There is often confusion surrounding the terms validation, calibration, and qualification within the pharmaceutical industry. Let’s explore their differences with explanatory examples.
Difference among Validation, Calibration, and Qualification
1. Qualification:
Qualification is the process of planning, conducting, and documenting test results performed on equipment to confirm its operational capability. It demonstrates that the equipment will function consistently as intended and meet predefined acceptance criteria outlined in the supplier’s recommendation, Design qualification specification, and guidelines.
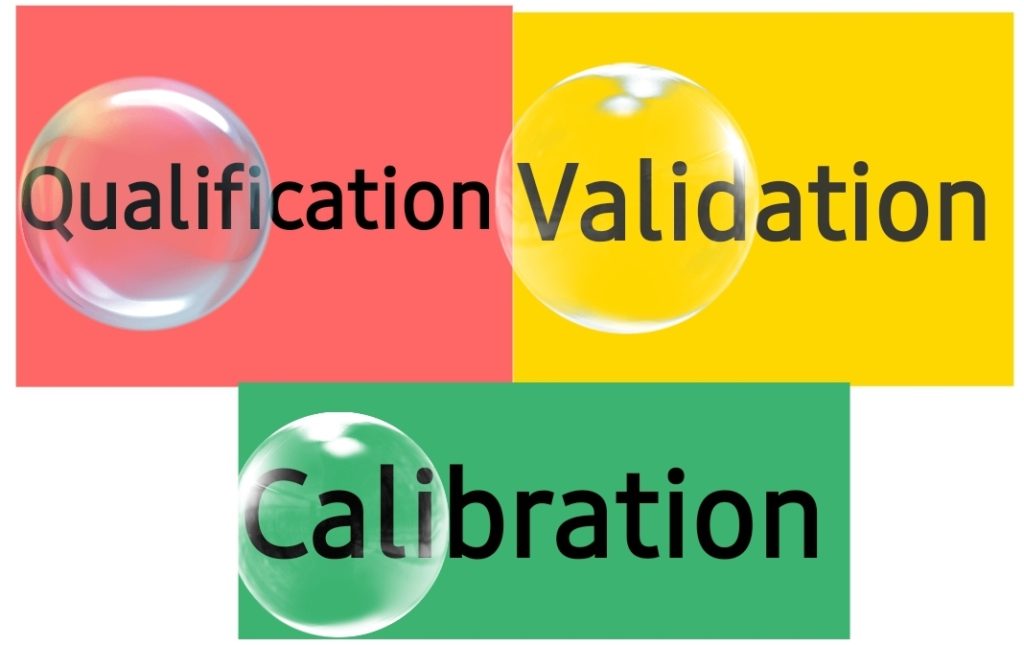
Qualification should be performed on related equipment, instruments, facilities, and areas before their use. The qualification process involves various stages such as user requirement specification (URS), factory acceptance test (FAT), Site acceptance test (SAT), design qualification, installation qualification, operational qualification, and performance qualification.
Qualification should be conducted for all new or existing equipment, facilities, systems, and instruments by the user, with assistance from the equipment manufacturer or supplier and a qualified team of engineers. In the manufacturing process, personnel, equipment, instruments, facilities, areas, systems, or software must be qualified before moving on to the validation process.
All equipment systems should undergo qualification every 1 to 7 years from the date of the last qualification. One batch should be selected for the performance qualification of manufacturing equipment.
2. Validation:
Validation provides documentary evidence to determine the consistency of the analytical method and manufacturing process. Throughout the process, data should be collected for evaluation to determine any process that produces consistent results over time according to predetermined criteria.
Process validation is categorized into three stages: stage 1 – process design, stage 2 – process qualification, and stage 3 – continuous process verification. Validation should be performed to identify the risk assessment involved in the process and for a thorough study of the method to understand the system, process validation is necessary.
Validation should be carried out for the water system, equipment cleaning, manufacturing process, HVAC system, analytical method, computer system, and water system. For the manufacturing process, validation of three consecutive batches should be conducted.
