, Checked By, and Use Before.
Acceptance Criteria:
- Status Labeling of Area/ Equipment and Machine should be as per the respective SOP.
Monitoring of Environmental Conditions of Primary Packing Area:
Frequency:
- At the Start of Batch
- After Every Four Hrs. ± 15 minutes. (if the duration of the Process is less than four hours, then the In-process shall be done at the start and near the end of the Process.)
Procedure:
- Monitor the Temperature, Relative Humidity, and Pressure Differential and record the same.
- Record Observation in the Format as per Annexure-IV.
Acceptance Criteria:
- Temperature, Relative Humidity, and Pressure Differential should be within the specified limit given in the respective Batch Record.
Blister Forming and Counter Sealing Temperature:
Frequency:
- At the Start of Batch
- After Every Four Hrs. ± 15 Minutes. (If the duration of the Process is less than four hours, then the In-process shall be done at the start and near the end of the Process.)
- After Any Breakdown and Maintenance of the Machine.
Procedure:
- Check the blister Forming and counter sealing Roller temperature shown in PLC in the blister machine.
- Record the observation in the format as per annexure iv.
Acceptance Criteria:
- Blister Forming and counter sealing Roller temperature Shall be within the specified limits, as given in the respective batch packing record.
Printed Aluminum Foil Checking:
Frequency:
- At the Start of Batch
- After Every Four Hrs. ± 15 minutes. (if the duration of the Process is less than four hours, then the In-process shall be done at the start and near the end of the Process.)
- After Any Maintenance and Breakdown of the Machine.
Procedure:
- Check the Artwork Code of the aluminum foil.
- Check the Visibility of Text Matter.
- Check the Mfg. License No. and Overprint Details.
- Record Observation in the Format as per Annexure lV.
Acceptance Criteria:
- Overprint details and Text Matter of the Aluminum foil should be as per respective Batch Packing records.
To Check the Leak Test:
Frequency:
- At the Start of Batch
- After Every Four Hrs. ± 15 Minutes. (If the duration of the Process Is less than four hours, then the In-process shall be done at the start and near the end of the Process.)
- After any Breakdown and Maintenance of the Machine.
Procedure:
- Collect a sample of blister/strips in such a way that it should cover all the pockets of the sealing Roller and sealing plates during the Leak Test
- Operate the Leak Test Apparatus as Per Respective SOP.
- Record Observation in the given Format as per Annexure-IV.
Acceptance Criteria:
- Blisters/strips should be subject to without any leakage.
In-process check for Carton Checking:
Frequency:
- At the Start of Batch
- After Every Four hours ±15 Minutes, (If the duration of the Process is less than four hours, then the in-process shall be done at the start and near the end of the Process.)
Procedure:
- Check the Artwork code on the Carton.
- Check the Overprinting Details on the Carton.
- Check the Carton to ensure the proper Pasting/Locking.
- Check Number of blisters/ Strips in the Carton.
- Record Observation in the Format as per Annexure.
Acceptance Criteria:
- Cartons should be packed with defects-free Blister / Strip.
- The number of Blister /Strip in a carton should be as per the quantity mentioned in the respective Batch Packing Record.
In-process for Label Checking:
Frequency:
- At the Start of Batch
- After Every Four Hours ± 15 minutes. (if the duration of the Process is less than four hours, then the In-process shall be done at the start and near the end of the Process.)
Procedure:
- Check the labels on the containers for the correctness of overprinting batch details.
- Check for the sticking of the labels on the containers.
- Check the alignment of labels on containers.
Acceptance Criteria:
- Overprinting batch details on the label must be correct. Sticking and appointment of labels must be appropriate.
In-process checks for Leaflets:
Frequency:
- At the Start of Batch
- After Every Four Hrs. + 15 Minutes. (If the duration of the Process is less than four hours, then the In-process shall be done at the start and near the end of the Process.)
Procedure:
- Check the Artwork Code of a leaflet.
- Check the printing of text Matter.
- Check the Presence of a Leaflet in a Carton.
Acceptance Criteria:
- The artwork code should be as per the approved BPR, and the text matter should be legible.
Pack Stock Verification:
Frequency:
- After Every Two Hrs. ± 15 minutes.
Procedure:
- Check the cartons/blisters/Strips in the shipper.
- Record the observations in Format Annexure VI.
Acceptance Criteria:
- No defects should be observed during pack stock verification.
Bulk Packing of Tablets:
Frequency:
- At the Start of Batch
- After Every Four Hrs. ± 15 minutes. (If the duration of the Process is less than four hours, then the In-process shall be done at the start and near the end of the Process.)
Procedure:
- Check the weight and number of tablets per container.
- Check the sealing of the Polybag in the HDPE container.
- Check for the presence of a Leaflet (if applicable) in the HDPE container.
- Check the Sealing of the Aluminum Tagger (if applicable) on the HDPE container.
- Record Observation in the Format as per Annexure V.
Acceptance Criteria:
- The number of tablets should be as per the respective BPR. The sealing of the Polybags in the HDPE container should be appropriate. Leaflets (if applicable) in each HDPE container must be present. The sealing of the Aluminium Tagger on the HDPE container (if applicable) should be perfect.
- Suppose it is observed that the result of any in-process Quality check is out of the specified limit. Then hold the affected drums/containers packed between the last satisfactory Test and the current unsatisfactory Test and initiate a deviation as per SOP “Handling of Deviation” followed by necessary corrective action.
Abbreviations:
- Annex.- Annexure
- pg. – Page
- LHS. – Left-Hand side
- RHS.- Right-Hand Side
- ML.No.- Manufacturing License Number
- MRP.- Maximum Retail Price

Naresh Bhakar is the Founder and Author at Pharmaguddu.com, bringing his extensive expertise in the field of pharmaceuticals to readers worldwide. He has experience in Pharma manufacturing and has worked with top Pharmaceuticals. He has rich knowledge and provides valuable insights and data through his articles and content on Pharmaguddu.com. For further inquiries or collaborations, please don’t hesitate to reach out via email at [email protected].