Validation is the established document evidence or proof that provides a high degree of assurance. A particular method can systematically produce a product that meets its predetermined specifications and quality attributes. Process validation is also a component of the validation, which is explained below.
Introduction to Pharmaceutical Validation:
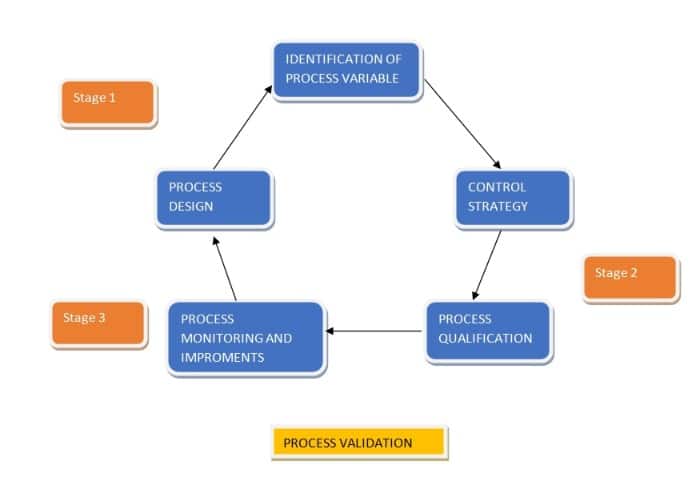
- Validation is a concept that has evolved continuously since its first informal appearance in the United States in 1978.
- However, concepts of validation were first introduced by Ted Byers and Bud Loftus in the middle 1970s to enhance the standard of prescribed drugs.
- The first validation activities targeted the processes concerned with creating these products; however, they quickly unfolded to associated processes and environmental management, media fill, equipment sanitizing, and pure water production.
- As per guidelines, validation is an act of demonstrating and documenting any Procedure, Process, and activity that can systematically cause the expected results.
- It includes the qualification of systems and equipment. The goal of the validation is to confirm that quality is maintained at every step and not simply tested at the last stage, as per the validation process.
The Importance of Validation in Pharmaceutical
Validation plays an essential role in pharmaceuticals as follows:
Quality assurance: In daily routine, product quality can not be assured by testing because of the limitation of sample availability and finished product testing.
For Cost reduction: Due to the streamlined validation process, there’s a reduction in the number of sampling and testing procedures. This leads to fewer product rejections and retesting, resulting in cost savings.
Compliance: Validation is essential according to cGMP compliance.
Responsible Departments for Validation
- Site validation committee: To develop a site master plan with preparation, execution, and studies of the master plan.
- Manufacturing departments: For the preparation of a batch.
- Quality assurance: To approve the protocol, documentation procedure, report, and compliances.
- Quality control: For testing according to protocol and generating reports.
The Responsible Authority for validation execution
- Head of Quality assurance
- Head of Quality control
- Head of a Production
- Head of Validation
Types of Pharmaceutical Validations
Different types of validations in pharmaceuticals are:
- Process validation
- Equipment validation
- Facilities validation
- HVAC system validation
- Cleaning validation
- Analytical method validation
- Computer system validation
What is Process Validation?
Process validation is the analysis of data collected throughout the design and manufacturing of products to ensure the process is consistently produced as per the given standard.
Process Validation is a demand of current (GMPs) for finished pharma products as per CFR (21CFR 211), and GMP rules for medical devices as per CFR (21 CFR 820) and so it applies to the manufacturers of each drug product and medical device.
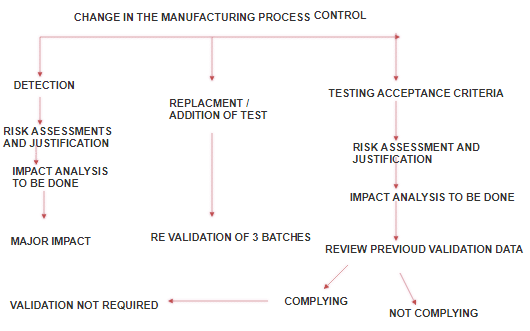
The aim of validating the process is to make sure we get high-quality products that remain consistent. Regulatory authorities like EMA and FDA have published guidelines that link to process validation.
