Capsules are solid dosage forms in which medicine or a combination of drugs, with or without excipients, is enclosed in Hard Gelatin Capsule Shells, soft, soluble gelatin shells, or hard or soft shells of any other acceptable material, in a variety of shapes and capacities. Normally, they are meant for oral consumption and contain a single dose of active ingredient(s). But capsules must be free from manufacturing defects during the manufacturing process. During manufacturing, capsules may get different types of defects that can be identified at the same time. Capsule Defects and Remedies are provided below to remove such types of defects.
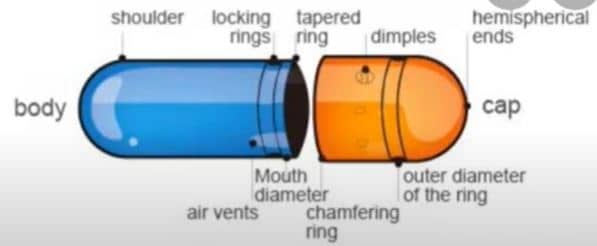
Types of Capsule Defects and Remedies:
- Loss of cap during transfer / Misalignment of cap and body bush
- Dents and pinholes (on tips)
- Cracks in Capsules
- Telescopic Capsules
- Dusty Capsules
- Empty Capsules
- Damaged band
- The capsule does not enter the rectifier block
- Capsule getting damaged during loading
- Capsule non-separation
- Target weight not achieved
- Weight variation
- Capsule lock length variation
Details of Capsule filling Problems and Solutions are Provided Below in this entire article.
1. Loss of cap during transfer / Misalignment of cap and body bush
Causes: High vacuum
Remedies: Reduce vacuum but make sure that it is not so low that capsule separation is not observed
Kindly check the alignment of the cap and body bush visually to remove the Misalignment of the
2. Dents and pinholes (on tips)
Causes: Excess closing/lock length setting during the encapsulation process, excessive lock length, excessive closing pressure, over-filling of capsules, incorrect pin size or pin configuration, and improper storage conditions (moisture).
Remedies: Ensure the correct size disc is used and also ensure the correct amount of dose is filled in the capsule
3. Cracks in Capsules
Causes
1. Improper (storage) conditions favor the transfer of moisture from the capsule shell to encapsulated components.
2. Misalignment of the upper and lower capsule segments incorrect setting of the cap hold-down pin in the joining station.
Remedies 1. Store the capsule properly
2. Make a Proper setting of the station.
4. Telescopic Capsules
Causes
1. Misalignment of cap and body bush
2. Closing pin not in the center of body bushes
3. Damage the rubber sheet of the closing plate
Remedies
1. Align cap/body bush to bush gauge.
2. Check pin straightness using a gauge pin If bent replaces it with a new one.
3. Wear of capsule closing units rubber sheet specifically at the point where the capsule strikes the sheet would lead to telescopic. Replace if required
5. Dusty Capsules:
Causes
1. Filling dusty fill.
Remedies: 1. Use capsule polisher
6. Empty Capsules
Causes
1. Malfunction in capsule filling machine which is preventing empty capsules from reaching exit chute (e.g. load cells, capacitive sensors, etc.).
Remedies
1. Make the sure presence of safeguards in the capsule filling machine which is preventing empty or under-filled capsules from reaching the exit chute (e.g. load cells, capacitive sensors, etc.).
7. Damaged band
Causes
1. Badly tuned banding process, such as improper wheel height and speed, improper processing temperature, improper band thickness, and poor/bad band wheel.
Remedies
1. Set all the parameters accurately.
8. Capsule does not enter the rectifier block
Causes
1. Capsule stored overnight and without climatic control.
2. Magazine non-alignment with rectifier block
Remedies
1. This may be due to improper room conditions or the capsules having been affected by improper storage conditions. In this case, some of the capsules stick to each other preventing them to be transferred to the magazine slots.