Periodic re-validation should be performed every five years or as per the in-house validation protocol (with proper justification) with one batch in line with the process qualification requirement.
3. Calibration:
Calibration is done to ensure the correct operation of equipment or a process according to operating specifications. It should be performed periodically to identify equipment drift and ensure accuracy. Calibration is always done against a standard reference; for example, calibration of a weighing balance is done periodically against the certified value of the weighing balance.
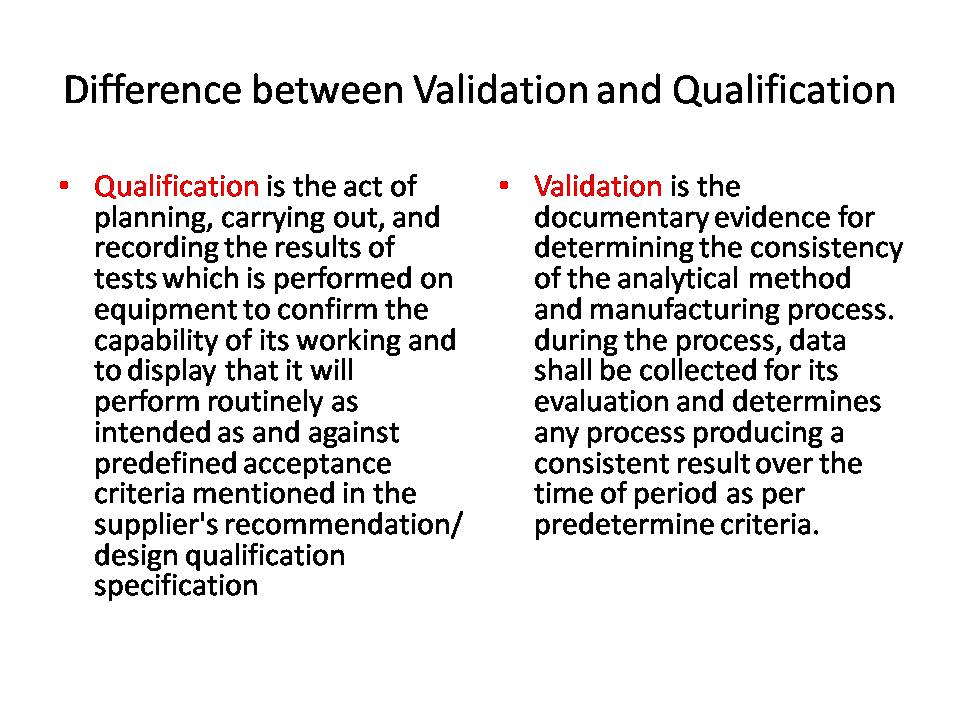
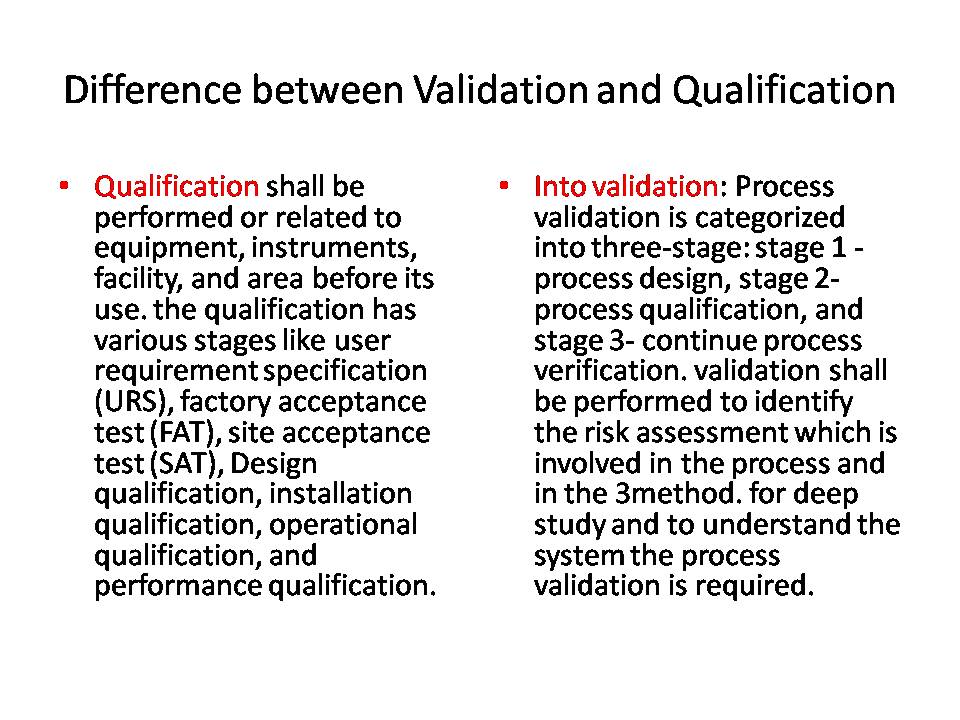
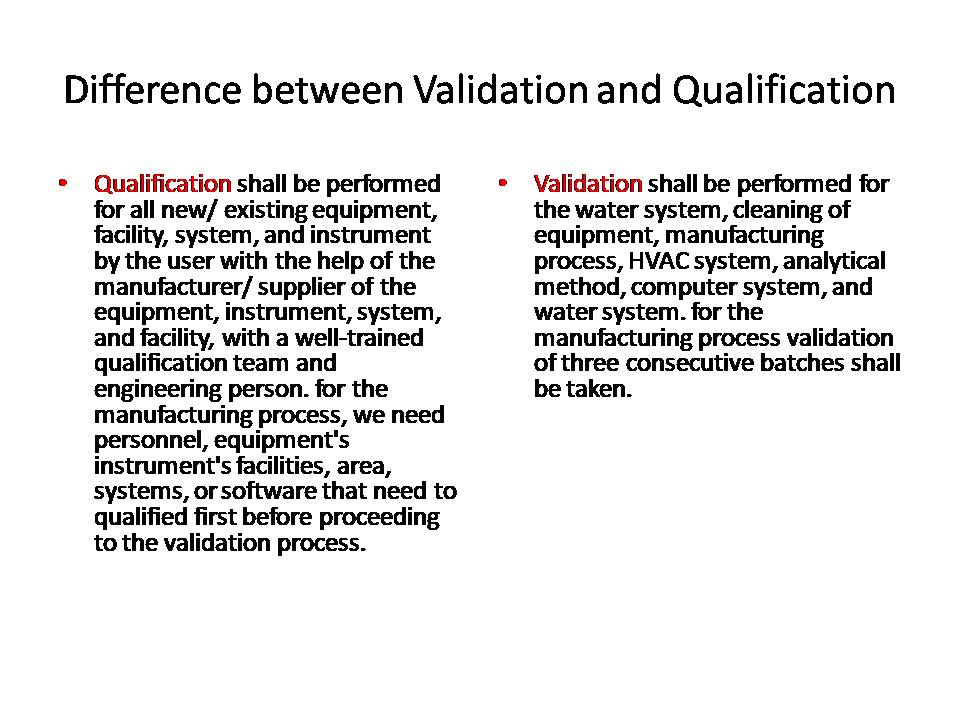

Why Validation, Calibration, and Qualification is important?
Validation, calibration, and qualification are integral parts of the quality system. Drift in any of them may lead to a loss of product quality. Therefore, it is essential to maintain them over extended periods to enhance product quality, system efficiency, safety, and meet regulatory requirements.

Naresh Bhakar is the Founder and Author at Pharmaguddu.com, bringing his extensive expertise in the field of pharmaceuticals to readers worldwide. He has experience in Pharma manufacturing and has worked with top Pharmaceuticals. He has rich knowledge and provides valuable insights and data through his articles and content on Pharmaguddu.com. For further inquiries or collaborations, please don’t hesitate to reach out via email at [email protected].
thank you