A colloidal mill is used to break down a mixture that contains Suspended solid particles to make a homogeneous mixture. So it is used in a wide range of pharmaceuticals and other industries to make a suspension.
Working Principle of Colloidal Mill:
The colloidal mill works on Shearing by using a rotor/ stator.
By using shearing force its breakdown the mixture by dispersion in liquid form.
Parts of Colloidal mill:
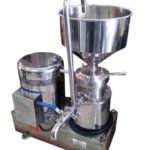
- To feed the material hopper is used, which is attached to the rotor and Stator assembly.
- Rotors and Stators, which are made of stainless steel, it may be rough, or finished surfaces used for Shearing the mixture.
- Motor assembly to rotate.
- A discharge point for outlets the mixture.
Related: RotaMeter Principle, Working, Construction, and Types
Colloidal mill Working/ mechanism:
The liquid containing Solid particles is put into the hopper. A suspension or liquid passes through the moving part (Rotor) and Non-Moving (Stator), which causes a high shearing force between the two narrow gaps.
Shear stress force can be reduced or increased by changing the gap (50 to 1000 mm) and by changing rotor speed( 1000 to 25000 rpm), but in most cases, the speed is (2000 to 18000 rpm).
The liquid mixture continuously flows through these two parts and makes it homogeneous, then finally drains out through the outlet.
Pharmaceutical use of Colloidal mill:
- It is used for the formation of Homogeneous mixtures, suspensions, and emulsions in pharmaceuticals, especially for tablet coating solutions.
- Its capabilities to produce a high suspension by reduced Particle size up to 3 microns.
- It can be used for making ointments, suspension, and emulsion, and fiber materials can be milled by the use of rough surfaces.
- It is used for making sterile Drug products.
Others usage:
- It can be used in the liquid-to-latex emulsion processes.
- Used in cosmetic (soap, toothpaste, butter, fish oil), food, paint, and textile industries
Advantages:
- The noise level is moderate.
- High efficiency to get more output
- Easy to operation
- Easy to clean
- High-grade MOC
- It can be used for high-viscosity range products.
- It required low space for installation.
- Less tear and wearing problems.
- It can be used for high and low-scale production.
Related: Fluid Energy Mill; Working, Principle, and Construction
Disadvantages:
- Use high energy power.
- Not suitable for solid and semi-solid products
- Wear problems in the case of Rotor and Stator.
Conclusion:
Colloidal mill is highly recommended in the Pharmaceutical, beverage, paint, textiles, and food processing industries. It can produce high output in less time, is easy to Operate, and Clean.
Related: Fluidized bed dryer (FBD): Principle
Reference:
- David, B. Troy, and Paul, Beringer (2006). Remington: The Science and of Pharmacy. 21st edition. Lippincott Williams and Wilkins, USA.
- Handbook for Pharmaceutical Pharmapathway edition 2016 by Dr. D.A. Savant.

Naresh Bhakar is the Founder and Author at Pharmaguddu.com, bringing his extensive expertise in the field of pharmaceuticals to readers worldwide. He has experience in Pharma manufacturing and has worked with top Pharmaceuticals. He has rich knowledge and provides valuable insights and data through his articles and content on Pharmaguddu.com. For further inquiries or collaborations, please don’t hesitate to reach out via email at [email protected].