Fumigation and fogging are commonly used in pharmaceuticals to control microbial contamination in a controlled area. Fumigation is the gaseous sterilization process that kills microorganisms and prevents microbial growth in the air or on the surface of the wall/floor.
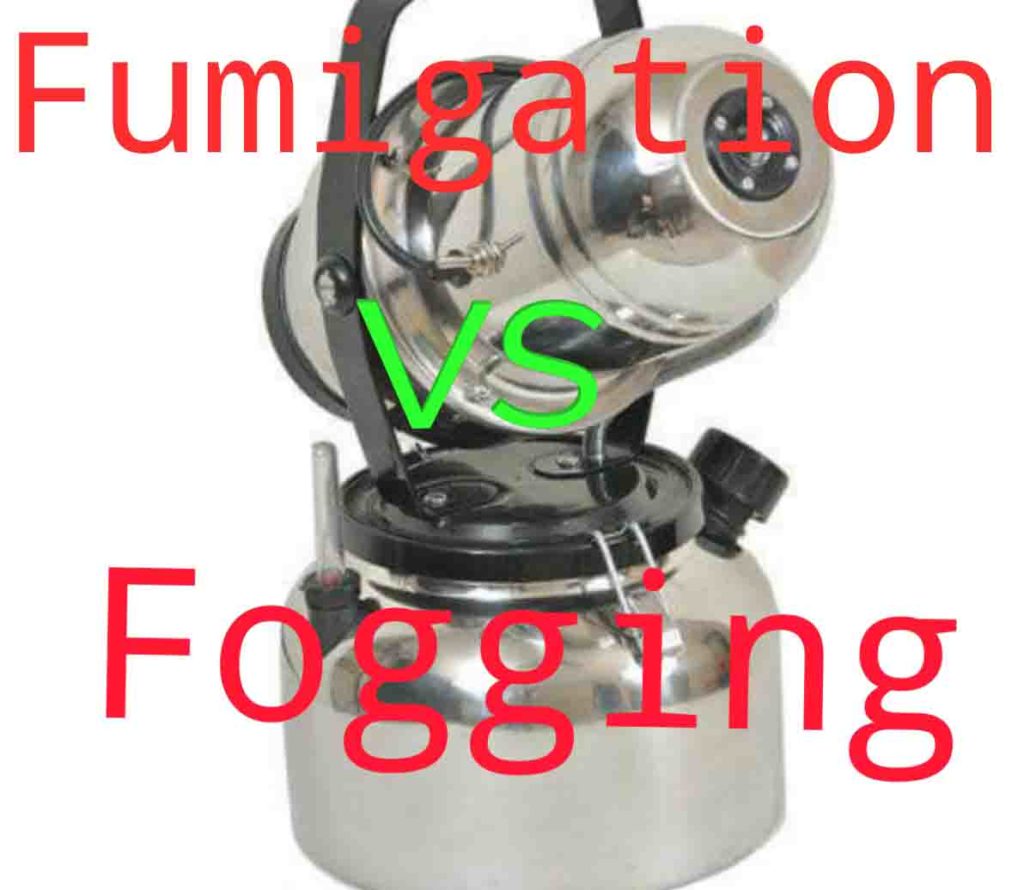
Fumigation agents, like chemicals such as formaldehyde and potassium permanganate, are often used to control micro-organisms. This technique also helps get rid of lizards, cockroaches, cobwebs, rodents, flies, and insects from the area. However, nowadays, using formaldehyde and potassium permanganate for fumigation is considered illegal by various regulatory agencies in pharmaceutical firms.
Why is formaldehyde banned in Pharmaceuticals?
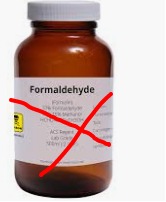
The reason for its ban is due to its cancer-causing properties and the associated risk of cancer. This applies especially to those who work with formaldehyde. Formaldehyde can also cause irritation to the eyes and nose.