2. Magazine alignment with the rectifier block could have shifted or not been set right. Align to the rectifier block using a gauge.
Read Also: Tablets Manufacturing Defects and remedies
9. Capsule getting damaged during loading
Cause
1. Misalignment of rectifier block with bushes
Remedies
1 Verify visually if the rectifier block is in alignment with the cap/body bush. Use alignment gauge if any doubt.
10. Capsule non-separation
Causes 1. Insufficient vacuum or incorrect vacuum pump
2. Leakage through filters
3. Cap body bush misalignment
4. Worn out bushes
5. Loss of spring tension at the top slide
Remedies
1. Proper capacity pump.
2. In case of vacuum drops kindly check the filters on the vacuum pump. Cleaned and/or replace it if required
3. A misalignment of cap and body bush can cause non-separation.
4. If non-separation occurs in specific bushes and cleaning does not help, replace these bushes with a new one.
5. Poor spring tension at the top side or sluggish movement of the top slide probably caused by pin results in improper closing of cap/body bush holder plate. Replace it
11. Target weight not achieved
Causes
1. Incorrect target weight with respect to selected capsule size
2. Improper slug formation due to incorrect setting parameters
3. Insufficient binding selected capsule size
4. Poor flow of product
Remedies
1. Check for the variation in physical parameters (Tapped density, moisture content, particle size distribution & Flow
2. Check for correct parameters setting
3. If a proper slug is not formed, part of the powder could be lost before delivery to the capsule
4. Poor flow of the powder in the dosing disc will result in insufficient powder flowing in the disc cavity properties of the formulation )
12. Weight variation
Causes
- Wrong selection of dosing disc thickness
- Incorrect gap between
- dosing disc and supporting pad
- Tamping pin and body bush
- Dosing disc and wiper block
- Dosing disc and body bush
Remedies:
- Kindly select the proper dosing disc for filling of powder fully onto the capsule shell
- Correct the Gap Between:
- dosing disc and supporting pad: NMT 0.1 mm
- Tamping pin and body bush: maintained at 0.2 to 0.4 mm
- Dosing disc and wiper block: NMT 0.1 mm
- Dosing disc and body bush: maintained at 0.8 to 1.0 mm
13. Capsule lock length variation
Causes
Remedies
1. Excess joined length
2. Improper setting of the closing plate
3. Damage the rubber sheet of the closing plate
4. Incorrect setting of the closing plate
Remedies:
1. Check for the standard locking length
2. Check for the gap between the closing unit rubber sheet and capsules. The distance between the two points should be between 0.5 and 0.8 mm.
3. Wear off of capsule closing unit rubber sheet, especially at the point where capsule strikes the sheet would lead to this problem. Replace it with a new one.
4. The flap should be visually parallel to the cap bush lock plate. Check to ensure that capsules are hitting the center of the rubber sheet and not the edge. If this were the case, the capsule would fall off the edge and fail to lock properly.
Other Common Capsule Defects and Remedies:
Deliquescent / Hygroscopic powders- Adsorbent [magnesium carbonate, heavy / light magnesium oxide]
A small dose of drug Remedy-Addition of inert powder.
Incompatibilities of materials -Use of two capsules – small in large
Lack of adhesiveness difficult to fill by punch method-Moistened with alcohol, granules reduced to powders.
Other inquiries Related to Capsule filling Problems:
Problems in capsule filling and remedies pdf
Capsules defects and remedies
Capsule defects and remedies
Capsules defects
Capsule defects with images
Telescoping capsule defect
Which of the following is not the defects of hard gelatin capsule shells

Naresh Bhakar is the Founder and Author at Pharmaguddu.com, bringing his extensive expertise in the field of pharmaceuticals to readers worldwide. He has experience in Pharma manufacturing and has worked with top Pharmaceuticals. He has rich knowledge and provides valuable insights and data through his articles and content on Pharmaguddu.com. For further inquiries or collaborations, please don’t hesitate to reach out via email at [email protected].