According to the Food and Drug Administration, product quality assurance comes from careful and general attention to various factors. This includes picking good-quality materials, having a well-designed process and method, and keeping an eye on the process through tests during and at the end.
FDA Guidelines Describe the Process Validation into three stages:
Process Design: Process design is the collection of data from the development stage to analyze the commercial manufacturing process. The collected information is used to analyze the established benchmark for quality and production control.
Process Qualification: Process Qualification is designed to find a result of the process that can determine the capability to reproduce commercial manufacturing output. During this process, all critical quality parameter is taken into account to ensure product quality.
Continued Process Verification: It is an ongoing monitoring process that ensures all production stages are under control.
Types of Process Validation?
Types of Process Validation depend on the at what time validation is performed relative to production; validation can be classified into four types:
- Prospective validation
- concurrent validation
- Retrospective validation
- Revalidation
1. Prospective validation: (Premarket Validation)
Prospective validation is carried out during the development stage (Also called premarket validation). The results of prospective validation help in identifying the risk factors in the production process. This process is broken down into various steps to analyze crucial points during product manufacturing, like mixing time, relative humidity (RH), and temperature.
Process validation is carried out for the manufacturing process when;
- Introduction of New Products in the manufacturing facility.
- If there is a significant change in the manufacturing process and the impact of the changes, e.g., leak test failed due to sealing problems in blister.
- The validation will include at least the first three consecutive production scale batches after the process stabilizes.
Criteria for Prospective Validation?
- Three prospective validation batches should have the same parameters.
- Process parameters shall be identical for these three batches.
- The first batch shall be dispatched after the completion of the third batch of manufacturing, testing, and review of results.
If there are any needed changes in the manufacturing process after the first batch, then follow these criteria:
- Take three batches with revised parameters and do not consider the first batch for this validation.
- Consider the 2nd, 3rd, and 4th batches as prospective validation batches, which have identical parameters.
- A change shall be made through the proper change control system.
- The first validation batch shall be released for sale and distribution after manufacturing, testing, and review of all three batches.
- The results of all three batches shall be within acceptable limits.
2. Concurrent Validation:
Concurrent validation is carried out during the regular production stage. It is based on a complete studying the process through prospective validation.
The first three production scale batches must be monitored as carefully as possible.
Concurrent validation is carried out when:
- A new product has been prospectively validated in a manufacturing facility.
- There is no change in the manufacturing process, and the impact of change in the manufacturing process is not significant.
- If there is a change in the supplier of raw materials in the existing production formula.
Examples of in-process testing are:
- pH Value
- Tablet Hardness
- Weight Variation
- Dissolution Time
- Content Uniformity
- Viscosity or Density
- Color uniformity
- Particle Size Distribution
- Average Unit Potency
FDA Position On Concurrent Validation:
FDA rejected Concurrent validation because pharmaceutical organizations do not provide sufficient data to show where the variability in the mixing process comes from and how it is controlled., therefor use of concurrent validation is inappropriate and FDA goes on to state that concurrent validation should only be used rarely.
Source: GMP compleience org
3. Retrospective validation:
Retrospective Validation is based on historical and testing data of previously manufactured batches. It includes the analysis of trends compiled and checks whether the process is within the allowed range of process parameters. This can be done using computer-based data or manual methods.
Retrospective Validation is carried out when:
- Collect data from previously completed batches.
- Organize all data sequences wise, i.e., batch manufacturing and expiry date.
- Use 10 to 25 batches or more for this purpose, preferably processed within 12 months and reviewed collectively.
- A Batch rejected during routine quality control is not included in this review.
4. Revalidation:
Revalidation is required to make sure that any changes made in the process environment, whether done intentionally or unintentionally, do not adversely affect the process characteristics and product quality.
Revalidation is needed when:
- After any change having a bearing on product quality.
- Periodical Revalidation.