Difference Between Fumigation and Fogging?
1. Fumigation:
Fumigation is the process of spraying formaldehyde and potassium in the form of liquid.
Principle of fumigation:
Formaldehyde is represented chemically as H-CHO in its pure form. It exists as a gas at room temperature, with a boiling point of -19 ℃. However, when the temperature is below 80℃, it easily undergoes polymerization to become a white solid. One of its significant polymers is paraformaldehyde (oligomer or short polymer of formaldehyde), which is a colorless substance. This substance quickly releases formaldehyde when heated. While it possesses strong bactericidal properties, its penetration power is relatively weak.
For a Effective fumigation process, the gas has been spread in the environment where bacteria are present. That’s why, in pharmaceutical industries, it’s suggested to do fumigation at a temperature above 22℃ and with a 75% relative humidity.
Advantages of fumigation:
- Fumigation controls all life stages of microorganisms because of its toxic nature.
- It is a quick way to control microorganisms, saving money and time.
- Fumigation is easy to process and reach in all areas where aerosol and spray can not reach.
- No residue problems.
Mode of action:
The mechanism of fumigation is the production of a cross-link between the proteins that interact with RNA and DNA. It acts as a mutagenic and alkylating agent that reacts with carbonyl, thiol, and hydroxyl groups.
It Requires 75% relative humidity for to be more effective ( humidity limit 60-80% and temperature 22 ℃) because gas has to dissolve in the film of moisture surrounding the bacteria.
How to Use Fumigation:
Steam can be used to increase humidity and temperature in a room up to the required limits.
- Use 500 ml formaldehyde and one liter distilled water for 28 cubic meters of area for four hours or overnight.
- Use 170 gm potassium permanganate and 500 ml formaldehyde for 28 cubic meters for four hours or overnights.
This concentration may be changed after proper validation.
2. Fogging:
Fogging uses a mixture of hydrogen peroxide and silver ion solution. It is used in pharmaceutical industries to control microbial contamination in controlled areas.
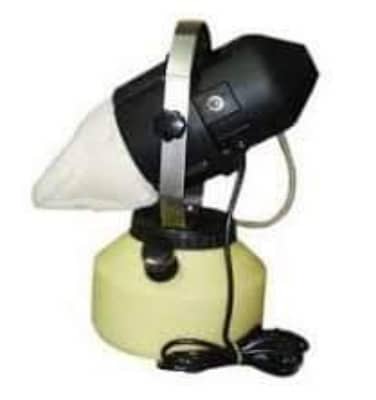
Advantages:
- These are non-toxic, eco-friendly, chlorine-free, non-mutagenic fumigating agents.
- Various formulations of H2O2 are available in the market having a concentration of 10% H2O2 with acidic pH and odorless.
- It is water-miscible and does not cost material.
How to Use Fogging:
For an area of 1000 ft3, you’ll need a solution of 20%, which means mixing 200 ml of the solution with 800 ml of demineralized water. Use a fogger to spray it for 30 minutes, and make sure the fogging rate is 130 ml per minute. Let it stay on the surface for at least one hour.
Mode of action:
It’s a powerful oxidizing agent. It helps neutralize bacteria, rendering them inactive. Virosil is a product in the market containing 10% hydrogen peroxide. The suggested concentrations for it are as follows:
- Surface disinfection (5%).
- Instrument disinfection (10%).
- Resin and filter disinfection (1 to 3%).
- Strong tank disinfection (5%).
- Laundry disinfection (10%).
But in the case of H2O2 and silver ions. It is supposed to be a safe solution for personal use. There is no requirement for de-fogging in fogging areas because no residues remain after fogging as they decompose into the water and nascent oxygen. Therefore, there is no need for cleaning and mopping equipment.
Precautions During the Fumigation and Fogging Process
- Firstly, Stop the process of operation before fumigation or fogging.
