Differential pressure in pharmaceuticals helps to prevent contamination and cross-contamination. A Magnehelic gauge device is used to measure the pressure difference between the two adjacent sections. The gauge has two inlets point for the pressure that is connected to the area being monitored.
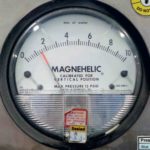
Differential pressure is the pressure that differentiates between the pressure of the atmosphere of one area(process area) to other surrounding areas(corridors). It is measured in pascals and wc of Hg. Magnehelic gauge is used to records the differential pressure.
Why is Differential Pressure important in Pharmaceuticals?
Differential pressure prevents contamination and cross-contamination during the product manufacturing process; during the process, the air becomes contaminated. If Differential pressure is not maintained within limits, the contaminated particles may enter or mix up with the fresh air and contaminate other manufacturing products.
Differential pressure must be checked and recorded every two Hours ± 15 minutes in the manufacturing area where the product is directly exposed, and every Four Hours ± 15 minutes where the product is directly not exposed or as per the given SOP “Records of area Differential Pressure.”
WHO guidelines on Differential pressure
According to the WHO Guidelines Annex 8, the airflow flow should be from a clean area to a cubicle area to avoid contamination. The processing area should be negative( in the case of OSD )compared to the corridor area to ensure airflow from the aseptic area to the non-aseptic area.
Generally, dust is generated in the process area, so the corridor should be at higher pressure to stop dust flow in the corridor area.
Importance of the airlock in Differential Pressure
Airlock in pharmaceuticals is used to transfer the materials. It is advised to keep positive pressure in the corridor rather than the processing or manufacturing area. The positive airlock should be there to minimize direct airflow from process air to the Non-Process area, which helps control the direct contamination in the processing area.
Airflow Direction in the Non-sterile Area with Respect to Corridor
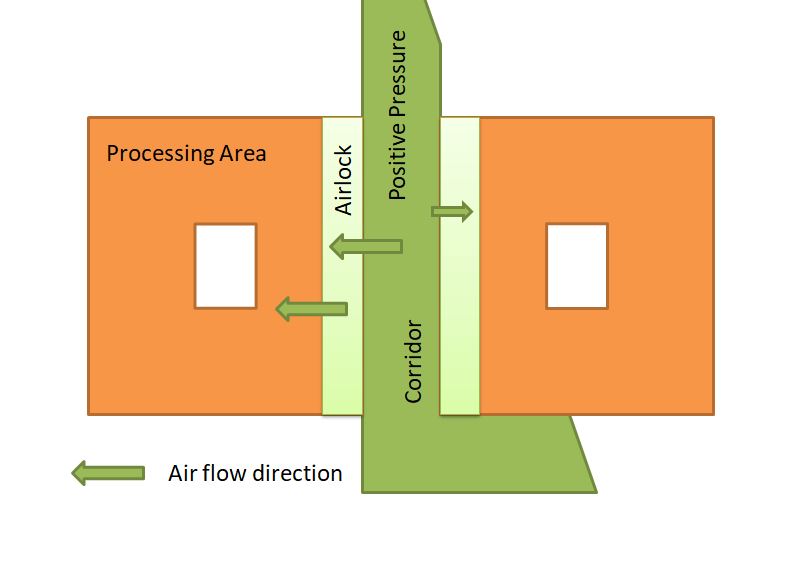
keep negative pressure inside the controlled area(process area) as compared to the corridor area(positive pressure) to prevent cross-contamination.
Negative pressure means clean airflow from the corridor going into the process room, and contaminated air in the process area flows out from the riser’s filters. These types of air systems are suitable for OSD (oral solid dosage), steroids, and chemotherapy products.
Differential Pressure in a Sterile area with respect to Corridor
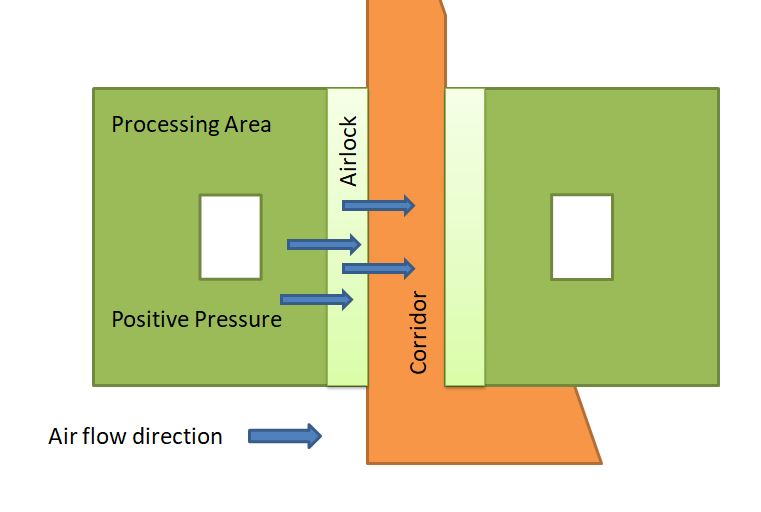
Cross-contamination of one product with the other products is an issue, but in a sterile area (injection filling), there are more chances of microbial contamination; that’s the reason positive pressure is maintained inside the sterile area as compared to the corridor.
Way to maintain Pressure in Area
Recovery Test for HVAC
It’s important to perform a recovery test as per the scheduled time to check the pressure differential in pharmaceuticals produced by the HVAC system. The calibration of the Magnehelic gauge must be checked regularly.
Building construction:
To take care of the integrity of the unit, airtight doors, a Gap between the door and floor, and window installation are required to stop the loss of pressure through the gap. An alarm for a sign should be available for workers to understand any loss of atmospheric pressure.
Summary
In the pharmaceutical industry, maintaining differential pressure is important to prevent contamination and cross-contamination during the manufacturing process. A Magnehelic gauge measures the pressure difference between the process area and surrounding spaces. This pressure is measured in pascals and wc of Hg, and it must be monitored regularly.
Failure to control differential pressure may allow contaminated particles to mix with fresh air. WHO guidelines highlight maintaining airflow from clean to less clean areas. So for that Airlocks play a vital role, keeping positive pressure in corridors to prevent direct contamination in processing areas.
For non-sterile areas, negative pressure in the process room ensures clean airflow from the corridor, suitable for OSD and other products. In sterile areas, positive pressure protection against microbial contamination. Regular recovery tests and HVAC system checks, along with airtight construction, are essential to maintain pressure integrity in the pharmaceuticals area.
Important FAQs
Ans: 10-15 pascal
Ans: It is measured in Pascal and wc of Hg
Ans: Hg refers to Mercury
Ans: Positive pressure
Ans: Negative pressure

Naresh Bhakar is the Founder and Author at Pharmaguddu.com, bringing his extensive expertise in the field of pharmaceuticals to readers worldwide. He has experience in Pharma manufacturing and has worked with top Pharmaceuticals. He has rich knowledge and provides valuable insights and data through his articles and content on Pharmaguddu.com. For further inquiries or collaborations, please don’t hesitate to reach out via email at [email protected].