- Change in Batch size.
- Change in facility and plant.
VALIDATION V/S QUALIFICATION
Validation is Related to the Process
Qualification related to system/Equipment.
Eg. For validation for the sterilization process, the autoclave must be qualified.
Validation Master Plan (VMP):
The validation master plan must be summarized before describing the whole thing in projects. These are the following points to be included in a protocol that is followed by all pharmaceutical industries.
- Introduction
- Methodology
- Qualifications (IQ, OQ, PQ)
- Personnel
- Schedules
- Preventive maintenance
- Change control
- Procedure
- Documentation
- Appendix
VMP Should state who is responsible for the validation:
- Preparation of VMP
- The protocol and SOPs
- Validation work
- Report and documentation and its control
- Approval and authorization of validation protocol
- Report on all stages of the validation process
- Tracking system
- The need for training in support of validation
Validation master plan, the following are the points to be considered during the preparation of the validation protocol:
Validation Protocol:
The following are the contents required for the validation protocol:
- General information
- Objective
- Background/Prevalidation activities details of development and technique transfer (from R&D or another site) activities to justify in-process testing and controls; any previous validations.
- List of equipment and their qualification status
- Facilities qualification
- Process flow chart
- Manufacturing procedure narrative
- List of critical processing parameters and critical excipients
- Sampling, tests, and specifications
- Acceptance criteria
Nowadays, software tool validation is also an essential aspect of the validation process.
Today’s medical device regulations concentrate on managing software tools, and there are dozens of applications for accounting tools to email tools.
The first step of any scenario is to assess the software tool for its impact on medical devices. If it will affect the “quality of the device,” then validation is also needed.
Consider that the software tool needs to manage the quality system including CAPAs, complaints, NCs, requirements, and risks that come under this category.
This is all well and good if you have insight and knowledge into the object you are validating. However, in most cases, especially for the off-the-shelf software tools, the user sees them only as black boxes.
Setting up a comprehensive validation for a software tool without knowing its internal mechanism is a challenging task; not much for what you know, instead of for what you do not.
It is challenging to develop tests for unknown boundaries and unclear algorithms. Moreover, generally, this ends up in vital gaps within the validation coverage.
Recently, computer code tool-developing corporations have started providing pre-validated computer code and validation packages for the medical device market.
The device is a priceless product for the manufacturer. It allows to demonstrate compliance using the expertise and knowledge of the developer(s); due to their knowledge of the internal processes of the tool, they can put together a relatively lean protocol that adequately challenges the product.
Caution: it is best practice (if not expected by regulatory bodies) to repeat at least part of the validation protocol in-house to confirm the results of the pre-validation provided by the developer. It is unlikely that you will be able to adequately control your software tool providers (read: audit them) to rely on their internal activities solely.
This article covers the following questions asked by interviewers:
- Types of validation in pharmaceuticals?
- What are process validation and its types in pharmaceuticals?
- Why is process validation required?
- Validation of master protocol contents in pharmaceuticals
- How do validate the process?
- What is the software tool validation?
References:
Current FDA guidelines on Process validation
Related Topics:
- Responsibilities of the Validation Team to Meet the cGMP Compliance
- Cleaning Validation Protocol for Pharmaceutical Equipment
- Fundamentals of Validation SOP
- Facility Upgrade Master Validation Plan
- Protocol on Hold Time Study of Machine Parts
- Difference between Validation, Calibration, and Qualification in Pharma
- Water System Validation and Phases

Naresh Bhakar is the Founder and Author at Pharmaguddu.com, bringing his extensive expertise in the field of pharmaceuticals to readers worldwide. He has experience in Pharma manufacturing and has worked with top Pharmaceuticals. He has rich knowledge and provides valuable insights and data through his articles and content on Pharmaguddu.com. For further inquiries or collaborations, please don’t hesitate to reach out via email at [email protected].
Is there any frequency for periodical revalidation in guide lines?
No, there are no such Guidelines for this.but you have to add it (time Frame) in periodic revalidation in protocol with proper justification.