- All materials, raw materials, finished goods, intermediates, and in-process goods related to products should be removed.
- All personnel follow entry and exit procedures.
- Windows and doors should be closed. AC and AHU should be switched off before starting fumigation or fogging.
- The status label ‘Area under fumigation or fogging, Do not enter’ shall be fixed on either side of the entrance.
- Intimation of fumigation and fogging and additional rounds should be given to security.
Cleaning after Fumigation:
After Fumigation Use 70%v/v IPA solution and lint-free cloth for cleaning purposes, At the same time the wiping of external parts of equipment should be done. Clean the floor and drain point as given in the respective SOP “Cleaning and sanitization in pharmaceutical. “
Scheduling of fumigation should be done after any prolonged shutdown or during weekends and the plant’s start-up.
Validation of Fumigation in Pharmaceuticals:
Validation requires verifying the effectiveness of fumigation in pharmaceutical companies. For this, indicator-like strips of Geobacillus stearothermophilus ATCC 7953 are commonly used.
These strips are marketed with the name BIO NOVA (these are perforated s.s. coupons with spores.)
These indicators are placed at different locations, mainly in critical locations like corners and behind the instruments. After the fogging process, these strips are incubated in the MC20 growth medium provided with the biological indicator at 60±2°C for twenty-four hours.
What are the Validation Criteria for Fogging?
If the color of the MC20 growth medium changes to yellow after incubation at 60±2°C. It indicates the presence of microbes even after fogging in the strips. If no change in color. It shows the effective fumigation of the area.
De-Fumigation in Pharmaceuticals
We need to de-fumigate the area by running the AHU (air handling units) continuously for a few hours without any activity. Defumigation is necessary to clear the air of residue, and it’s important to clean the equipment after the fumigation process.
Conclusion:
Fogging is a safe and better method to control microorganisms over fumigation in pharmaceuticals. Fogging is preferred over fumigation because it is safe for personal and has no requirement for cleaning and defogging.
It kills bacteria and fungi quickly. There is no need to take extra care of residues, but in fumigation, there are requirements of regular care and keeping the area and handling equipment safe; therefore, fogging is the best choice for fumigation.
Related Topics:
- Difference between Humidity and Relative Humidity
- Moisture Content and Loss On Drying (LOD) in Pharmaceuticals
- pH Meter | Principle, Calibration, and Working
- Good Laboratory Practice (GLP) in Pharmaceutical
- High-Performance Liquid Chromatography (HPLC)
- Injectable | Parenteral | sterile preparations, types, Standard test
- Tablet Friability Test Calibration and Specification
- Pharmaceutical Sampling, types, tools ( Guidelines)
- Vernier Caliper measurement and operation in Pharma
- Handling of Laboratory Incidents in Pharma
FAQs
Ans: Due to its carcinogenic properties and associated cancer risks for personnel.
Ans: Operating air handling units continuously remove residue after fumigation.
Ans: Fumigation sprays formaldehyde, while fogging uses hydrogen peroxide and silver ion solution.
Ans: Controls microorganisms at all stages, quickly, easily, and leaves no residue problems.
Ans: Fogging uses non-toxic, eco-friendly agents like hydrogen peroxide and silver ions.
Ans: Stop operations, remove materials, follow entry procedures, close doors, and switch off AC.
Ans: Indicator strips like BIO NOVA with Geobacillus stearothermophilus verify effectiveness after fogging.

Naresh Bhakar is the Founder and Author at Pharmaguddu.com, bringing his extensive expertise in the field of pharmaceuticals to readers worldwide. He has experience in Pharma manufacturing and has worked with top Pharmaceuticals. He has rich knowledge and provides valuable insights and data through his articles and content on Pharmaguddu.com. For further inquiries or collaborations, please don’t hesitate to reach out via email at [email protected].
Appreciable. Very informative.
Good Information. Very and easy to understand