Air is one of the major sources of contamination for pharmaceutical products. That is why the design, monitoring, and maintenance of the AHU (Air Handling Unit) are essential to increase its efficiency and capacity as per GMP (Good Manufacturing Practices). Important tips are given here to follow good practices for an Air Handling Unit.
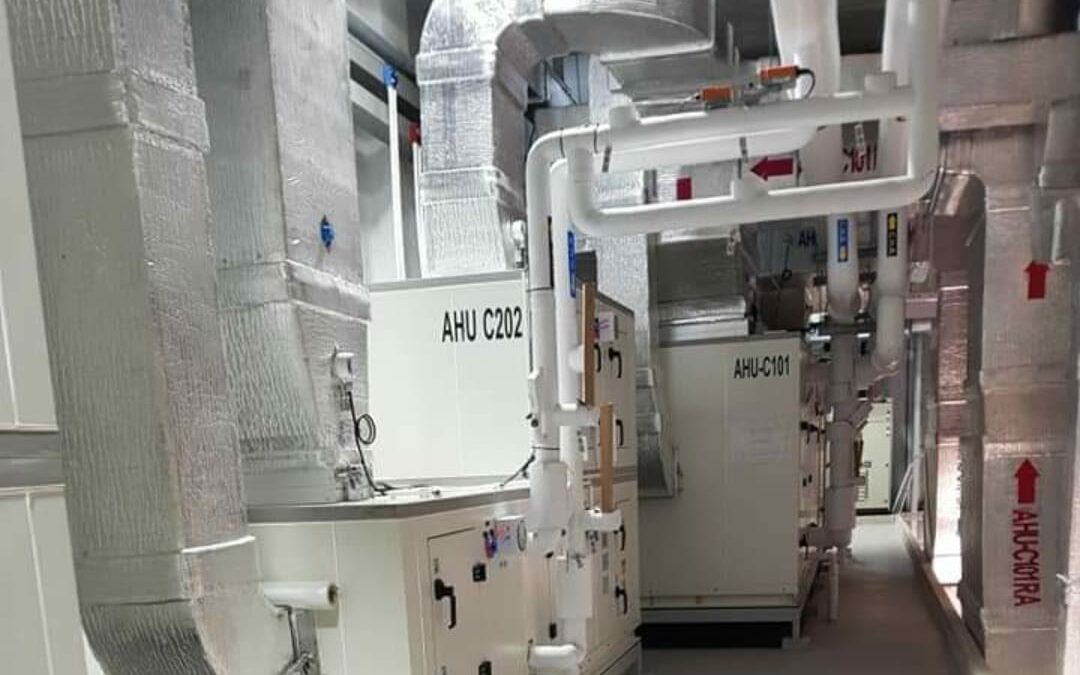
Tips for Good Practices of Air Handling Unit (AHU):
- AHU system should be designed as per requirement in new schedule ‘M’ or such other guidelines.
- Installation of window A/C without any air filtration and pressure design is not satisfactory.
- AHU should be fabricated and installed according to design qualification, and its record should be kept available.
- AHU system should be located in a proper, and clean place, and the space should be adequate for cleaning and maintenance.
- Proper size filters should be fitted in AHU to supply the air quality of the desired class. Separate AHU for different areas.
- Temperature humidity controls should be PLC-based and fully atomized. An alarm system in out-of-specification condition shall be installed.
- The material for the construction of AHU should be easily cleanable and not generate any type of contamination.
- The design of AHU should be easily cleanable.
- Return air ducts should have adequate filters, especially in dusty areas, such as tablets, powder, capsules, etc.
- Before the system is utilized for the production area, it should be validated, and validation, (DQ, IQ, OQ, PQ) with SOP should be documented.
- Training should be given to personnel for good practices for the Air handling unit, and records should be maintained.
- SOP should be correctly written, followed, and displayed near to AHU.
- Periodical cleaning, preventive maintenance, and validation should be done, and records should be maintained.
- AHU systems for parenteral and other formulations should be designed by considering the proper pressure to differentiate, airflow patterns from cleaner to dirtier, Air changes, heat load, and occupancy.
- Fabrication quality of AHU and duct, pipelines should be good with no leakage, and Properly installed wherever required.
- Systematic drawing, with the type of duct, diffuser, grills, dust size, elbow, and branching should be available.
- AHU system should give desired air quality.
- Manometers should be installed to indicate the room inside pressure.
- AHU filters in critical, non-sterile areas should be installed at the terminals, for any class filters should be fitted at the terminals.
- Air velocity records should be kept.
- Filters should be installed properly with proper gaskets to avoid leakages.
- Dust from production through exhaust should not be let into the atmosphere.
- Filter cleaning and preventive maintenance record should be maintained.
- Diffusers, grills, and risers should be cleaned frequently in the powdery operation area,
- AHU should be ‘ON’ whenever production is going on.
- Start-up, a time to achieve the desired air quality class, should be established and recorded.
- AHU should be installed in the shed and not in an open space.
- Fire and safety instruments should be fitted to the AHU system.
- Temperature, Humidity, pressure, and air velocity measuring instruments shall be made available.
- Out-of-specification should be recorded (if Applicable).
- Pressure drop across the filter should be maintained and recorded for filter integrity.
- Air supply should be adequate in all airlocks.
- Working ranges should be marked in green on manometers also mark the green and red zone on the monometer.
- AHU’s surrounding area should be clean.
- AHU and Area shall be disinfected when there is a longer gap between production activity.
Validation steps as per the sequence:
- Test equipment calibration and certification.
- Equipment on AHU calibration.
- Utility verification.
- Documentation logs.
- Control parameter.
- Alarm testing HEPA filter integrity testing.
- HEPA filter airflow velocity.
- Air changes per hour.
- Smoke studies room, pressurization test.
- Qualification of temp and humidity test.
- Nonviable and viable microbial counts for a logical time period.

Naresh Bhakar is the Founder and Author at Pharmaguddu.com, bringing his extensive expertise in the field of pharmaceuticals to readers worldwide. He has experience in Pharma manufacturing and has worked with top Pharmaceuticals. He has rich knowledge and provides valuable insights and data through his articles and content on Pharmaguddu.com. For further inquiries or collaborations, please don’t hesitate to reach out via email at [email protected].